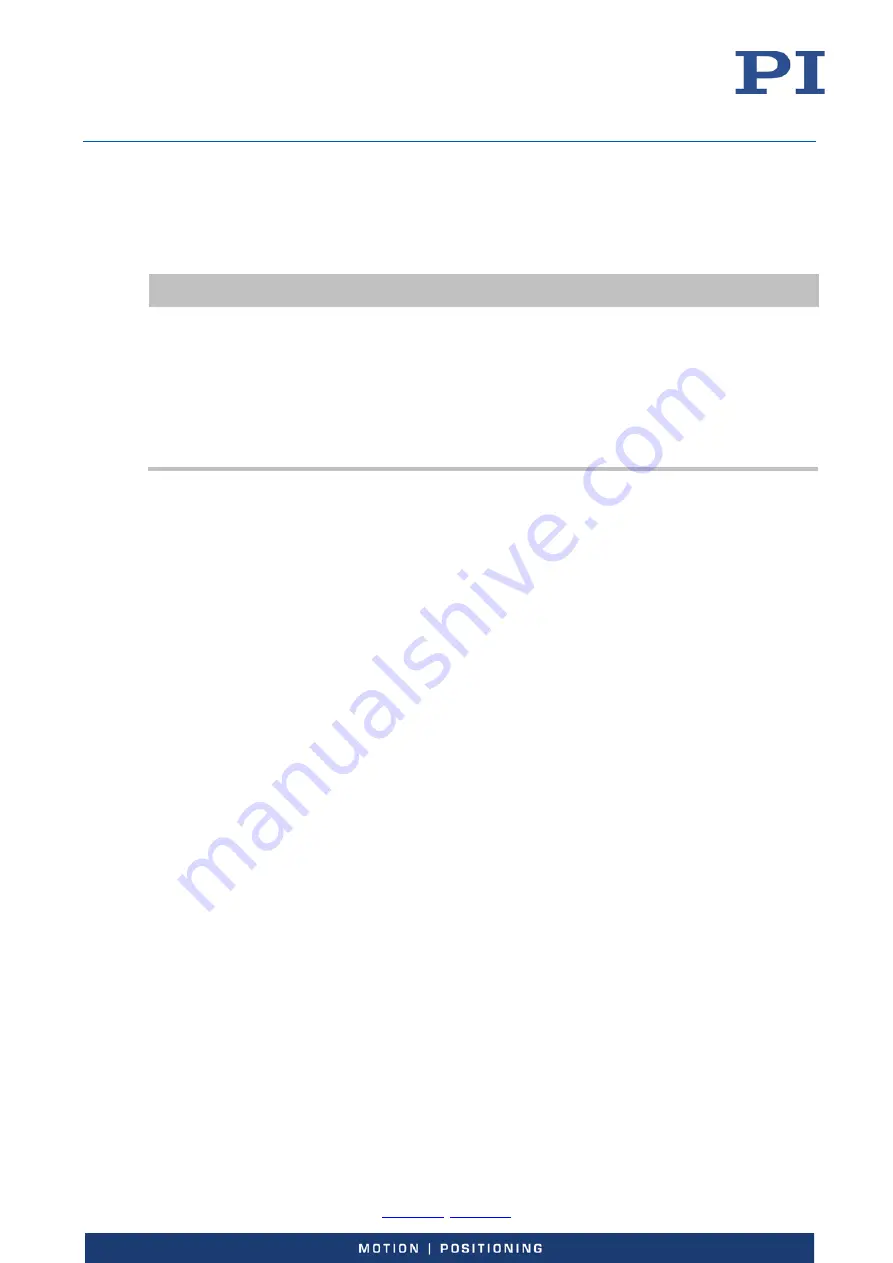
User Manual
E727T0005, valid for E-727
BRO, 2019-06-28
Physik Instrumente (PI) GmbH & Co. KG, Auf der Roemerstrasse 1, 76228 Karlsruhe, Germany
Page 30 / 240
Phone +49 721 4846-0, Fax +49 721 4846-1019, Email
In PIMikroMove, these parameters are available in the
Axis Definition
parameter groups in the
Device Parameter Configuration
window. In addition, you can check the matrix coefficients in the
Axis Matrices
window (open via
View -> Axis Matrices
menu item of the
Device Parameter
Configuration
window).
INFORMATION
The coefficients of the input matrix are determined during calibration at the factory. The preset
values of the coefficients for the internal sensors should not be changed.
If the connected mechanics has an ID-chip, the coefficients will be read in from the ID-chip (see
"ID-Chip Support / Stage Replacement" (p. 131) for more information).
E-727.xxxA and .xxxAx models only:
The coefficients for the analog input lines should be set to zero as long as no external sensors are
connected to the analog input lines or when the analog input is used for control value generation
(see "Using the Analog Input" (p. 85) for more information).
While TSP? reports the position values of the input signal channels, the POS? command reports the
axis positions calculated via the input matrix. Note that the physical units to be used for the axes
can be queried with the PUN? command.
Control Value Generation
The control value for the motion of an axis can result from multiple sources (see below).
Furthermore, the feedback from multiple sensors can be used to maintain the axis position,
depending on the current operating mode. The interpretation of the control values depends on the
settings of the output matrix (see "Output Generation" (p. 34) for more information). By default,
the output matrix is set up so that control values correspond numerically to axis position values.
The E-727 provides the following operating modes:
Open-loop control
(also referred to as "servo-off state" in this document): No
control algorithm is used, and the sensor feedback does not participate in the
control value generation.
Closed-loop control
(also referred to as "servo-on state" in this document): Sensor
feedback participates in the control value generation.
For each logical axis, a control algorithm is used to generate corrections to the
control value (default: PID algorithm). In addition, two notch filters are used for each
axis (default: only active in closed-loop operation). The settings for control algorithm
and notch filters are accessible as parameters. See "Control Details" (p. 35), "Servo
Controller Dynamic Tuning" (p. 134) and " Parameters" (p. 185) for more
information.
The operating mode can be selected with the SVO command for each axis. By default, open-loop
control is active after power-on. Using the
Power Up Servo On Enable
parameter (ID 0x07000800),
you can set up the individual axes to start with closed-loop control. When switching from open-
loop to closed-loop control, the behaviour depends on the setting made with parameter