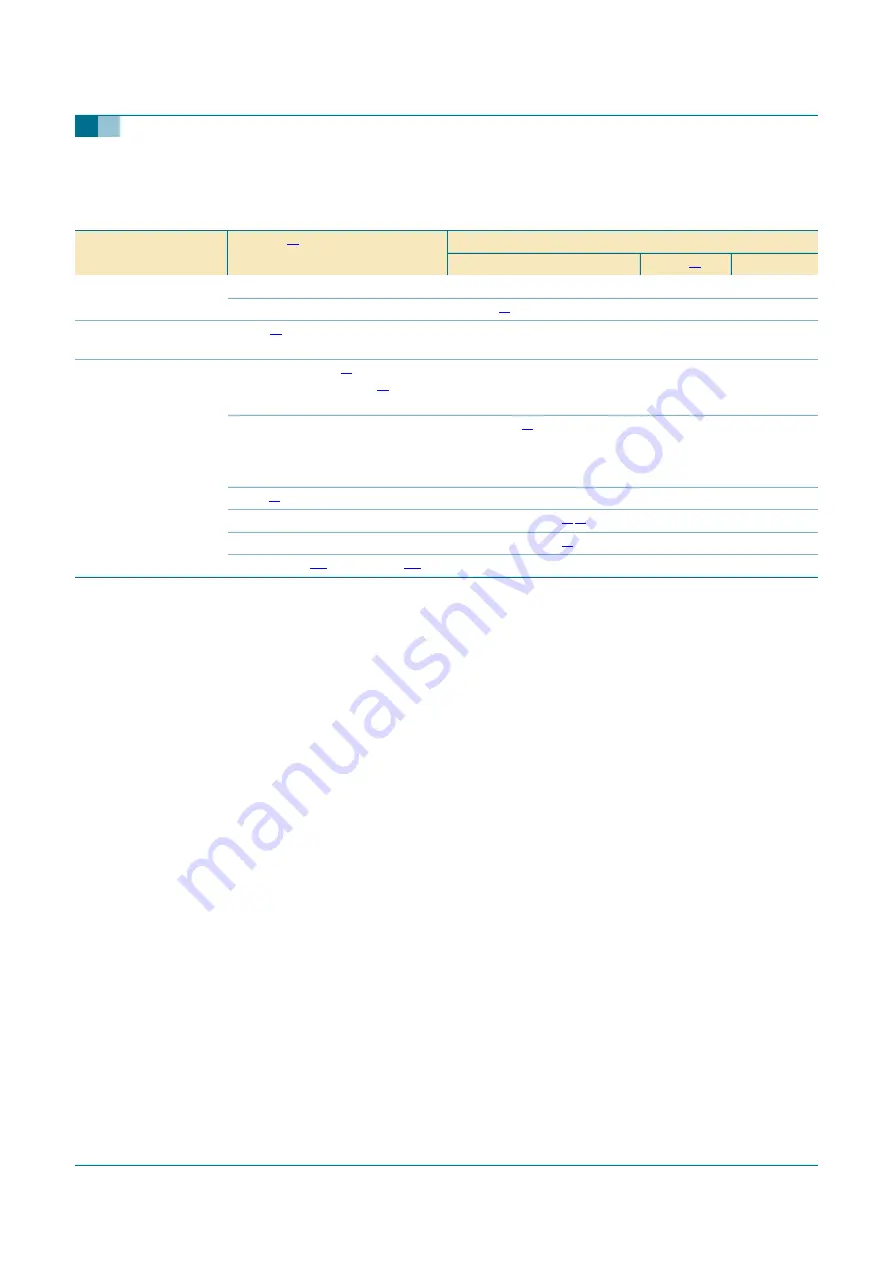
TDA8920B_2
© Koninklijke Philips Electronics N.V. 2005. All rights reserved.
Product data sheet
Rev. 02 — 07 November 2005
31 of 34
Philips Semiconductors
TDA8920B
2
×
100 W class-D power amplifier
16.4 Package related soldering information
[1]
For more detailed information on the BGA packages refer to the
(LF)BGA Application Note (AN01026); order a copy from your Philips
Semiconductors sales office.
[2]
All surface mount (SMD) packages are moisture sensitive. Depending upon the moisture content, the maximum temperature (with
respect to time) and body size of the package, there is a risk that internal or external package cracks may occur due to vaporization of
the moisture in them (the so called popcorn effect). For details, refer to the Drypack information in the
Data Handbook IC26; Integrated
Circuit Packages; Section: Packing Methods.
[3]
For SDIP packages, the longitudinal axis must be parallel to the transport direction of the printed-circuit board.
[4]
Hot bar soldering or manual soldering is suitable for PMFP packages.
[5]
These transparent plastic packages are extremely sensitive to reflow soldering conditions and must on no account be processed
through more than one soldering cycle or subjected to infrared reflow soldering with peak temperature exceeding 217
°
C
±
10
°
C
measured in the atmosphere of the reflow oven. The package body peak temperature must be kept as low as possible.
[6]
These packages are not suitable for wave soldering. On versions with the heatsink on the bottom side, the solder cannot penetrate
between the printed-circuit board and the heatsink. On versions with the heatsink on the top side, the solder might be deposited on the
heatsink surface.
[7]
If wave soldering is considered, then the package must be placed at a 45
°
angle to the solder wave direction. The package footprint
must incorporate solder thieves downstream and at the side corners.
[8]
Wave soldering is suitable for LQFP, QFP and TQFP packages with a pitch (e) larger than 0.8 mm; it is definitely not suitable for
packages with a pitch (e) equal to or smaller than 0.65 mm.
[9]
Wave soldering is suitable for SSOP, TSSOP, VSO and VSSOP packages with a pitch (e) equal to or larger than 0.65 mm; it is definitely
not suitable for packages with a pitch (e) equal to or smaller than 0.5 mm.
[10] Image sensor packages in principle should not be soldered. They are mounted in sockets or delivered pre-mounted on flex foil.
However, the image sensor package can be mounted by the client on a flex foil by using a hot bar soldering process. The appropriate
soldering profile can be provided on request.
Table 11:
Suitability of IC packages for wave, reflow and dipping soldering methods
Mounting
Package
[1]
Soldering method
Wave
Reflow
[2]
Dipping
Through-hole mount
CPGA, HCPGA
suitable
−
−
DBS, DIP, HDIP, RDBS, SDIP, SIL
suitable
[3]
−
suitable
Through-hole-surface
mount
PMFP
[4]
not suitable
not suitable
−
Surface mount
BGA, HTSSON..T
[5]
, LBGA,
LFBGA, SQFP, SSOP..T
[5]
,
TFBGA, VFBGA, XSON
not suitable
suitable
−
DHVQFN, HBCC, HBGA, HLQFP,
HSO, HSOP, HSQFP, HSSON,
HTQFP, HTSSOP, HVQFN,
HVSON, SMS
not suitable
[6]
suitable
−
PLCC
[7]
, SO, SOJ
suitable
suitable
−
LQFP, QFP, TQFP
not recommended
[7] [8]
suitable
−
SSOP, TSSOP, VSO, VSSOP
not recommended
[9]
suitable
−
CWQCCN..L
[10]
, WQCCN..L
[10]
not suitable
not suitable
−