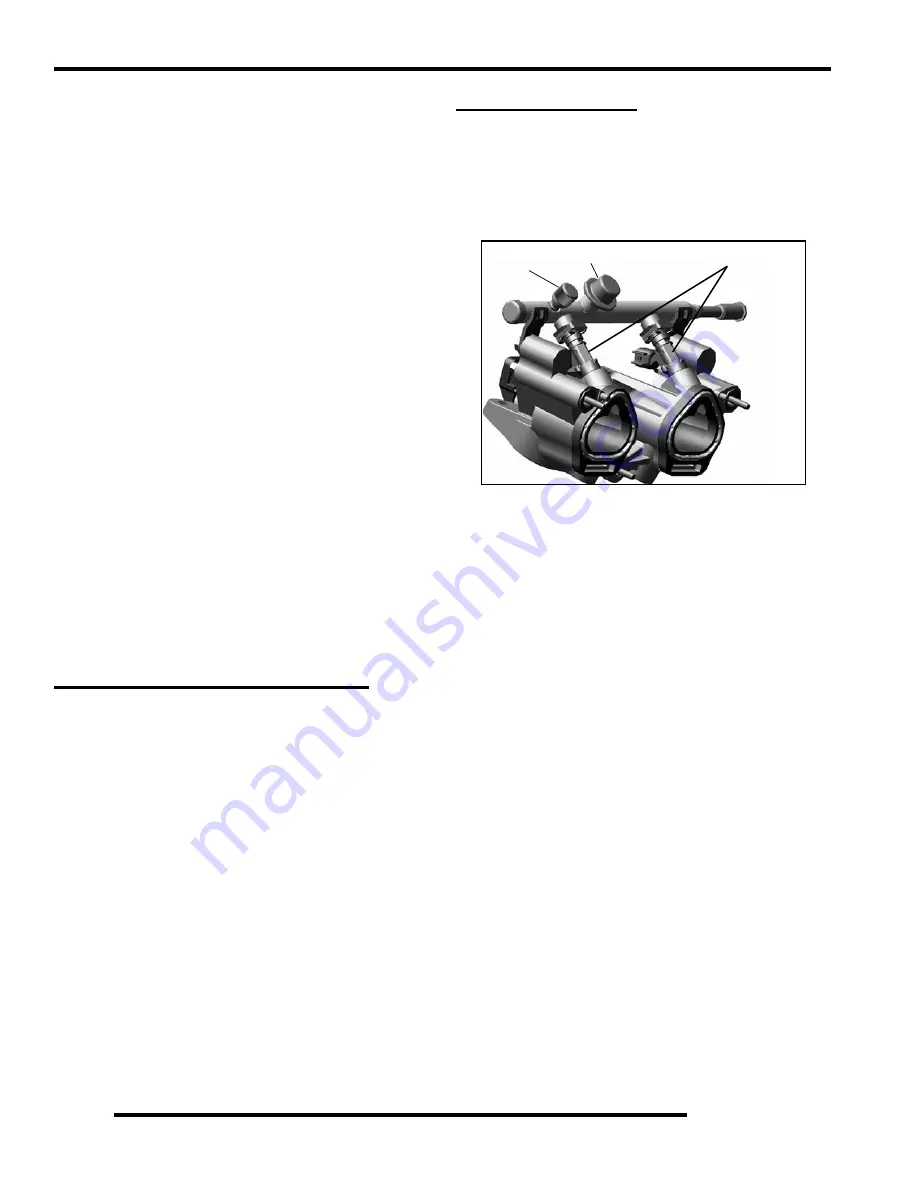
3.14
ELECTRONIC FUEL INJECTION
Fuel Pump / Fuel Tank Installation
1.
Reinstall the fuel tank assembly through the right side.
2.
Connect the fuel line to the fuel pump outlet and connect
the fuel pump electrical harness.
3.
Reinstall the vent line to the tank fitting.
4.
Install the (2) fuel tank mounting screws and tighten
securely.
5.
Install the (4) screws into the bottom portion of the right-
hand footwell.
6.
Install the front cab assembly (see Chapter 9 “Front Cab”).
7.
Remove the shop towel from the fuel tank inlet, reconnect
the fuel fill hose and tighten hose clamp securely.
8.
Install the front rack assembly (see Chapter 9 “Front
Rack”).
9.
Install the front mud guards (see Chapter 9 “Mud Guards”).
10. Reconnect the negative cable to the battery.
11. Install the upper side panels and seat (see Chapter 9 “Seat
and Side Panels”).
12. Test the fuel pump by turning on the key and listening for
the pump to activate.
FUEL PRESSURE REGULATOR
Operation Overview
The fuel pressure regulator maintains the required operating
system pressure of 43 psi ± 3 psi. A rubber-fiber diaphragm
divides the regulator into two separate sections, the fuel
chamber and the pressure regulating chamber. The pressure
regulating spring presses against the valve holder (part of the
diaphragm), pressing the valve against the valve seat. The
combination of atmospheric pressure and regulating spring
tension equals the desired operating pressure. Any time the fuel
pressure against the bottom of the diaphragm exceeds the
desired (top) pressure, the valve opens, relieving the excess
pressure, returning the excess fuel back to the tank.
Fuel Pressure Regulator Test
Refer to the “Fuel Pump Test” procedure.
Fuel Pressure Regulator Replacement
The regulator is a sealed, non-serviceable assembly. If it is
faulty, the fuel tank assembly must be replaced. Refer to the
“Fuel Pump / Tank Assembly Replacement” procedure.
FUEL INJECTORS
Operation Overview
The fuel injectors mount into the Integrated Air Fuel Manifold
(IAFM), and the fuel rail attaches to the top end of them.
Replaceable O-rings on both ends of the injector prevent
external fuel leaks and also insulate it from heat and vibration.
When the key switch is on, the fuel rail is pressurized, and the
EFI relay provides voltage to the injectors. During engine
operation, the ECU completes the ground circuit, energizing the
injectors. The valve needle in the injector is opened
electromagnetically, and the pressure in the fuel rail forces fuel
down through the inside. The “director plate” at the tip of the
injector contains a series of calibrated openings which directs
the fuel into the intake port in a cone-shaped spray pattern.
The amount of fuel injected is controlled by the ECU and
determined by the length of time the valve needle is held open,
also referred to as the “injection duration” or “pulse width”. It
may vary in length depending on the speed and load
requirements of the engine.
Fuel Injector Service
Injector problems typically fall into three general categories-
electrical, dirty / clogged, or leakage. An electrical problem
usually causes one or both of the injectors to stop functioning.
Several methods may be used to check if the injectors are
operating.
NOTE: Do not apply voltage directly to the fuel
injectors. Excessive voltage will burn out the
injectors. Do not ground the injectors with the
ignition on. The injectors will open if the EFI relay is
energized.
If an injector is not operating, it can indicate either a bad injector,
or a wiring/electrical connection problem. Check as follows:
Fuel Injectors
Pressure
Damper
Valve
PartShark.com
877-999-5686
Summary of Contents for 2009 Sportsman XP 850
Page 10: ...NOTES GENERAL INFORMATION 1 10 P a r t S h a r k c o m 8 7 7 9 9 9 5 6 8 6 ...
Page 44: ...NOTES MAINTENANCE 2 34 P a r t S h a r k c o m 8 7 7 9 9 9 5 6 8 6 ...
Page 148: ...5 56 ENGINE Balance Shaft Timing P a r t S h a r k c o m 8 7 7 9 9 9 5 6 8 6 ...
Page 154: ...NOTES ENGINE 5 62 P a r t S h a r k c o m 8 7 7 9 9 9 5 6 8 6 ...
Page 202: ...NOTES CLUTCHING PVT 7 30 P a r t S h a r k c o m 8 7 7 9 9 9 5 6 8 6 ...
Page 256: ...NOTES BODY FRAME 9 10 P a r t S h a r k c o m 8 7 7 9 9 9 5 6 8 6 ...
Page 323: ...12 31 ELECTRICAL 12 Instrument Cluster Circuit P a r t S h a r k c o m 8 7 7 9 9 9 5 6 8 6 ...
Page 327: ...12 35 ELECTRICAL 12 Battery Charging Circuits P a r t S h a r k c o m 8 7 7 9 9 9 5 6 8 6 ...
Page 329: ...12 37 ELECTRICAL 12 Constant Power Circuits P a r t S h a r k c o m 8 7 7 9 9 9 5 6 8 6 ...
Page 335: ...12 43 ELECTRICAL 12 Engine Start Command Circuits P a r t S h a r k c o m 8 7 7 9 9 9 5 6 8 6 ...
Page 338: ...12 46 ELECTRICAL AWD ADC Circuits P a r t S h a r k c o m 8 7 7 9 9 9 5 6 8 6 ...
Page 341: ...12 49 ELECTRICAL 12 Radiator Fan Circuit P a r t S h a r k c o m 8 7 7 9 9 9 5 6 8 6 ...
Page 343: ...12 51 ELECTRICAL 12 Gear Selector Switch Circuit P a r t S h a r k c o m 8 7 7 9 9 9 5 6 8 6 ...
Page 356: ...WD 20 WIRE DIAGRAM 2009 SPORTSMAN XP 850 INTL EFI P a r t S h a r k c o m 8 7 7 9 9 9 5 6 8 6 ...
Page 358: ...WD 24 WIRE DIAGRAM 2009 SPORTSMAN XP 850 INTL EPS P a r t S h a r k c o m 8 7 7 9 9 9 5 6 8 6 ...
Page 367: ...WD 5 WIRE DIAGRAM 2009 SPORTSMAN XP 850 AWD ADC P a r t S h a r k c o m 8 7 7 9 9 9 5 6 8 6 ...
Page 374: ...WD 19 WIRE DIAGRAM 2009 SPORTSMAN XP 850 EFI P a r t S h a r k c o m 8 7 7 9 9 9 5 6 8 6 ...
Page 376: ...WD 23 WIRE DIAGRAM 2009 SPORTSMAN XP 850 EPS P a r t S h a r k c o m 8 7 7 9 9 9 5 6 8 6 ...