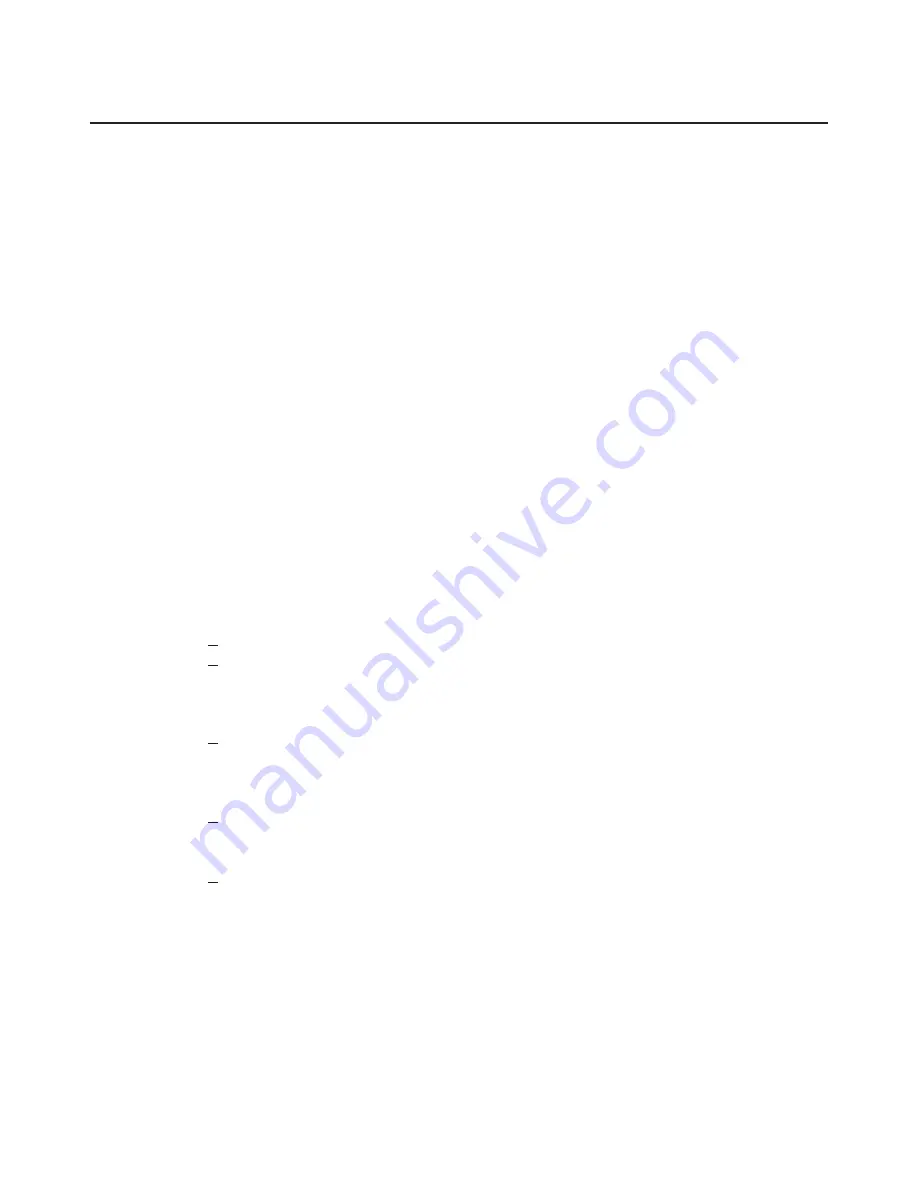
PROPELLER DEICING SYTEM (Cont.)
E INSPECTION (Cont.)
(2) 100 HOUR INSPECTION (Cont.)
(a)Remove cowling.
(b) Conduct 50 hour inspection.
(c) Check for radio noise or radio compass interference by operating engine at near takeoff
power with radio gear ON while turning deicer switch ON and OFF. If noise or interference
occurs with deicer switch ON, and disappears when switch is OFF, see troubleshooting chart.
(d) Ascertain that all clamps, clips, mountings and electrical connections are tight. Check for
loose, broken or missing safety wire.
(e) Deicers: Closely check deicers for wrinkled, loose or torn areas, particularly around outboard
end and especially where strap passes under strap retainer. Look for abrasion or cuts, espe-
cially along leading edge and flat or thrust face. If heater wires are exposed in damaged areas
or if rubber is found to be tacky, swollen or deteriorated (as from oil or solvent contact),
replace damaged deicer in accordance with Installation of Deicer.
– NOTE –
Check that strap restrainers are correctly located and secure.
Look for cracks or other damage. Operate propeller from full
pitch to low pitch and check that deicer lead straps do not
come under tension, or are pinched by propeller blade.
(f) Slip Rings: Check slip rings for gouges, roughened surface, cracks, burned or discolored
areas and for deposits of oil, grease or dirt.
1 Clean greasy or contaminated slip rings with CRC2-26 solvent.
2 If uneven wear is found or if wobble is noticed, set up dial indicator as shown in figure
30-9 to check alignment of slip rings to propeller shaft.
(g) Brush Block - Brushes: Examine mounting brackets and housing for cracks, deformation or
other physical damage.
1 Test that each brush rides fully on its slip ring over 360. Figure 10 shows wear pattern if
this condition is not corrected. If alignment is off, shim where brush block bracket
attaches to engine back bone or pivot at support arm which is attached to generator idler
pulley bracket.
2 Check for proper clearance of brush block to slip rings as shown in Figure 12. If not cor-
rect, loosen mounting screws and move in elongated holes to correct block position
before tightening securely.
3 Visually check brush block for approximately 2 angle of attack. (Refer to Figure 12.) If
not, loosen mounting screws and twist block, but be sure to hold clearance limits shown
when tightening.
(h) System Wiring: With deicer system operating, have assistant observe ammeter while visually
inspecting and physically flexing wiring from brush blocks through firewall, to timer, to
ammeter, to switch and to aircraft power supply. The ammeter will flicker as the timer
switches approxi- mately every 90 seconds in cycle. Jumps or flickers at other times indi-
cates loose or broken wiring in area under examination at that moment. In such case, check
continuity through affected harness, while flexing and prodding each wire in area that gave
inital indication of trouble. Use wiring diagram in Chapter 91 to trace circuitry.
PIPER AIRCRAFT
PA-32R-301/301T
MAINTENANCE MANUAL
30-60-00
Page 30-35
Reissued: July 1, 1993
2I5
Summary of Contents for PA-32R-301T SARATOGA S
Page 26: ...CHAPTER 4 AIRWORTHINESS LIMITATIONS 1C1 ...
Page 29: ...CHAPTER 5 TIME LIMITS MAINTENANCE CHECKS 1C4 ...
Page 53: ...CHAPTER 6 DIMENSIONS AND AREAS 1D6 ...
Page 64: ...CHAPTER 7 LIFTING AND SHORING 1D21 ...
Page 68: ...CHAPTER 8 LEVELING AND WEIGHING 1E1 ...
Page 72: ...CHAPTER 9 TOWING AND TAXIING 1E5 ...
Page 76: ...CHAPTER 10 PARKING AND MOORING 1E9 ...
Page 80: ...CHAPTER 11 REQUIRED PLACARDS 1E13 ...
Page 92: ...CHAPTER 12 SERVICING 1F1 ...
Page 126: ...CHAPTER 20 STANDARD PRACTICES AIRFRAME 1G17 ...
Page 127: ...THIS PAGE INTENTIONALLY LEFT BLANK ...
Page 139: ...CHAPTER 21 ENVIRONMENTAL SYSTEMS 1H5 ...
Page 188: ...CHAPTER 22 AUTOFLIGHT 1J7 ...
Page 193: ...CHAPTER 23 COMMUNICATIONS 1J12 ...
Page 203: ...CHAPTER 24 ELECTRICAL POWER 1J22 ...
Page 263: ...CHAPTER 25 EQUIPMENT FURNISHINGS 2A13 ...
Page 269: ...CHAPTER 27 FLIGHT CONTROLS 2A20 ...
Page 332: ...CHAPTER 28 FUEL 2D11 ...
Page 363: ...CHAPTER 29 HYDRAULIC POWER 2E18 ...
Page 404: ...CHAPTER 30 ICE AND RAIN PROTECTION 2G16 ...
Page 470: ...CHAPTER 32 LANDING GEAR 3A13 ...
Page 550: ...CHAPTER 33 LIGHTS 3D24 ...
Page 562: ...CHAPTER 34 NAVIGATION AND PITOT STATIC 3E12 ...
Page 582: ...CHAPTER 35 OXYGEN 3F8 ...
Page 604: ...CHAPTER 37 VACUUM 3G6 ...
Page 616: ...CHAPTER 39 3G18 ELECTRIC ELECTRONIC PANELS MULTIPURPOSE PARTS ...
Page 620: ...CHAPTER 51 STRUCTURES 3G22 ...
Page 636: ...CHAPTER 52 DOORS 3H14 ...
Page 650: ...CHAPTER 55 STABILIZERS 3I4 ...
Page 662: ...CHAPTER 56 WINDOWS 3I16 ...
Page 670: ...CHAPTER 57 WINGS 3I24 ...
Page 688: ...CHAPTER 61 PROPELLER 3J18 ...
Page 704: ...CHAPTER 70 STANDARD PRACTICES ENGINES 3K10 ...
Page 708: ...CHAPTER 71 POWER PLANT 3K14 ...
Page 737: ...CHAPTER 73 ENGINE FUEL SYSTEM 4A13 ...
Page 749: ...CHAPTER 74 IGNITION 4B1 ...
Page 783: ...CHAPTER 77 ENGINE INDICATING 4C11 ...
Page 793: ...CHAPTER 78 EXHAUST 4C21 ...
Page 801: ...CHAPTER 79 OIL 4D5 ...
Page 805: ...CHAPTER 80 STARTING 4D9 ...
Page 819: ...CHAPTER 81 TURBINES 4D23 ...
Page 833: ...CHAPTER 91 CHARTS WIRING DIAGRAMS 4E13 ...