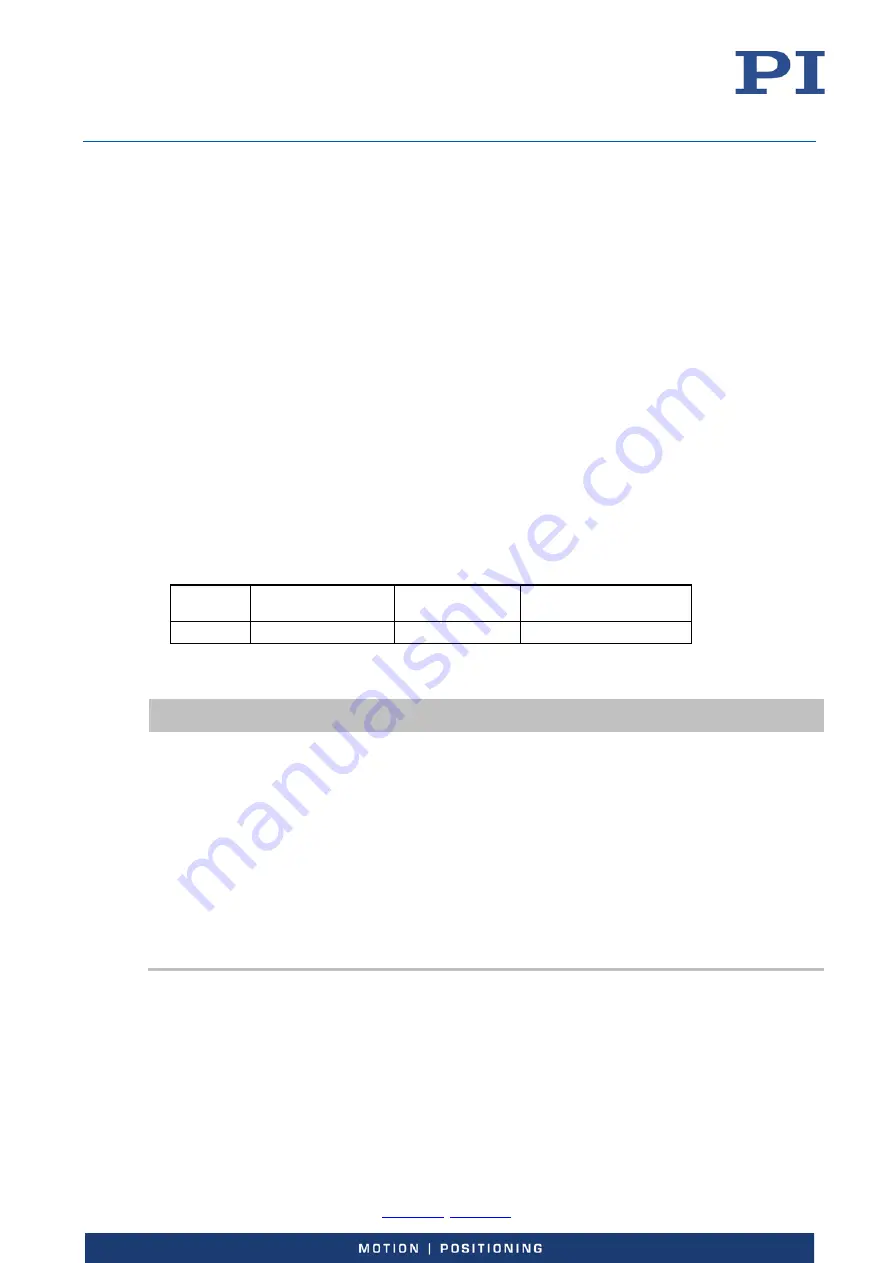
User Manual
E727T0005, valid for E-727
BRO, 2019-06-28
Physik Instrumente (PI) GmbH & Co. KG, Auf der Roemerstrasse 1, 76228 Karlsruhe, Germany
Page 71 / 240
Phone +49 721 4846-0, Fax +49 721 4846-1019, Email
Example—"Position Distance" Trigger Mode
The "Position Distance" trigger mode is designed for scanning applications. A trigger pulse is
written whenever the axis has covered the distance set with CTO (<TriggerStep>). The unit of
<TriggerStep> is the physical unit of the axes (query with the PUN? command).
In addition to the basic configuration, the “Position Distance” trigger mode provides several
options:
Definition of pulse length, p. 72: variable (depending on velocity) or constant
Definition of thresholds for trigger limitation to a certain position range and
direction of motion, p. 74
Filter definition for reduction of false triggers, p. 76
Basic trigger configuration
The following parameters must be set for the digital output line which is to be used for trigger
output (<TrigOutID>):
Axis (<CTOPam> = 2)
TriggerMode (<CTOPam> = 3)
TriggerStep (<CTOPam> = 1)
General notation of the CTO command for this mode (in fact, the command arguments can be
divided in three "portions", each starting with the <TrigOutID> declaration):
Command
mnemonic
Axis selection
Trigger mode
selection
Step size setting
CTO
<TrigOutID> 2
Axis
<TrigOutID> 3 0
<TrigOutID> 1
Stepsize
Instead of using the CTO command, you can also set the values of the corresponding parameters
with SPA or SEP, see “Configuring Trigger Output” (p. 69) for a parameter list.
INFORMATION
Possible values for TriggerStep depend on the axis velocity.
With high velocities, the minimum TriggerStep value is limited as follows:
TriggerStep > 4 * velocity * Servo Update Time
Servo Update Time is given in seconds by parameter 0x0E000200
Examples (the Servo Update Time of the E-727 is 50 µs):
o
With a velocity of 1000 µm/s, the minimum TriggerStep value is 200 nm.
o
With a TriggerStep value of 100 nm, the maximum velocity is 500 µm/s.
With very small velocities, the minimum TriggerStep value is limited by the noise of the
position sensor. For reliable triggering, the TriggerStep setting has to be at least 5 times larger
than the peak-to-peak level of the sensor noise. The sensor noise level can be reduced by
digital filtering of the signal (p. 27). To detect the noise, you can record, for example, the
position error of the axis using the data recorder.
Example: A pulse on the digital output line 1 is to be generated whenever axis 1 of the stage has
covered a distance of 0.1 µm. Send:
CTO 1 2 1 1 3 0 1 1 0.1