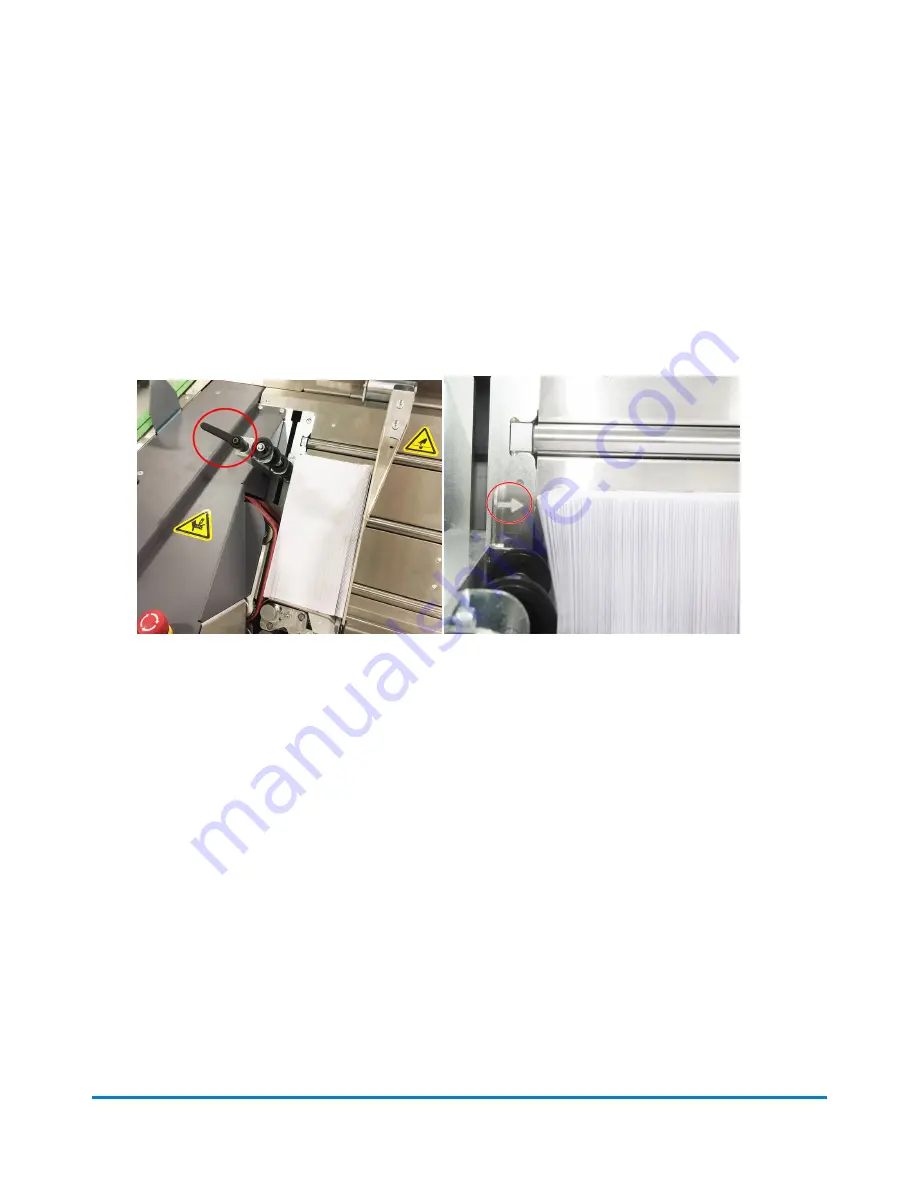
Adjusting the Envelope Fence
The envelope fence supports the envelopes at the feed head and also keeps the envelopes aligned with
the feed head.
1. Load a stack of envelopes (flap down and facing to the right) in the envelope hopper.
2. Loosen the lock down lever and slide the envelope fence up or down until the alignment arrow
lines up with the top edge of the envelopes.
Loosen Lever and Use Alignment Arrows
3. When the fence is properly positioned, lock it in place.
Operator Adjustments
Pitney Bowes
Epic Select Operator Guide
December, 2017
Page 55 of 288
Summary of Contents for Epic
Page 27: ...3 Power the System On and Off In this section Power Up the System 22 Power Down the System 24 ...
Page 32: ...This page intentionally left blank ...
Page 193: ......
Page 224: ...This page intentionally left blank ...
Page 236: ...This page intentionally left blank ...
Page 250: ...This page intentionally left blank ...