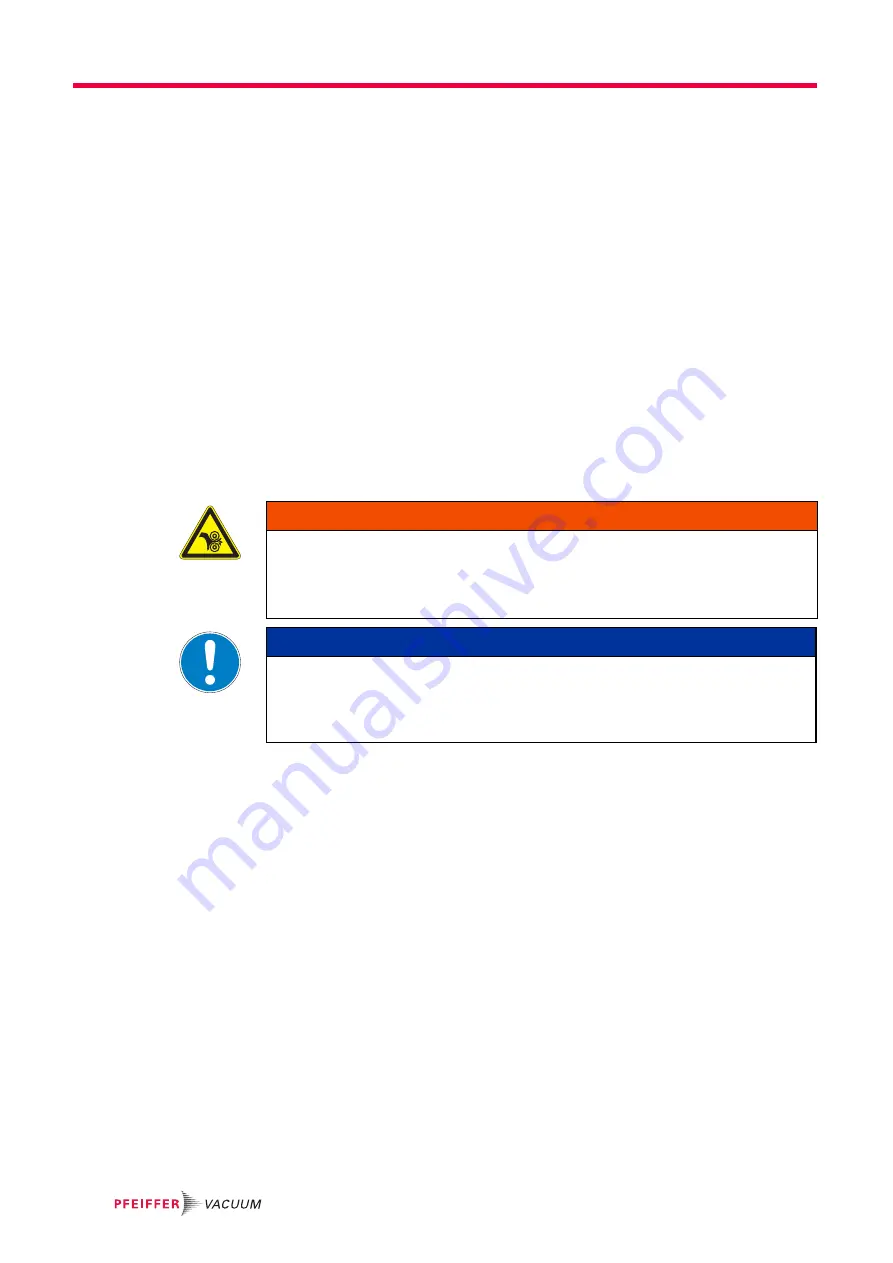
26
Maintenance
Change sealing oil
(only for version with
RSSR)
It is recommended that the sealing oil should be changed on an annual basis.
Unscrew lubricant drain screw 16.1 at the sealing oil chamber; check the O-ring.
Allow the lubricant to drain off.
Screw in lubricant drain screw 16.1 with O-ring.
Fill oiler 18 to halfway with new lubricant (sealing oil).
Falling oil level in the oiler and an oil leak below the lamp indicates a defective
external
radial shaft seal ring. In this case, the pump can continue to operate for a certain time
provided the oil loss from the oiler is equalised.
Conversely, an increasing oil level without visible loss below the pump indicates a worn
internal
radial shaft seal ring. All three sealing rings should be replaced immediately as
it will cause the oil in the bearing chamber to rise above the permitted level.
Changing the sealant
of the mechanical
seal
Maintenance work on the mechanical seal and the sealant reservoir should be per-
formed in accordance with the maintenance instructions supplied by the manufactur-
er; the intervals for changing the sealant may vary from application to application.
Use the sealant in accordance with the manufacturer's instructions.
7.3
Cleaning the suction chamber
Disconnect the drive motor from the mains and secure it so that it cannot be switched
on.
Dismantle the vacuum line and the fore-vacuum line of the pump.
Dismantle the overflow valve
.
Clean the suction chamber and overflow channel using suitable brushes and cleaning
agents.
After cleaning, remove remaining fluids using absorbent materials and dry the working
chamber.
Reassemble the overflow valve and pipework after cleaning.
Remove the means by which the motor was secured against being switched on.
The lubricant should also be replaced
after every suction cham-
ber cleaning.
WARNING
Exposed, rotating rolling pistons!
Fingers and hands can become crushed when the intake flange is open.
Keep all body parts out of operating range of the rolling pistons.
Use a wooden handle to rotate the rolling pistons during cleaning.
NOTICE
Risk of damage to the pump!
During the flushing and cleaning procedure the flushing liquid and the process medium
can pass over into the bearings and oil chambers and can stick there.
To protect the bearings during cleaning, sealing gas must always be used.