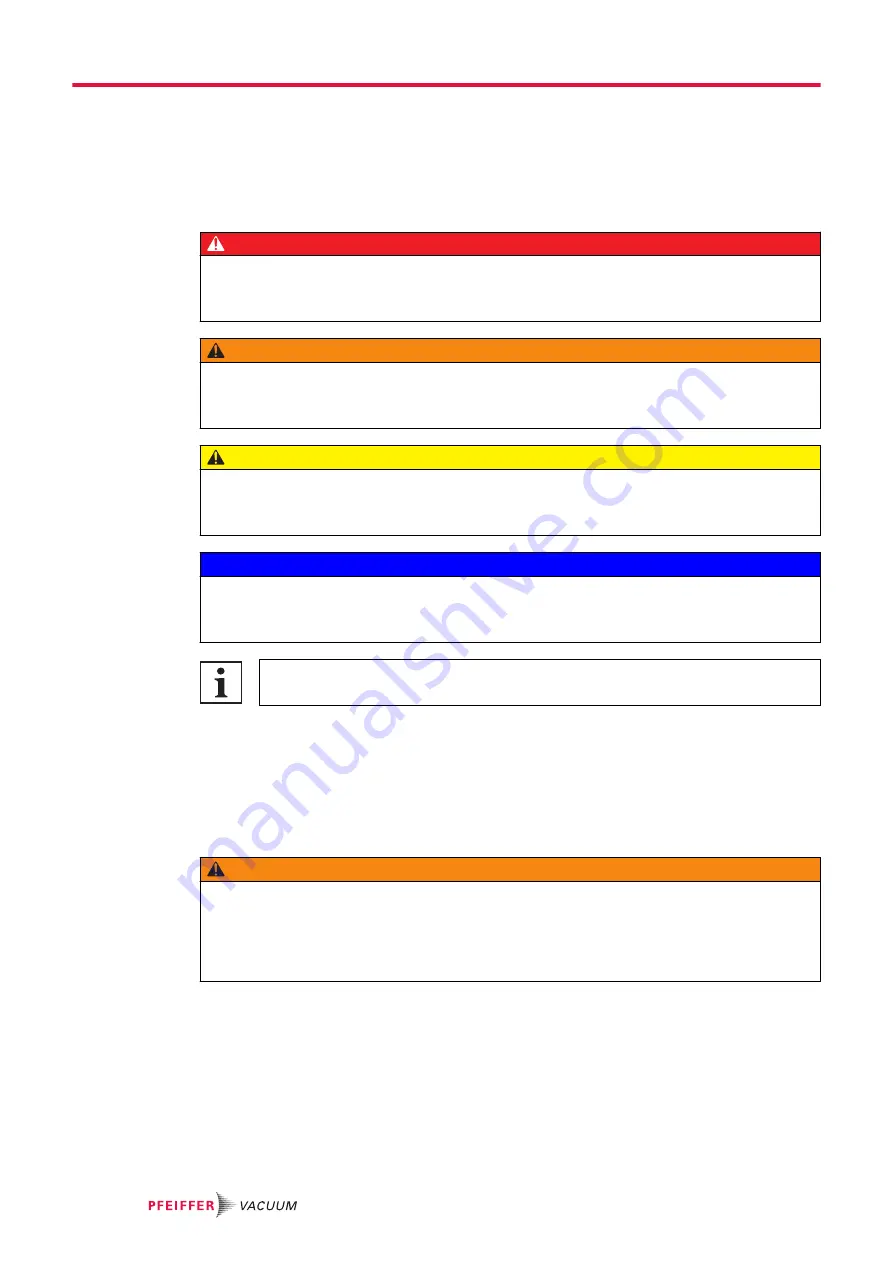
2 Safety
2.1 General safety instructions
This document includes the following 4 risk levels and 1 information level.
DANGER
Imminent danger
Indicates a hazardous situation which, if not avoided, will result in death or serious injury.
► Instructions on avoiding the hazardous situation
WARNING
Possibly imminent danger
Indicates a hazardous situation which, if not avoided, could result in death or serious injury.
► Instructions on avoiding the hazardous situation
CAUTION
Possibly imminent danger
Indicates a hazardous situation which, if not avoided, could result in minor or moderate injury.
► Instructions on avoiding the hazardous situation
NOTICE
Danger of property damage
Notice is used to address practices not related to physical injury.
► Instructions on avoiding property damage
Notes, tips or examples indicate important information on the product or on this document.
2.2 Safety instructions
All safety instructions in this document are based on the results of the risk assessment carried out in
accordance with Machinery Directive 2006/42/EC Annex I and EN ISO 12100 Section 5. Where applica-
ble, all life cycle phases of the product were taken into account.
Risks during transportation
WARNING
Danger of serious injury due to falling objects
Due to falling objects there is a risk of injuries to limbs through to broken bones.
► Take particular care and pay special attention when transporting products manually.
► Do not stack the products.
► Wear protective equipment, e.g. safety shoes.
Safety
10/60