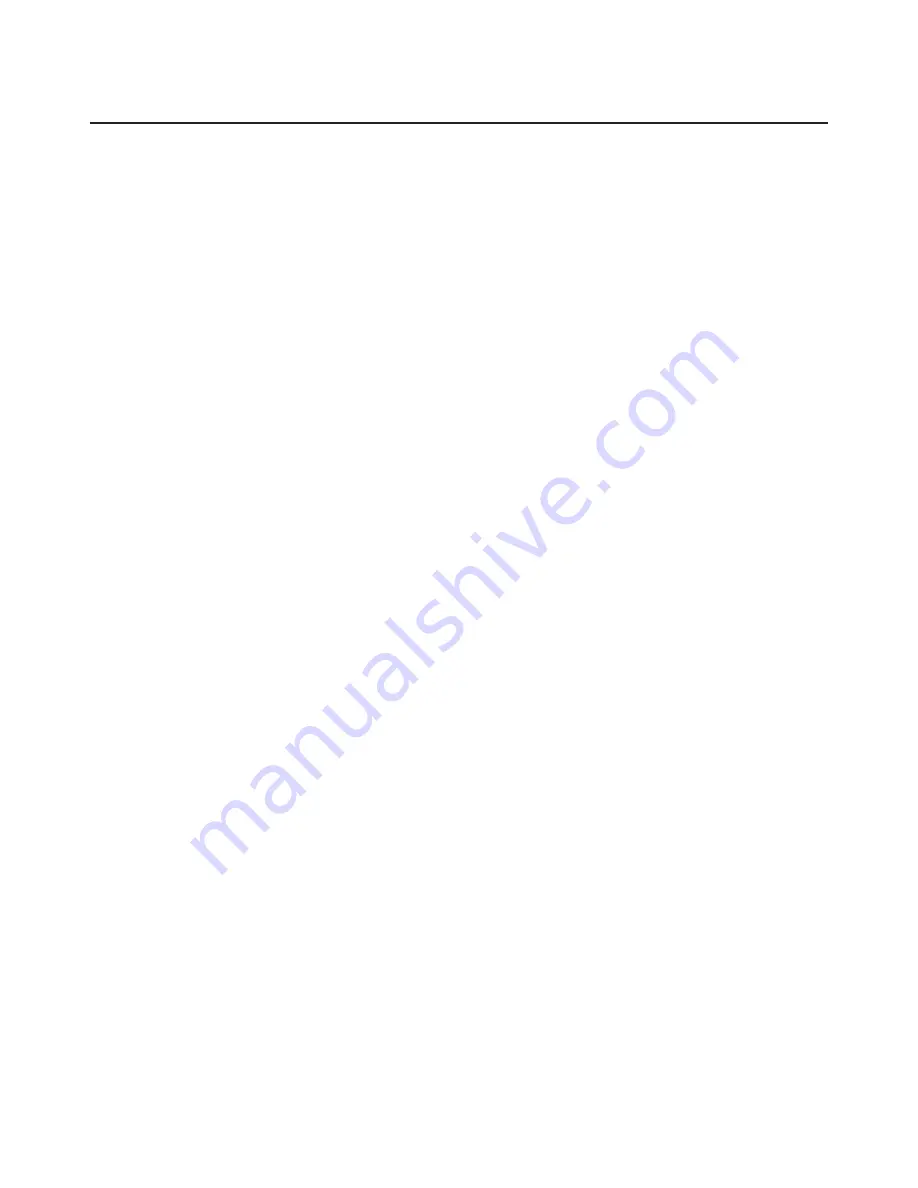
BRUSH HOLDERS.
1. To test brush holders, touch one test probe to the brush plate and the other to each brush holder.
2. The test lamp should light when the grounded brush holders are touched and should not light when the
insulated brush holders are touched.
GEAR AND PINION HOUSING.
Inspect housings for cracks and bearings for excessive wear. Remove rust, paint or grease from mounting
surfaces.
BENDIX DRIVE.
The Bendix Drive should be wiped clean with a dry cloth. The pinion should turn smoothly in one direc-
tion and should lock in the other direction. Replace drive if it fails to check as above or if the pinion teeth
are excessively worn or damaged.
ASSEMBLY OF STARTING MOTOR.
1. When assembling the starting motor, always use an arbor press and the proper bearing arbor for
installing graphitized bronze and roller bearings. The Bendix shaft should have a thin film of
Lubriplate #777 or equivalent on the Bendix portion of the shaft. End play should be .005 to .050 of an
inch.
2. New brushes should be properly seated when installing by wrapping a strip of 00 sandpaper around
the commutator (with the sanding side out) 1-1/4 to 1-1/2 times maximum. Drop brushes on sandpaper
covered commutator and turn the armature slowly in the direction of rotation. Dust should be blown
out of the motor after sanding.
– NOTE –
The spring tension is 32 to 40 ounces with new brushes. This
tension is measured with the scale hooked under the brush
spring near the brush and the reading is taken at right angles
to the line of force exerted by the brush spring.
3. Check the position of the pinion to be sure the unit will mesh properly with the flywheel ring gear. See
BENCH TEST.
1. After the starting motor is reassembled, it should be tested to see that the no-load current at a certain
voltage is within specifications as given in Starting Motor Service Test Specifications. To make this
make sure there is no binding or interference. Two or three sharp raps on the frame with a rawhide
hammer will often help to align the bearings and free the armature.
2. If no difficulty is indicated in the above test, a stall torque test may be made to see if the starting
motor is producing its rated cranking power. Make test connections as shown in Figure 6.
3. If torque and current are not within specifications, check the seating of the brushes and internal con-
nections for high resistance. If these checks are made and found to be in good order, replace frame and
field assembly and retest starter.
PIPER AIRCRAFT
PA-32R-301/301T
MAINTENANCE MANUAL
80-10-00
Page 80-8
Reissued: July 1, 1993
4D18
Summary of Contents for PA-32R-301T SARATOGA S
Page 26: ...CHAPTER 4 AIRWORTHINESS LIMITATIONS 1C1 ...
Page 29: ...CHAPTER 5 TIME LIMITS MAINTENANCE CHECKS 1C4 ...
Page 53: ...CHAPTER 6 DIMENSIONS AND AREAS 1D6 ...
Page 64: ...CHAPTER 7 LIFTING AND SHORING 1D21 ...
Page 68: ...CHAPTER 8 LEVELING AND WEIGHING 1E1 ...
Page 72: ...CHAPTER 9 TOWING AND TAXIING 1E5 ...
Page 76: ...CHAPTER 10 PARKING AND MOORING 1E9 ...
Page 80: ...CHAPTER 11 REQUIRED PLACARDS 1E13 ...
Page 92: ...CHAPTER 12 SERVICING 1F1 ...
Page 126: ...CHAPTER 20 STANDARD PRACTICES AIRFRAME 1G17 ...
Page 127: ...THIS PAGE INTENTIONALLY LEFT BLANK ...
Page 139: ...CHAPTER 21 ENVIRONMENTAL SYSTEMS 1H5 ...
Page 188: ...CHAPTER 22 AUTOFLIGHT 1J7 ...
Page 193: ...CHAPTER 23 COMMUNICATIONS 1J12 ...
Page 203: ...CHAPTER 24 ELECTRICAL POWER 1J22 ...
Page 263: ...CHAPTER 25 EQUIPMENT FURNISHINGS 2A13 ...
Page 269: ...CHAPTER 27 FLIGHT CONTROLS 2A20 ...
Page 332: ...CHAPTER 28 FUEL 2D11 ...
Page 363: ...CHAPTER 29 HYDRAULIC POWER 2E18 ...
Page 404: ...CHAPTER 30 ICE AND RAIN PROTECTION 2G16 ...
Page 470: ...CHAPTER 32 LANDING GEAR 3A13 ...
Page 550: ...CHAPTER 33 LIGHTS 3D24 ...
Page 562: ...CHAPTER 34 NAVIGATION AND PITOT STATIC 3E12 ...
Page 582: ...CHAPTER 35 OXYGEN 3F8 ...
Page 604: ...CHAPTER 37 VACUUM 3G6 ...
Page 616: ...CHAPTER 39 3G18 ELECTRIC ELECTRONIC PANELS MULTIPURPOSE PARTS ...
Page 620: ...CHAPTER 51 STRUCTURES 3G22 ...
Page 636: ...CHAPTER 52 DOORS 3H14 ...
Page 650: ...CHAPTER 55 STABILIZERS 3I4 ...
Page 662: ...CHAPTER 56 WINDOWS 3I16 ...
Page 670: ...CHAPTER 57 WINGS 3I24 ...
Page 688: ...CHAPTER 61 PROPELLER 3J18 ...
Page 704: ...CHAPTER 70 STANDARD PRACTICES ENGINES 3K10 ...
Page 708: ...CHAPTER 71 POWER PLANT 3K14 ...
Page 737: ...CHAPTER 73 ENGINE FUEL SYSTEM 4A13 ...
Page 749: ...CHAPTER 74 IGNITION 4B1 ...
Page 783: ...CHAPTER 77 ENGINE INDICATING 4C11 ...
Page 793: ...CHAPTER 78 EXHAUST 4C21 ...
Page 801: ...CHAPTER 79 OIL 4D5 ...
Page 805: ...CHAPTER 80 STARTING 4D9 ...
Page 819: ...CHAPTER 81 TURBINES 4D23 ...
Page 833: ...CHAPTER 91 CHARTS WIRING DIAGRAMS 4E13 ...