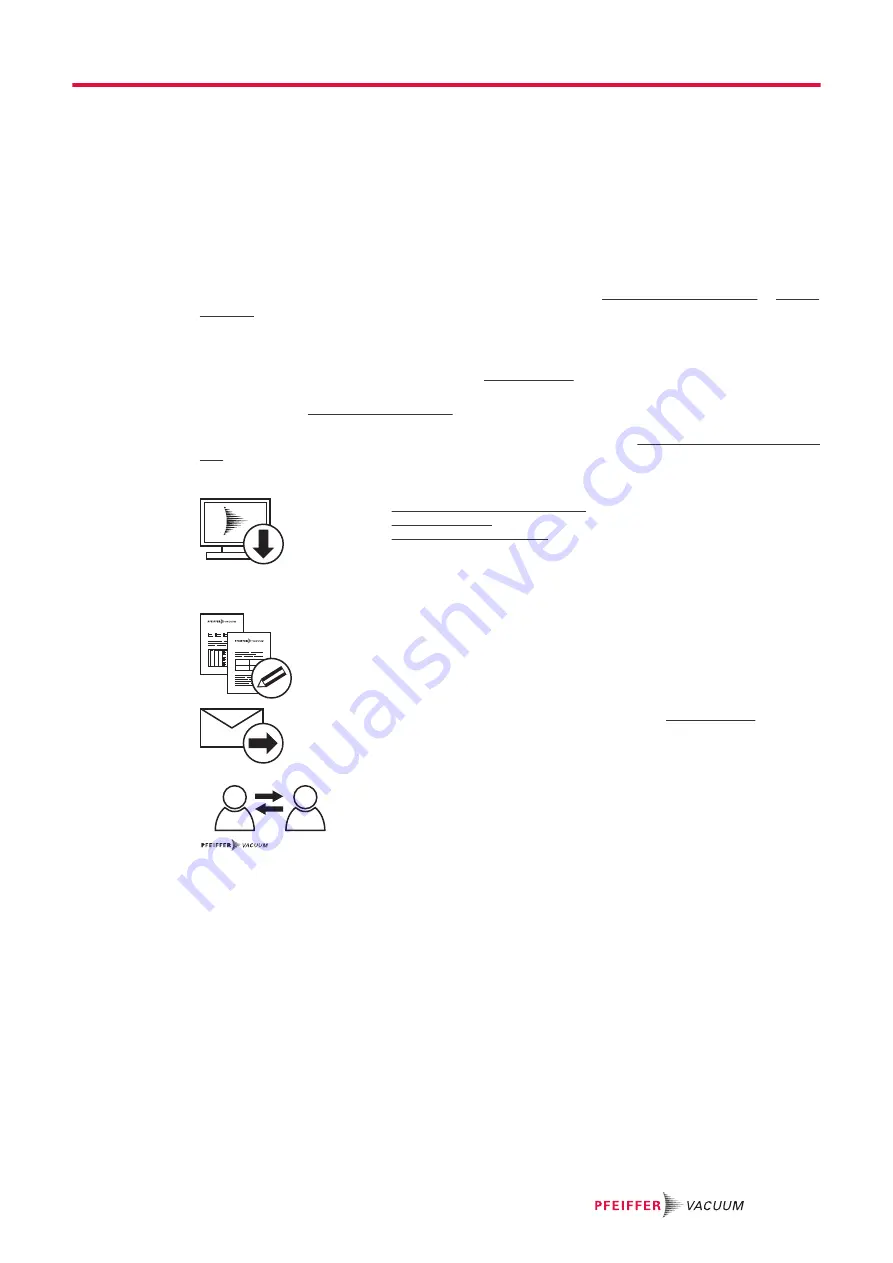
11 Service solutions by Pfeiffer Vacuum
We offer first-class service
High vacuum component service life, in combination with low downtime, are clear expectations that you
place on us. We meet your needs with efficient products and outstanding service.
We are always focused on perfecting our core competence – servicing of vacuum components. Once
you have purchased a product from Pfeiffer Vacuum, our service is far from over. This is often exactly
where service begins. Obviously, in proven Pfeiffer Vacuum quality.
Our professional sales and service employees are available to provide you with reliable assistance,
worldwide. Pfeiffer Vacuum offers an entire range of services, from
Make use of Pfeiffer Vacuum service
Whether preventive, on-site service carried out by our field service, fast replacement with mint condition
replacement products, or repair carried out in a
near you – you have various options for
maintaining your equipment availability. You can find more detailed information and addresses on our
homepage, in the
You can obtain advice on the optimal solution for you, from your
.
For fast and smooth service process handling, we recommend the following:
1. Download the up-to-date form templates.
─
Explanations of service requests
─
─
a) Remove and store all accessories (all external parts, such as valves, pro-
tective screens, etc.).
b) If necessary, drain operating fluid/lubricant.
c) If necessary, drain coolant.
ANFORDERUNG SERVICE
ERKLÄRUNG KONTAMINIERUNG
2. Complete the service request and contamination declaration.
3. Send the forms by email, fax, or post to your local
.
4. You will receive an acknowledgment from Pfeiffer Vacuum.
Submission of contaminated products
No microbiological, explosive, or radiologically contaminated products will be accepted. Where products
are contaminated, or the contamination declaration is missing, Pfeiffer Vacuum will contact you before
starting service work. Depending on the product and degree of pollution,
additional decontamination
costs
may be incurred.
Service solutions by Pfeiffer Vacuum
47/58