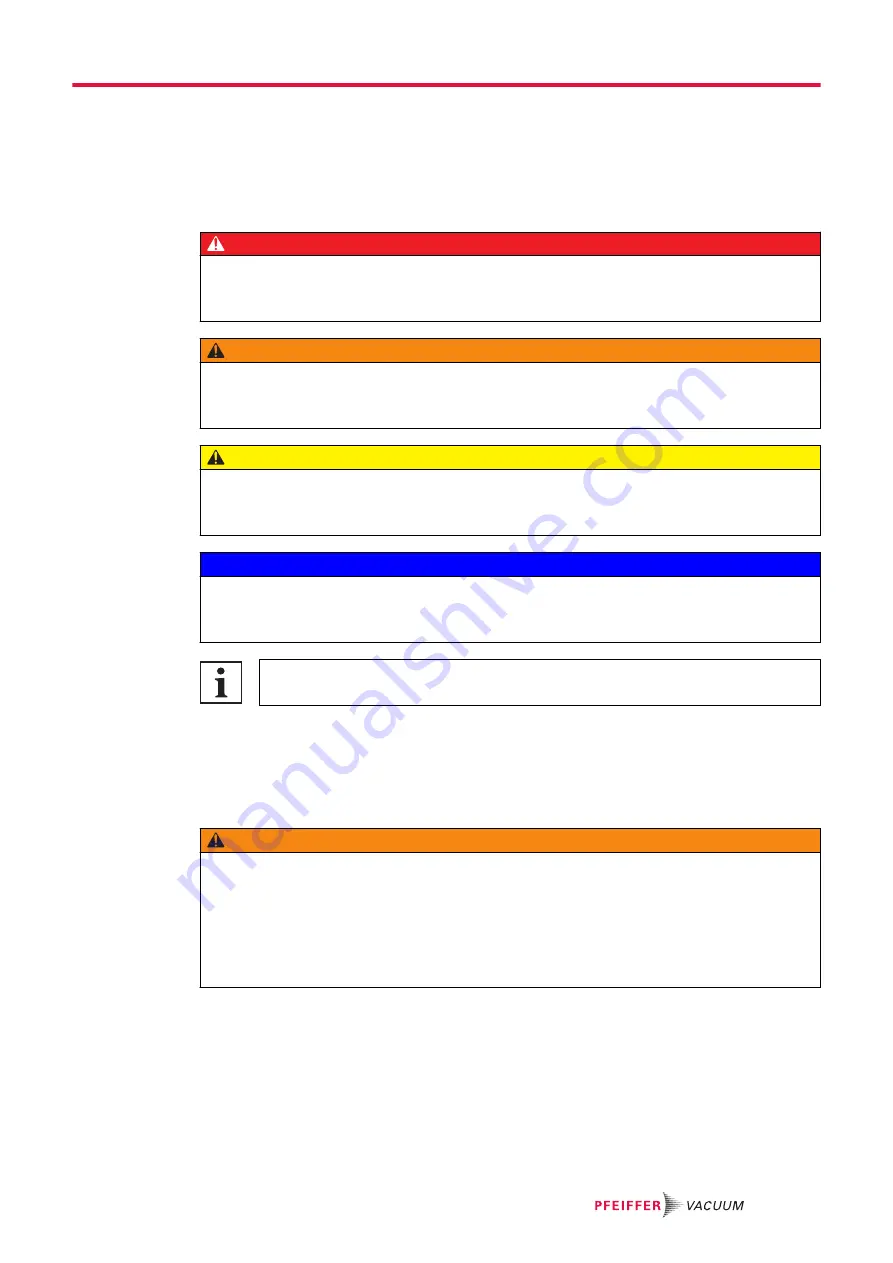
2 Safety
2.1 General safety information
The following 4 risk levels and 1 information level are taken into account in this document.
DANGER
Immediately pending danger
Indicates an immediately pending danger that will result in death or serious injury if not observed.
► Instructions to avoid the danger situation
WARNING
Potential pending danger
Indicates a pending danger that could result in death or serious injury if not observed.
► Instructions to avoid the danger situation
CAUTION
Potential pending danger
Indicates a pending danger that could result in minor injuries if not observed.
► Instructions to avoid the danger situation
NOTICE
Danger of damage to property
Is used to highlight actions that are not associated with personal injury.
► Instructions to avoid damage to property
Notes, tips or examples indicate important information about the product or about this docu-
ment.
2.2 Safety instructions
All safety instructions in this document are based on the results of the risk assessment carried out in
accordance with Machinery Directive 2006/42/EC Annex I and EN ISO 12100 Section 5. Where applica-
ble, all life cycle phases of the product were taken into account.
WARNING
Risk of crushing when the product is slung
Given the heaviness of the product, there is a risk of crushing during handling operations involving
lifting devices. Under no circumstances shall the manufacturer be liable if the following instructions
are not followed:
► Only qualified staff trained in handling heavy objects are authorized to handle the product.
► The lifting devices provided
must be used
and the procedures set out in this document must be
followed.
Safety
11/78