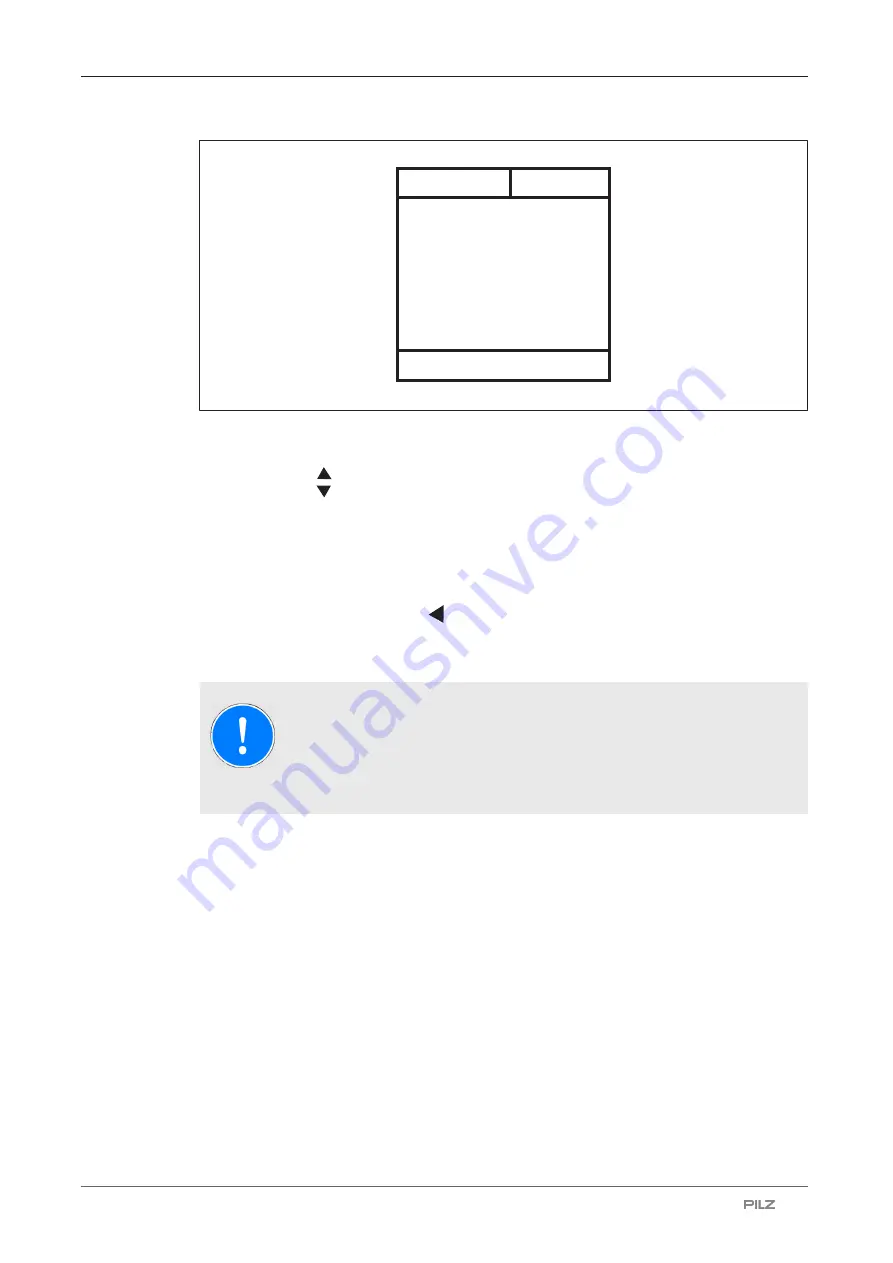
Commissioning
Operating Manual PSENvip RL D P Set
1001641-EN-09
| 81
SYSTEM OK
OSSD OFF
SETUP
Overrun: 10 mm
Fig.: Enter overrun
}
Using the keys
, select the overrun that is specified on the type label of the press
brake.
The permitted value range is 2 ... 14 mm, in 2 mm steps.
}
Finish the entry using the <ENTER> key.
The PSENvip prompts you to confirm that you accept the new overrun:
}
Within 3 seconds, press the key
.
}
You can exit the menu at any time without confirming the entry by pressing <ESC>. In
this case, the previous value for the overrun will be retained.
NOTICE
Once the overrun has been entered, you will have to perform a function test
on the safety device (see section entitled "Function test of the safety
device").
7.5
Check protective equipment
Tests are used for early identification of defects on the press brake and its safeguards.
They help to maintain a safe, working condition, i.e. to prevent accidents.
The test of the protective equipment consists of:
}
A function test using the test piece
and
}
a visual inspection