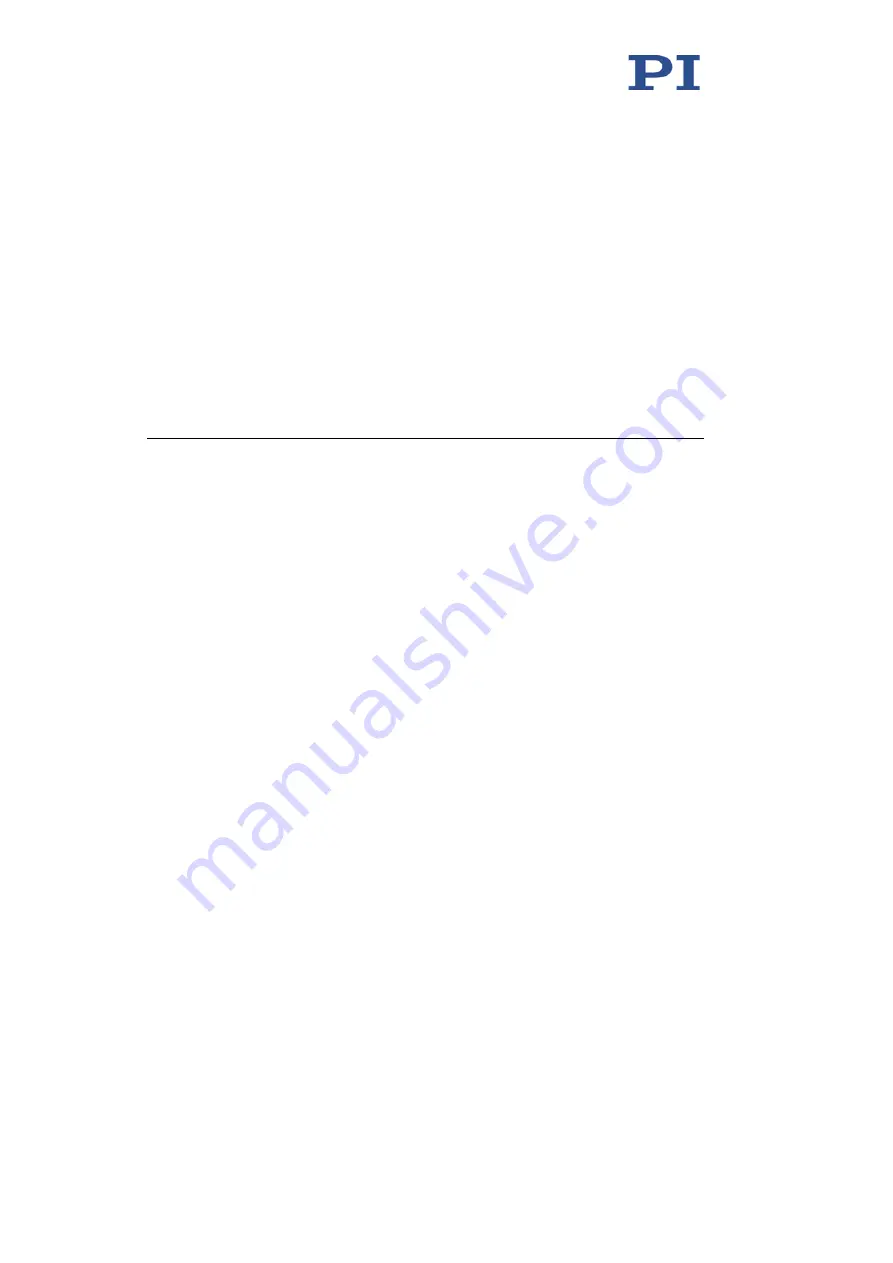
Operation
www.pi.ws
E-651 / E-614 Controller / Amplifier PZ129E Release 6.1.0 Page 13
4.2.2
Open-Loop Operation
In open-loop mode the variable output voltage for the actuator
is controlled by the control input signal (this output voltage for
the actuator is in direct linear relation to the control input
voltage).
A channel of an E-651 benchtop device is in open-loop mode if
the corresponding SERVO switch on the front panel is set to
OFF.
For information on E-614 OEM modules, see the E614T0003
technical note.
4.3
On-Board Submodules
Each E-651 / E-614 channel is equipped with submodules for
sensor processing (E-801) and servo-control (E-802).
4.3.1
E-801 Submodule for Strain Gauge Sensor Processing
This submodule is used for excitation and evaluation of one
strain gauge sensor (SGS). It is designed as a plug-in
submodule to be used on different PCBs.
The submodule supplies the strain gauge with a DC voltage
and generates a signal proportional to the expansion changes
of the strain gauge. Located on the submodule is a sensor gain
adjustment and settings for a low-pass filter.
See the SGS portions of the E-801 User Manual (PZ117E) for
details.
4.3.2
E-802 Position Servo-Control Submodule
The E-802 submodule produces an analog control signal for the
power amplifier driving the actuator. Slew rate limitation, notch
filter and servo-control loop are all implemented on the E-802.
The servo-loop logic compares the control voltage input (target)
and the sensor signal (current position) to generate the
amplifier control signal using an analog proportional-integral
(P-I) algorithm.
For calibration procedures, see “Calibration” and the E-802
Servo-Control Submodule User Manual (PZ150E).