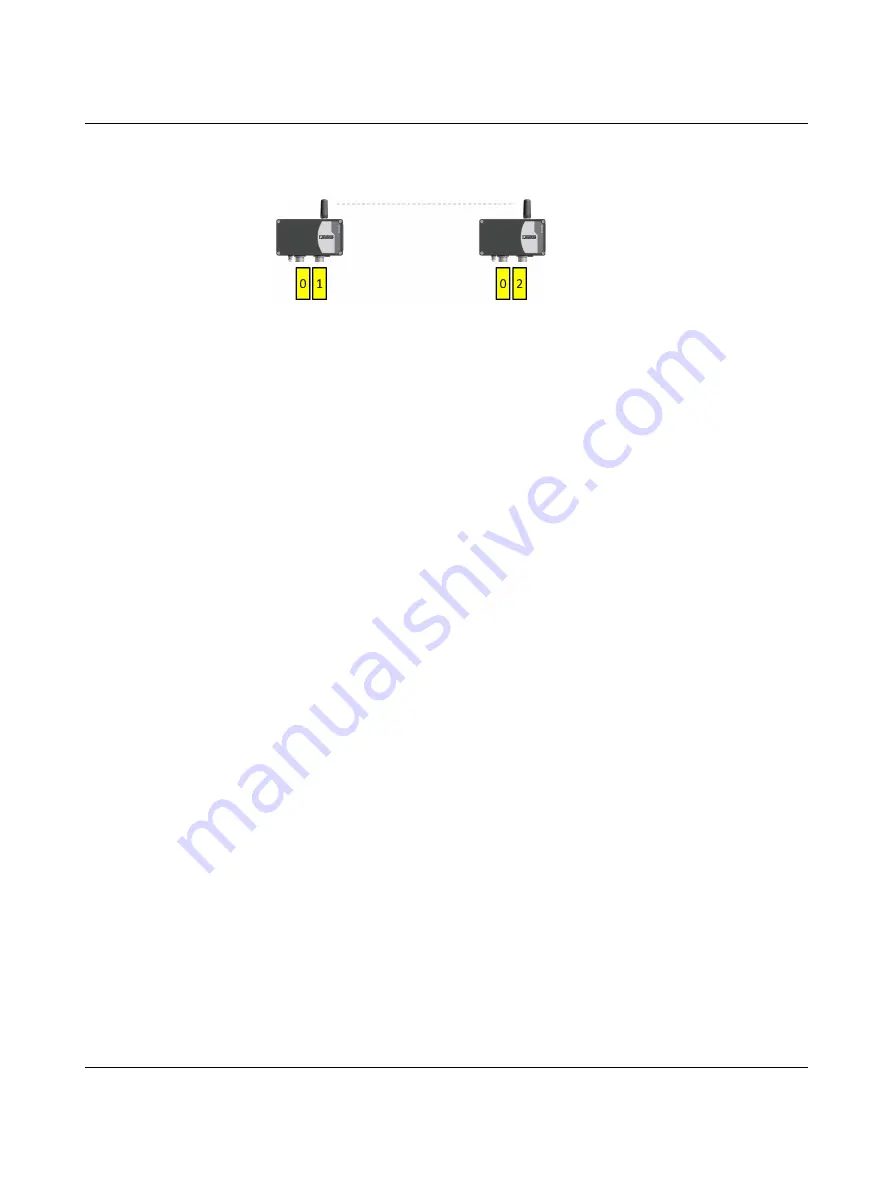
Configuration and startup
3827_en_B
PHOENIX CONTACT
–
The RAD-900-DAIO6 may be used to create a point-to-point connection with another
RAD-900-DAIO6. In this case, one RAD-900-DAIO6 must have its address set to
01
and the other must be set to
02
.
Figure 5-15
Thumbwheel addressing of the RAD-900-DAIO6 in point-to-point mode
Wireless module in PLC/Modbus RTU mode
–
Multiple RAD-900-DAIO6 devices may not use the same thumbwheel address in a
single network.
–
The input and output data is saved in a Modbus memory map in the master wireless
module. You can read or write the process data via the serial interface of the master
wireless module (RAD ID = 01) using the Modbus RTU command. The process data
tables can be found starting at “Modbus memory map” on page 100.
5.8.2
RAD-900-DAIO6 in PLC/Modbus RTU dual mode
–
Each wireless module is assigned a Modbus address. The Modbus address of each
module is that of the RAD-ID (yellow thumbwheel) set on the module. The master
wireless module Modbus address may be changed from
01
, if an existing Modbus
device is already assigned this address. A Modbus address may only appear once in
the network.
–
Each RAD-900-DAIO6 device must use a unique thumbwheel address within a single
network.
–
The input and output data is saved in a Modbus memory map in the wireless module.
You can read or write the process data via the serial interface of the master wireless
module (RAD ID = 01) using the Modbus RTU command. The process data tables can