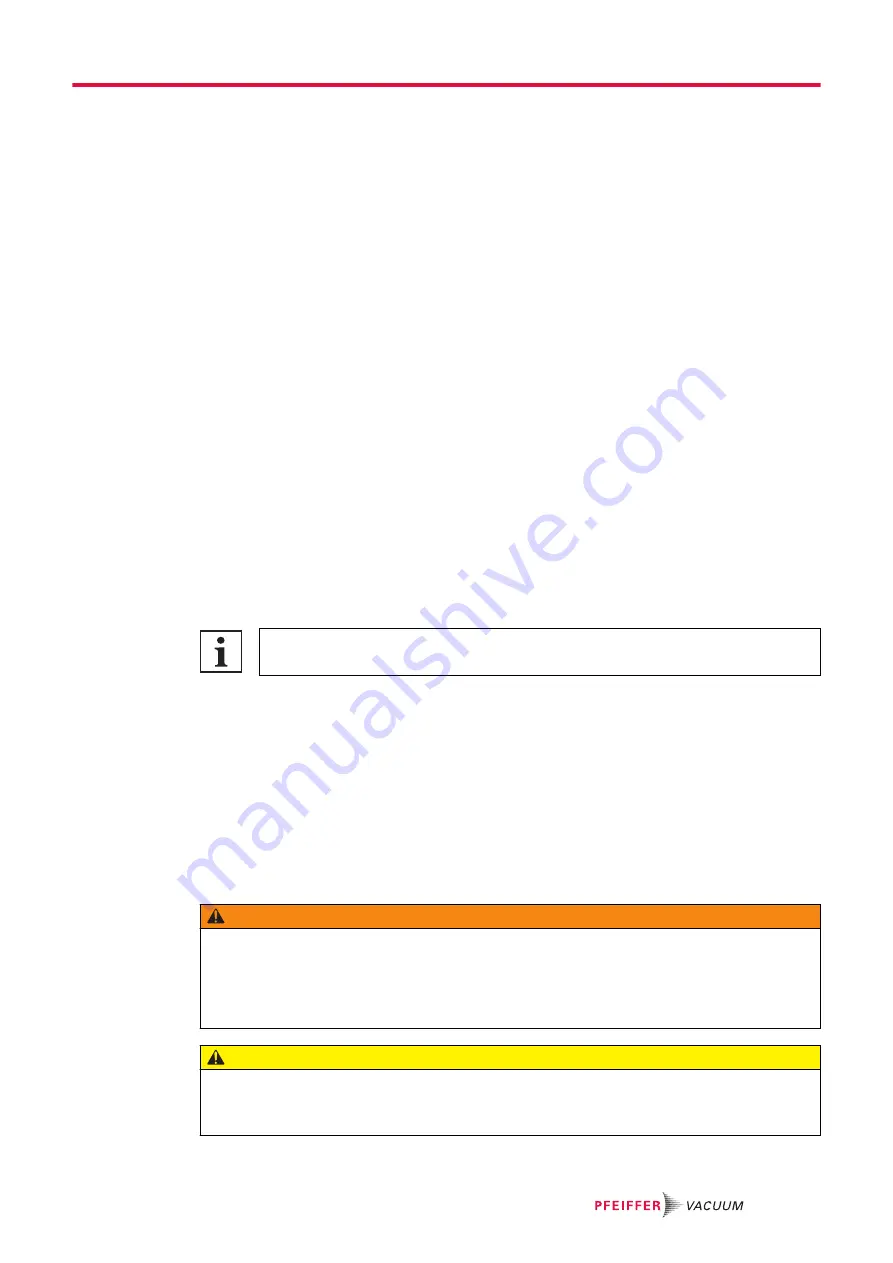
6.3 Adjusting rotation speed
When operating the vacuum pump, there are 3 different control options, each of which can lead to a
smooth circular runout of the vacuum pump at motor rotation speed > 400 rpm. The motor rotation
speed of the vacuum pump increases linearly in each case up to max. rotation speed.
The higher the motor rotation speed, the higher the pumping speed. The lower the rotation speed, the
longer the service life of the diaphragms and valves. In the low rotation speed range between approx.
600 and 1000 rpm, the diaphragm pump achieves the best final vacuum.
Prerequisites
● Trimmer turned to left stop
● Control cable connected on terminal block ST1B (except with setting via trimmer)
Setting the rotation speed externally through the PWM signal
► For a user-specific rotation speed, specify the control cable to apply an electrically isolated PWM
signal to terminal block ST1B.
– 5 V – 24 V (mandatory), boundary frequency: > 100 Hz, < 1.5 kHz
Setting the rotation speed externally through analog voltage
► Specify an analog voltage in the range of 0.8 V to 10 V.
Setting the rotation speed via the trimmer
► Rotate the trimmer clockwise to increase the motor rotation speed.
► Rotate the trimmer anti-clockwise to reduce the motor rotation speed.
6.4 Operating the diaphragm pump in interval operation
The interval operation increases the service life of the diaphragm pump with low gas throughputs of
< 0.18 hPa l/s. The turbopump electronic drive unit switches the diaphragm pump on and off depending
on the rated input of the turbopump. The rated input of the turbopump depends on the fore-vacuum
pressure and gas throughput.
It is not possible to control the rotation speed
Rotation speed control is not possible in this operating mode.
Procedure
1. Apply a galvanically isolated PWM signal to the control signal input.
– 0 V = pump "off”, 24 V = pump “on” (max. rotation speed)
2. For low gas throughput, reduce the relative duty cycle to about 1 to 60% by comparing the rated
input with an upper and lower threshold value.
3. From approx. 0.018 hPa l/s, make sure that the buffer volume in the fore-vacuum line is 0.5 liters
in order to avoid switching on too frequently.
6.5 Pumping condensable vapors
Vapors or moisture from pumped media impair the throughput after condensation in the vacuum pump.
WARNING
Risk of explosion from reactive, explosive or other hazardous gas / air mixtures.
Uncontrolled inlet of gas at the flushing gas nozzle leads to sparks generated mechanically following
diaphragm rupture, hot surfaces or to explosive gas / air mixtures in the vacuum system caused by
static electricity.
► If necessary, use inert gas for supplying the flushing gas in order to avoid a potential ignition.
CAUTION
Risk of poisoning due to toxic process gases escaping
For intake pressures > 500 hPa, process gas may escape from the flushing gas nozzle.
► If necessary, use an extraction line.
Operation
23/42