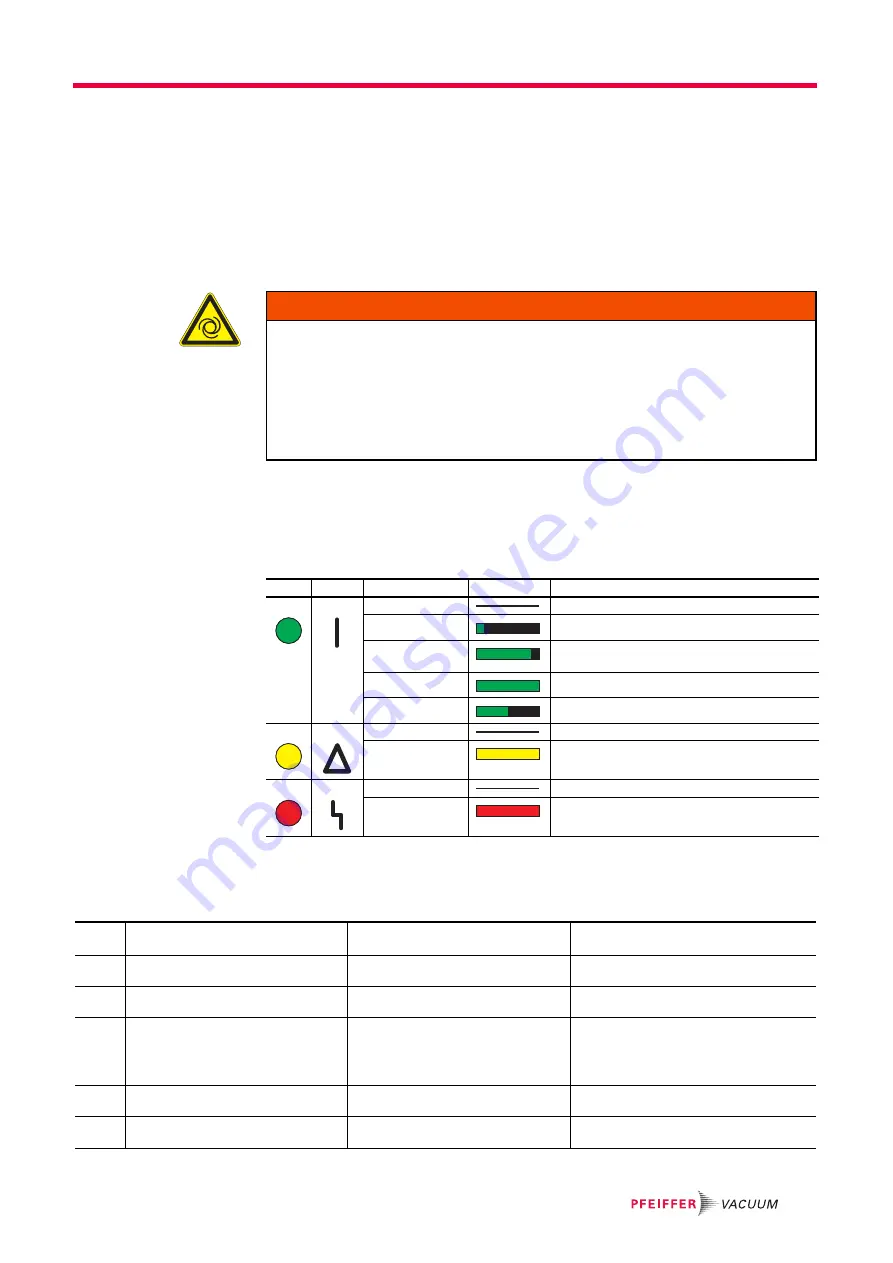
Malfunctions
33
9
Malfunctions
9.1
General
Turbopump and electronic drive unit malfunctions always result in a warning or error
message. In both cases, the electronic drive unit outputs an error code. Operating mes-
sages are generally displayed via the LEDs on the electronic drive unit. If an error occurs,
the turbopump and connected devices will be switched off. The selected venting mode
will be triggered after the preset delay.
9.2
Operation display via LED
LEDs in the front panel of the electronic drive unit show basic operating conditions of the
turbopump. A differentiated malfunction and warning display is possible only for opera-
tion with DCU or HPU.
Fig. 8:
Behaviour and meaning of LEDs on the electronic drive unit
9.3
Error codes
WARNING
Automatic start-up after power failure or malfunction acknowledgement
The function "pumping station" of the electronic drive unit remains active after power
failure or errors that lead to shut down the pump or the system. The turbopump runs up
automatically after power ist restored or malfunction acknowledgement.
Switch off the function "pumping station" if necessary.
Provide safety measures against interference in the high vacuum flange while the tur-
bopump is running.
LED
Symbol LED status
Display
Meaning
Green
Off
currentless
On, flashing
"Pumping Station OFF", rotation speed
≤
60 min
-1
On, invers flashing
"Pumping Station ON", set rotation speed not at-
tained
On, constantly
"Pumping Station ON", set rotation speed attained
On, blinking
"Pumping Station OFF", rotation speed > 60 min
-1
Yellow
Off
no warning
On, constantly
Warning
Red
Off
no malfunction
On, constantly
Malfunction
Error
code
Problem
Possible causes
Remedy
Err001
Overspeed
Call Pfeiffer Vacuum Service
Only acknowledge for rotational speed f = 0
Err002
Overvoltage
– Incorrect power pack used
Check power pack type
Check partial mains voltage
Err006
Run-up fault
– Run-up time threshold set too low
– Gas flow in recipient through leaks or
open valves
– Speed-control switching point not
reached upon expiration of run-up time
Adjust run-up time to process conditions
Check recipient for leakage and closed
valves
Adjust speed-control switching point
Err007
Insufficient operating materials
– Insufficient operating materials
Check operating materials
Only acknowledge for rotational speed f = 0
Err008
Connection from electronic drive unit to
pump faulty
– Connection to pump faulty
Check connections
Only acknowledge for rotational speed f = 0