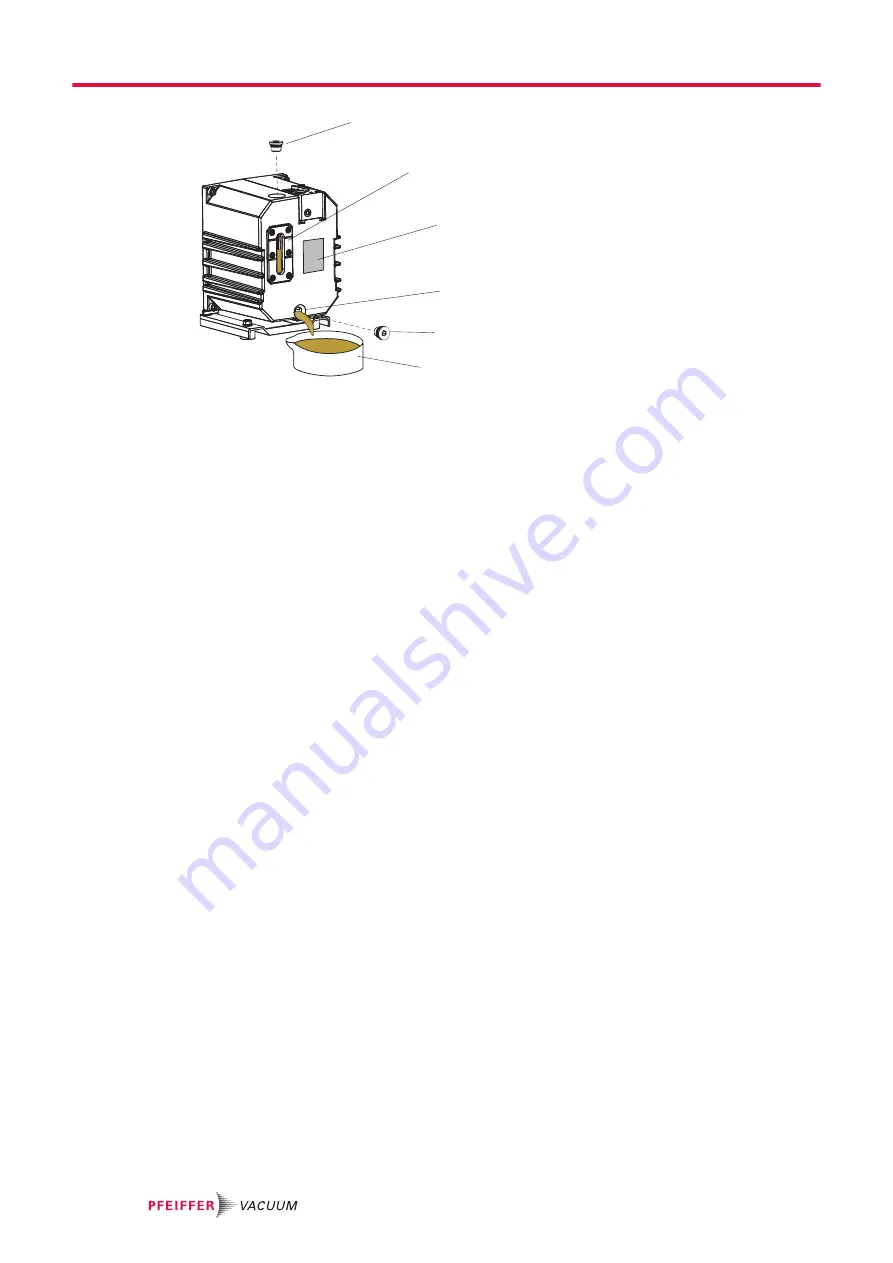
1
2
3
5
4
6
Fig. 16:
Draining the operating fluid
1 Filler screw with o-ring
4
Drain hole
2 Sight glass
5
Drain screw with o-ring
3 Rating plate
6
Collection receptacle
Consumable
● Operating fluid
Required tools
● Allen key,
WAF 6
● Allen key,
WAF 8
● Calibrated torque wrench (tightening factor ≤ 2.5)
Required aids
● Collection receptacle (> 1.5 l)
Prerequisites
● Vacuum pump switched off
● Vacuum pump is vented to atmospheric pressure on the suction side
● Vacuum pump cooled down and touchable, operating fluid still warm
Draining the operating fluid
1. Unscrew the filler screw.
– Be careful with o-ring.
2. Place a collection receptacle below the drain hole.
3. Unscrew the drain screw.
– Be careful with o-ring.
4. Allow operating fluid to drain into collection receptacle.
Agitate remaining operating fluid
1. Screw in the filler screw.
2. Screw in the drain screw.
3. Switch on the vacuum pump with the vacuum flange open for a maximum of 5 seconds.
Drain remaining operating fluid
1. Unscrew the drain screw.
2. Gently tilt the vacuum pump.
3. Drain remaining operating fluid.
4. Screw in the drain screw.
5. Dispose of old operating fluid according to applicable regulations.
Fill fresh operating fluid
1. Screw the drain screw in up to the stop.
– Be careful with the O-ring.
– Tightening torque:
3.0 Nm
2. Fill new operating fluid.
Maintenance
38/60