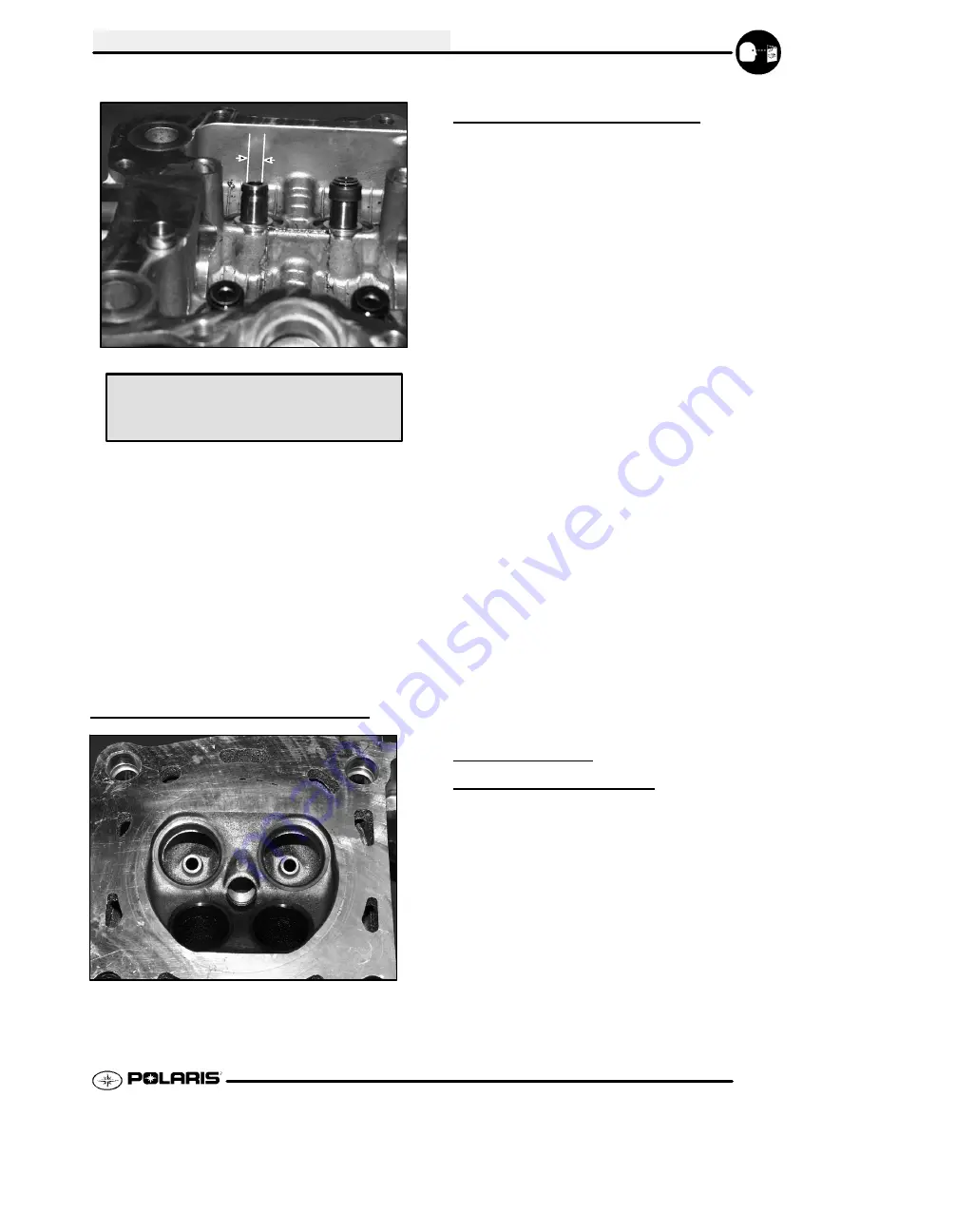
GENERAL INFORMATION
3.23
Valve Guide I.D.:
.2362-.2367
I
(6.0-6.012 mm)
6. Measure valve guide inside diameter at the top
middle and end of the guide using a small hole
gauge and a micrometer.
Measure in two
directions, front to back and side to side.
7. Subtract valve stem measurement to obtain stem
to guide clearance.
NOTE:
Be sure to measure
each guide and valve combination individually.
8. Replace valve and/or guide if clearance is
excessive. Compare to specifications.
NOTE:
If valve guides are replaced, valve seats
must be reconditioned.
Refer to Valve Seat
Reconditioning for procedure.
COMBUSTION CHAMBER
Clean all accumulated carbon deposits from
combustion chamber and valve seat area with a soft
wire brush.
VALVE SEAT SERVICE
Valve Seat Inspection
Inspect valve seat in cylinder head for pitting, burnt
spots, roughness, and uneven surface. If any of the
above conditions exist, the valve seat must be
reconditioned. See Valve Seat Reconditioning, Page
3.25.
If the valve seat is cracked the cylinder head
must be replaced.
Cylinder Head Reconditioning
NOTE:
Servicing the valve guides and valve seats
requires special tools and a thorough knowledge of
reconditioning techniques. Follow the instructions
provided in the cylinder head service tool kit.
CAUTION:
Wear eye protection when performing
cylinder head service. Valve guide replacement will
require heating of the cylinder head. Wear gloves to
prevent burns.
Valve Guide Removal/Installation
1. Remove all carbon deposits from the combustion
chamber, valve seat and valve guide area before
attempting to remove valve guides.
CAUTION:
Carbon deposits are extremely abrasive and may
damage the valve guide bore when guides are
removed.
2. Place new valve guides in a freezer for at least 15
minutes while heating cylinder head.
3. Heat cylinder head in an oven or use a hot plate to
bring cylinder head temperature to 212
°
F (100
°
C).
CAUTION:
Do not use a torch to heat
cylinder head or warpage may result from uneven
heating. Head temperature can be checked with
a pyrometer or a welding temperature stick.
VALVE SEAT
RECONDITIONING
Follow the manufacturers instructions provided with
the valve seat cutters in the Valve Seat
Reconditioning Kit (
PN 2200634
). Abrasive stone
seat reconditioning equipment can also be used.
Keep all valves in order with their respective seat.
Summary of Contents for 2004-2005 Sportsman 6x6
Page 1: ...SPORTSMAN 6X6 6 59 0 18 31 504 SPORTSMAN 6X6 6 59 0 18 31 504...
Page 58: ...MAINTENANCE 2 38 NOTES...
Page 78: ...GENERAL INFORMATION 3 20 CYLINDER HEAD EXPLODED VIEW EH50PL EH50PL...
Page 126: ...GENERAL INFORMATION 4 14 NOTES...
Page 142: ...GENERAL INFORMATION 5 16 NOTES...
Page 198: ...GENERAL INFORMATION 7 30 NOTES...
Page 276: ...ELECTRICAL 10 48 NOTES...
Page 277: ...ELECTRICAL WIRING DIAGRAM 2004 SPORTSMAN 6X6...
Page 278: ...ELECTRICAL WIRING DIAGRAM 2004 SPORTSMAN 6X6 NOTES...
Page 279: ...ELECTRICAL WIRING DIAGRAM 2005 SPORTSMAN 6X6 BUILT BEFORE JULY 12 2004...
Page 280: ...ELECTRICAL WIRING DIAGRAM 2005 SPORTSMAN 6X6 BUILT BEFORE JULY 12 2004 NOTES...
Page 281: ...ELECTRICAL WIRING DIAGRAM 2005 SPORTSMAN 6X6 BUILT AFTER JULY 12 2004...
Page 282: ...ELECTRICAL WIRING DIAGRAM 2005 SPORTSMAN 6X6 BUILT AFTER JULY 12 2004 NOTES...
Page 289: ...31 504 3ULQWHG LQ 86...