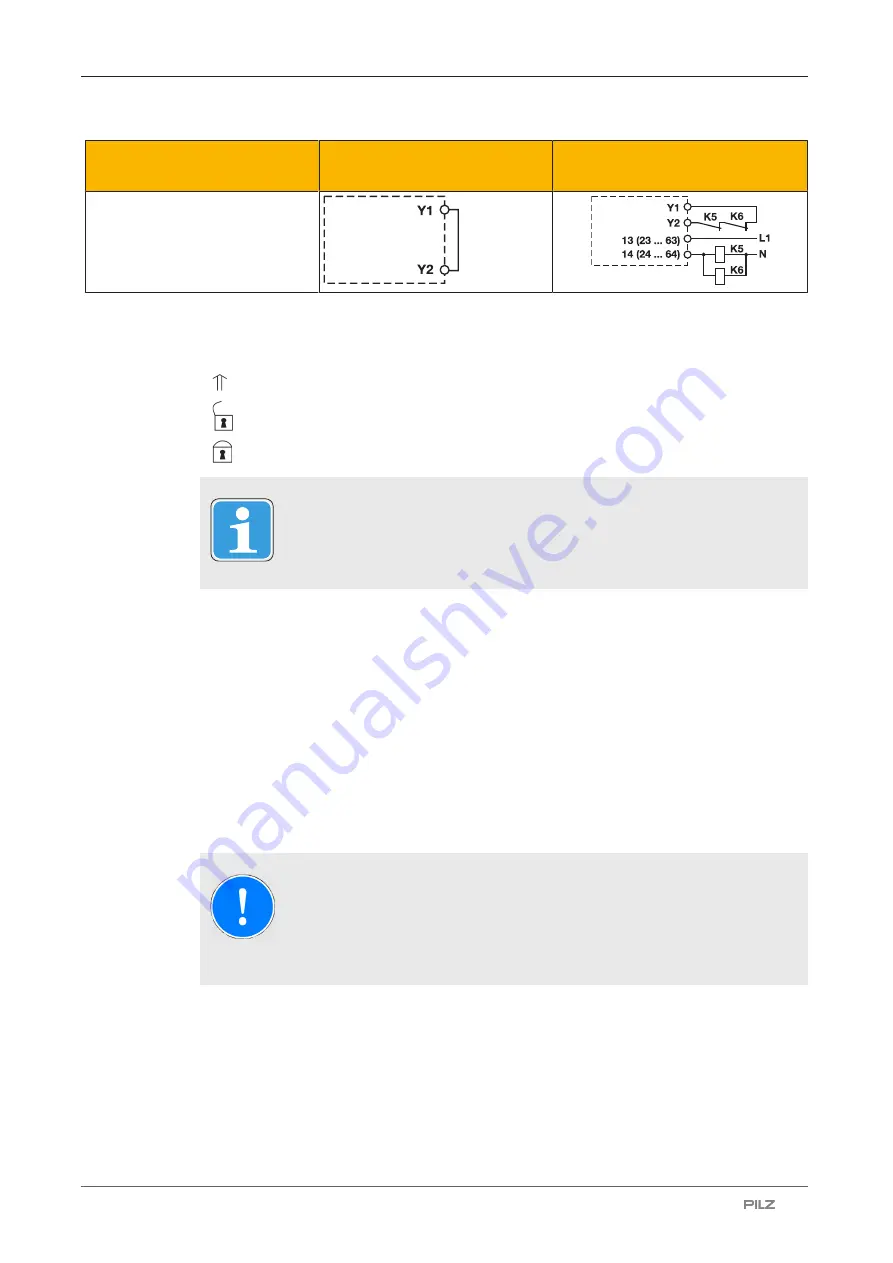
PNOZ X10.1
Operating Manual PNOZ X10.1
20005-EN-10
| 13
Feedback loop
Without feedback loop monit-
oring
With feedback loop monitoring
Link or contacts from external
contactors
Legend
}
S1/S2: E-STOP/safety gate switch
}
S3: Reset button
}
: Switch operated
}
: Gate open
}
: Gate closed
INFORMATION
With automatic start and manual start, Y1 and S37 must not be linked.
Operation
When the relay outputs are switched on, the mechanical contact on the relay cannot be
tested automatically. Depending on the operational environment, measures to detect the
non-opening of switching elements may be required under some circumstances.
When the product is used in accordance with the European Machinery Directive, a check
must be carried out to ensure that the safety contacts on the relay outputs open correctly.
Open the safety contacts (switch off output) and start the device again, so that the internal
diagnostics can check that the safety contacts open correctly
}
for SIL CL 3/PL e at least 1x per month
}
for SIL CL 2/PL d at least 1x per year
NOTICE
The safety function should be checked after initial commissioning and each
time the plant/machine is changed. The safety functions may only be
checked by qualified personnel.