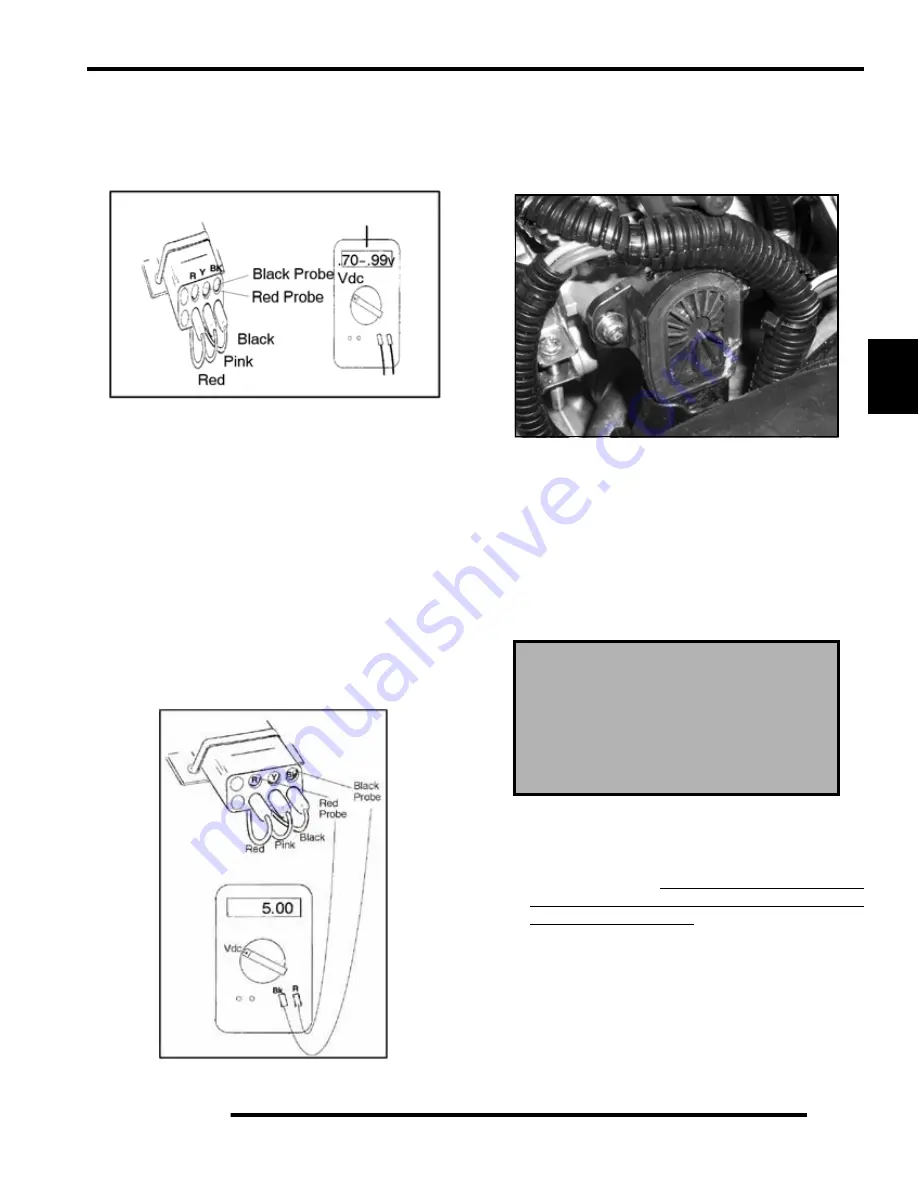
4.39
ELECTRONIC FUEL INJECTION
4
• Connect the test leads connected as shown in Figure 2
and the meter set to the “vdc” scale, move the throttle
open and closed slowly while reading the display. The
voltage should increase smoothly with no “jumps” or
decreases when the throttle is applied.
• If the TPS does not function correctly, replace it.
TPS Tester - Correct Reference Voltage
A 5 volt reference voltage signal from the test harness is
required for the TPS test to be accurate. Refer to the instructions
provided with the TPS Test Adapter Harness (
2201519
) or
follow these steps to check reference voltage.
• Harness Test: Insert black voltmeter probe into the
“Bk” test port.
• Connect the red meter probe into the “R” port and
verify the voltage is 4.99-5.01 vdc. If this reading is
low, verify the 9 volt battery is good or try a new 9 volt
battery.
Throttle Position Sensor Replacement
NOTE: The correct position of the TPS is
established and set at the factory. If the TPS is
repositioned, replaced or loosened it must be
recalibrated.
1. Remove the seat.
2. Disconnect sensor from the engine harness.
3. Loosen and rotate the throttle body (B) to gain access to the
retaining screws (if required).
4. Remove the retaining screws and replace the sensor, but do
not tighten the screws at this point.
5. Refer to “TPS Initialization” for setting the TPS voltage.
Throttle Position Sensor Initialization
Establishing a TPS setting :
This step is crucial as it sets the
TPS position using the fixed physical stop.
• Open and close throttle plate a couple of times to ensure
full throttle closing. Do not snap closed, as this could
cause unnecessary throttle plate to throttle body
interference and/or damage.
Tester 2201519
No “Jumps” in read out
The correct position of the throttle body idle
stop is established and set at the factory.
Do not loosen the throttle body idle stop or
alter the stop position in any fashion. If the
stop is repositioned, the entire throttle body
assembly must be replaced.
Summary of Contents for Ranger 500 2x4 2007
Page 1: ......
Page 20: ...1 18 GENERAL INFORMATION SAE Tap Drill Sizes Metric Tap Drill Sizes Decimal Equivalents ...
Page 82: ...3 23 ENGINE 3 Cylinder Head Exploded View EH50PL EFI Shown A A ...
Page 153: ...4 45 ELECTRONIC FUEL INJECTION 4 Fuel Pump Circuit Ignition Coil Circuit ...
Page 157: ...4 49 ELECTRONIC FUEL INJECTION 4 Diagnostic Connector Circuit ...
Page 296: ...10 10 ELECTRICAL POWER DISTRIBUTION MODULE NON EFI MODELS PDM Operation ...
Page 309: ...10 23 ELECTRICAL 10 EFI Cooling System Break Out Diagram PDM RD WH Key On 12 V Power ...
Page 332: ...10 46 ELECTRICAL Transmission Switch Circuit Differential Solenoid Circuit ...
Page 333: ...10 47 ELECTRICAL 10 Charging System Circuit Cooling Fan Circuit ...
Page 334: ...10 48 ELECTRICAL AWD Circuit ...
Page 339: ...WD 1 WIRE DIAGRAM RANGER 500 2X4 4X4 CHASSIS ...
Page 340: ...WD 2 WIRE DIAGRAM RANGER 500 2X4 4X4 DASH ...
Page 341: ...WD 3 WIRE DIAGRAM RANGER 500 EFI 4X4 CHASSIS PAGE 1 OF 2 ...
Page 342: ...WD 4 WIRE DIAGRAM RANGER 500 EFI 4X4 CHASSIS PAGE 2 OF 2 ...
Page 343: ...WD 5 WIRE DIAGRAM RANGER 500 EFI 4X4 DASH ...
Page 344: ...WD 6 WIRE DIAGRAM RANGER 500 EFI 4X4 BREAKOUTS ...
Page 345: ...WD 7 WIRE DIAGRAM RANGER 500 2X4 4X4 BREAKOUTS ...