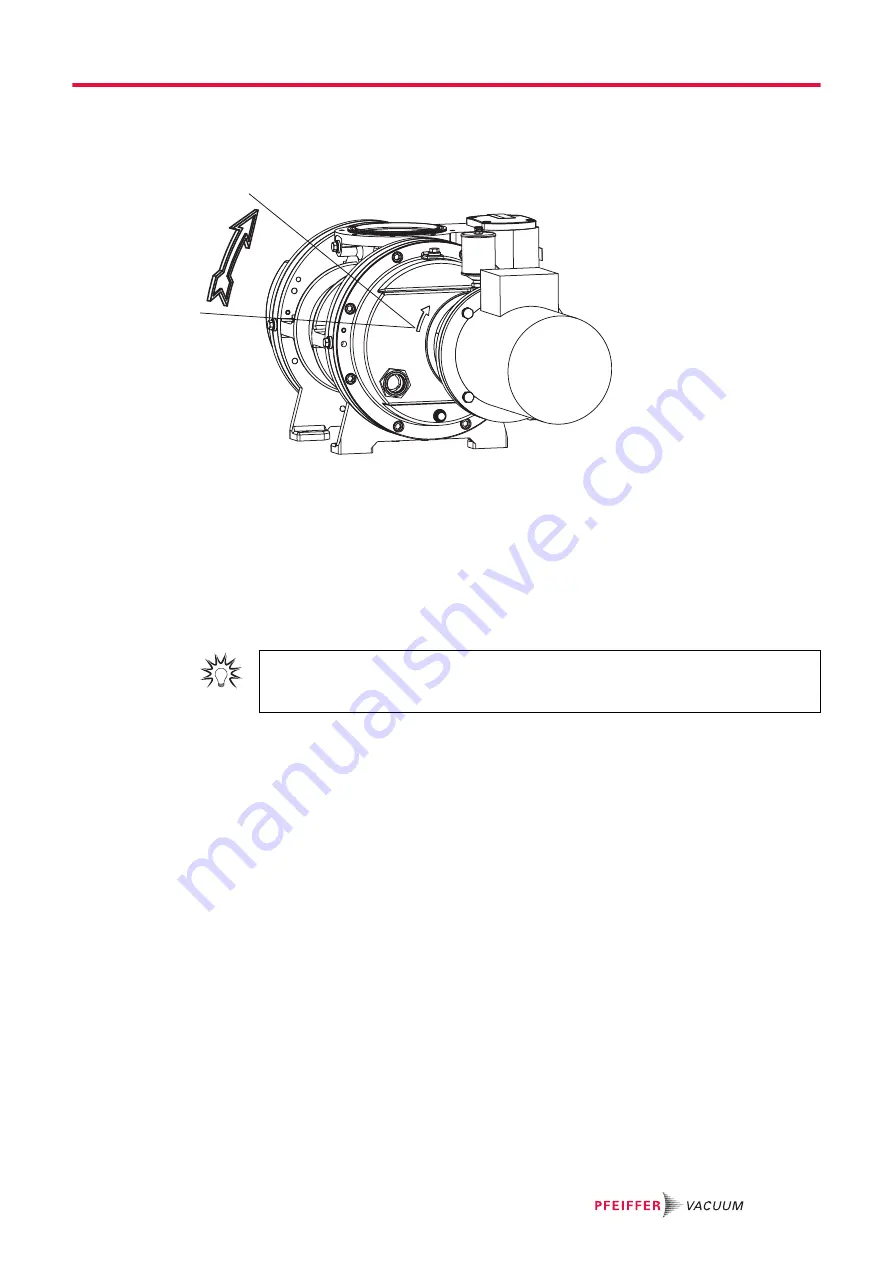
The ends of the 3 phases are connected in the star point. The terminal voltage is √3 times the phase
voltage, the mains current is equal to the phase current. The star circuit is marked with the Y symbol.
5.6.2 Checking the direction of rotation
Fig. 8:
Check of direction of rotation
Procedure
When switching on for the first time, check the roots pump direction of rotation.
1. Switch the vacuum pump on briefly (2 to 3 seconds)
– The motor and coupling must rotate clockwise (see directional arrow on housing cover).
2. If the direction of rotation is incorrect, exchange the 2 phases on the connection cable.
5.6.3 Connecting the PTC thermistor tripping unit
Tripping units store the shut-down
Pfeiffer Vacuum recommends connecting motors with PTC in the stator winding to a PTC
resistor tripping device for protection against overload.
Installation
25/52