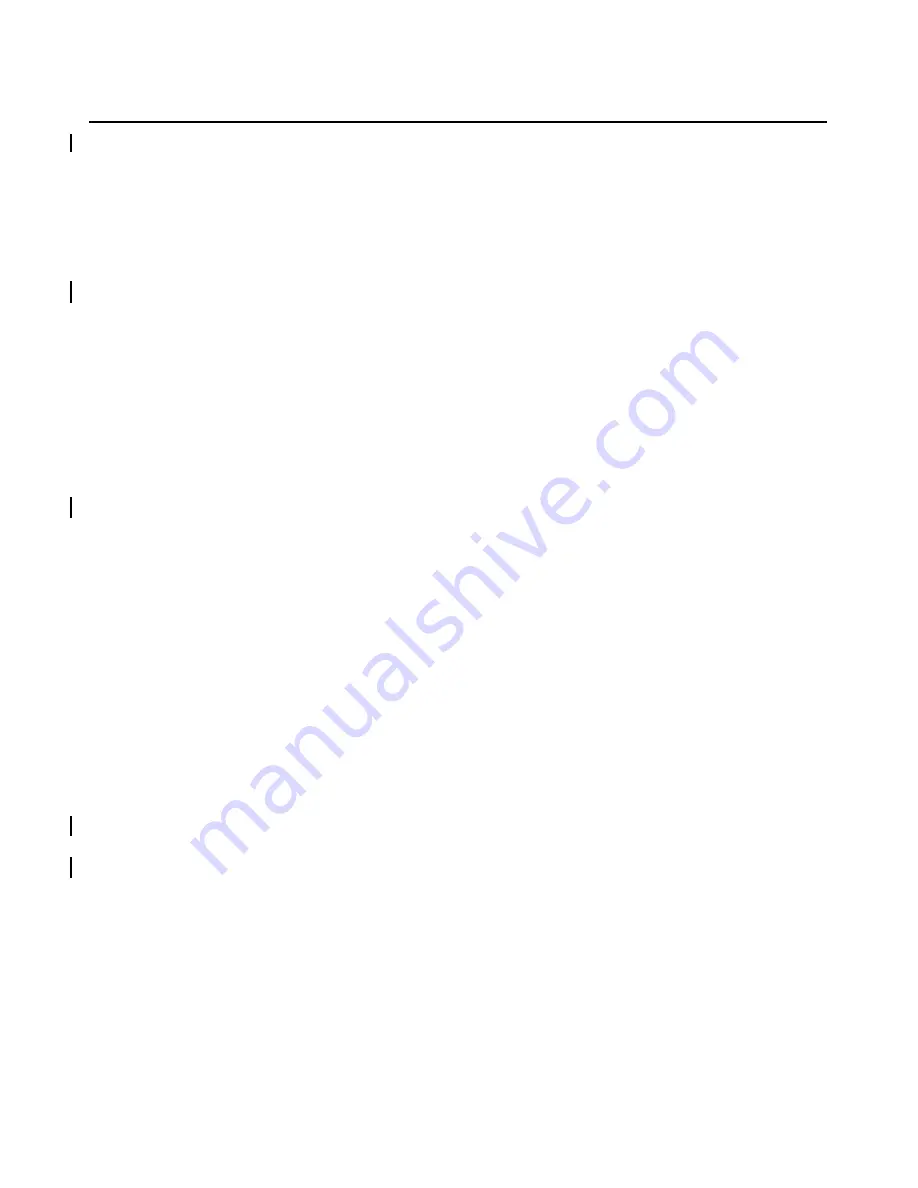
RIGGING AND ADJUSTMENT OF AILERON CONTROLS. (Refer to Figure 27-10.)
1. To check and adjust the rigging of the aileron controls:
A.
Insure that the flaps are adjusted and rigged properly, and in their up locked position.
2. Check that the control wheels are properly adjusted and in their neutral position. Place the tee bar in
the full forward position and maintain in this position by use of a suitable tool.
3 . Check that both bellcranks are at their neutral positions. The neutral position is obtained when the
f o rward and aft cable connection holes on the bellcrank are an equal distance from the adjacent
o u tboard wing rib. Rigging tools, as shown in Figure 27-9 may be fabricated to hold the bellcranks in
their neutral positions. A snug fit of the tool is required between the bellcrank arms and ribs, which
may necessitate loosening a primary or balance cable. Refer to Chapter 91 for tool fabrication details.
4. With the aileron control rod connected between the bellcrank and aileron, check that the trailing edge
of the aileron is even with the trailing outboard edge of the flaps. This is the aileron neutral position.
The ailerons may be allowed to droop by approximately 0.125 of an inch at this point.
5. Should the two trailing edges (aileron and flap) not align, disconnect the aileron control push rod from
the bellcrank and aileron, loosen the jam nuts at each rod end, and adjust the rod ends to obtain t r a i l i n g
edge alignment. Apply a slight up pressure against the trailing edge of the aileron while making this
adjustment. Check that there is sufficient thread engagement at both rod ends. Any adjustment should
be distributed between both rod ends.
6. Adjust the primary and balance cable tension as given in Figure 27-10 by the following procedure:
A.
Remove the two front seats if desired, and the bottom of the rear seat to facilitate in the necessary
operation.
B.
Loosen the connecting bolts of the idler crossover sprockets at the control tee bar to allow the
chain to fit snug around the control wheel sprockets and over the idler sprockets, then tighten
bolts.
C.
Ascertain that both bellcranks are at their neutral position.
D.
Adjust the turnbuckles (located in the access opening just aft of the main spar) of the primary and
balance cables to their proper cable tension and maintain neutral position of the control wheels.
To obtain neutral position of both control wheels, it may also be necessary to adjust the roller
chain turnbuckle located between the control wheel sprockets. Finish the adjustment with even
tension on all cables and remove any rigging tools.
7. Check control operation to insure that the left aileron up and right aileron down stops are contacted
simultaneously and vice versa. Adjust the stops as required.
8. Rotate the left control wheel in each direction until the bellcranks contact the stops. The sprocket
stops on the tee bar should not be contacted until additional “override” movement (cushion) of 0.030
to 0.040 is obtained between the sprocket pin and adjustable stop bolts. (Refer to Figure 27-6.)
9. Place the ailerons in the neutral position (aligned with flaps). Check that the up and down travels of
each aileron from neutral position is in accordance with specifications given in Figure 27-10. When
measuring these travels maintain a light up or down pressure just sufficient to remove the slack
between the bellcrank and aileron. Total free play at the aileron trailing edge should not exceed 0.120
of an inch.
1 0 . Should an out-of-trim condition persist despite all rigging corrections that can be made, there is a
p o ssibility that the trailing edge of the aileron has been used to move the aircraft forward. This can
result in a slight bulging of the aileron contour at the trailing edge which will cause an out-of-rig con-
dition that is very difficult to correct.
PIPER AIRCRAFT
PA - 4 4 - 1 8 0 / 1 8 0 T
AIRPLANE MAINTENANCE MANUAL
27-10-05
Page 27-19
Revised: June 20, 1995
1K21
Summary of Contents for SEMINOLE PA-44-180
Page 38: ...CHAPTER DIMENSIONS AND AREAS 1B14...
Page 49: ...CHAPTER LIFTING AND SHORING 1C1...
Page 53: ...CHAPTER LEVELING AND WEIGHING 1C5...
Page 58: ...CHAPTER TOWING AND TAXIING 1C10...
Page 62: ...CHAPTER PARKING AND MOORING 1C14...
Page 65: ...CHAPTER REQUIRED PLACARDS 1C17...
Page 70: ...CHAPTER SERVICING 1C22...
Page 98: ...CHAPTER STANDARD PRACTICES AIRFRAME 1E2...
Page 108: ...CHAPTER ENVIRONMENTAL SYSTEM 1E12...
Page 189: ...CHAPTER AUTOFLIGHT 1H21...
Page 192: ...CHAPTER COMMUNICATIONS 1H24...
Page 202: ...CHAPTER ELECTRICAL POWER 1I10...
Page 228: ...CHAPTER EQUIPMENT FURNISHINGS 1J12...
Page 233: ...CHAPTER FIRE PROTECTION 1J17...
Page 238: ...CHAPTER FLIGHT CONTROLS 1J24...
Page 304: ...2A18 CHAPTER FUEL...
Page 325: ...2B17 CHAPTER HYDRAULIC POWER...
Page 357: ...2D1 CHAPTER ICE AND RAIN PROTECTION...
Page 414: ...CHAPTER LANDING GEAR 2F13...
Page 479: ...2I6 CHAPTER LIGHTS...
Page 488: ...2I16 CHAPTER NAVIGATION AND PITOT STATIC...
Page 503: ...2J7 CHAPTER OXYGEN...
Page 524: ...2K6 CHAPTER VACUUM...
Page 535: ...2K19 CHAPTER ELECTRICAL ELECTRONIC PANELS AND MULTIPURPOSE PARTS...
Page 546: ...INTENTIONALLY LEFT BLANK PA 44 180 180T AIRPLANE MAINTENANCE MANUAL 2L6 PIPER AIRCRAFT...
Page 547: ...2L7 CHAPTER STRUCTURES...
Page 582: ...CHAPTER DOORS 3A18...
Page 593: ...CHAPTER STABILIZERS 3B8...
Page 604: ...CHAPTER WINDOWS 3B22...
Page 611: ...CHAPTER WINGS 3C10...
Page 624: ...CHAPTER PROPELLER 3D1...
Page 643: ...CHAPTER POWER PLANT 3D21...
Page 667: ...CHAPTER ENGINE FUEL SYSTEM 3F1...
Page 681: ...CHAPTER IGNITION 3F16...
Page 712: ...CHAPTER ENGINE INDICATING 3H1...
Page 730: ...CHAPTER EXHAUST 3H19...
Page 734: ...CHAPTER OIL 3I1...
Page 743: ...CHAPTER STARTING 3I11...
Page 755: ...CHAPTER TURBINES 3J1...