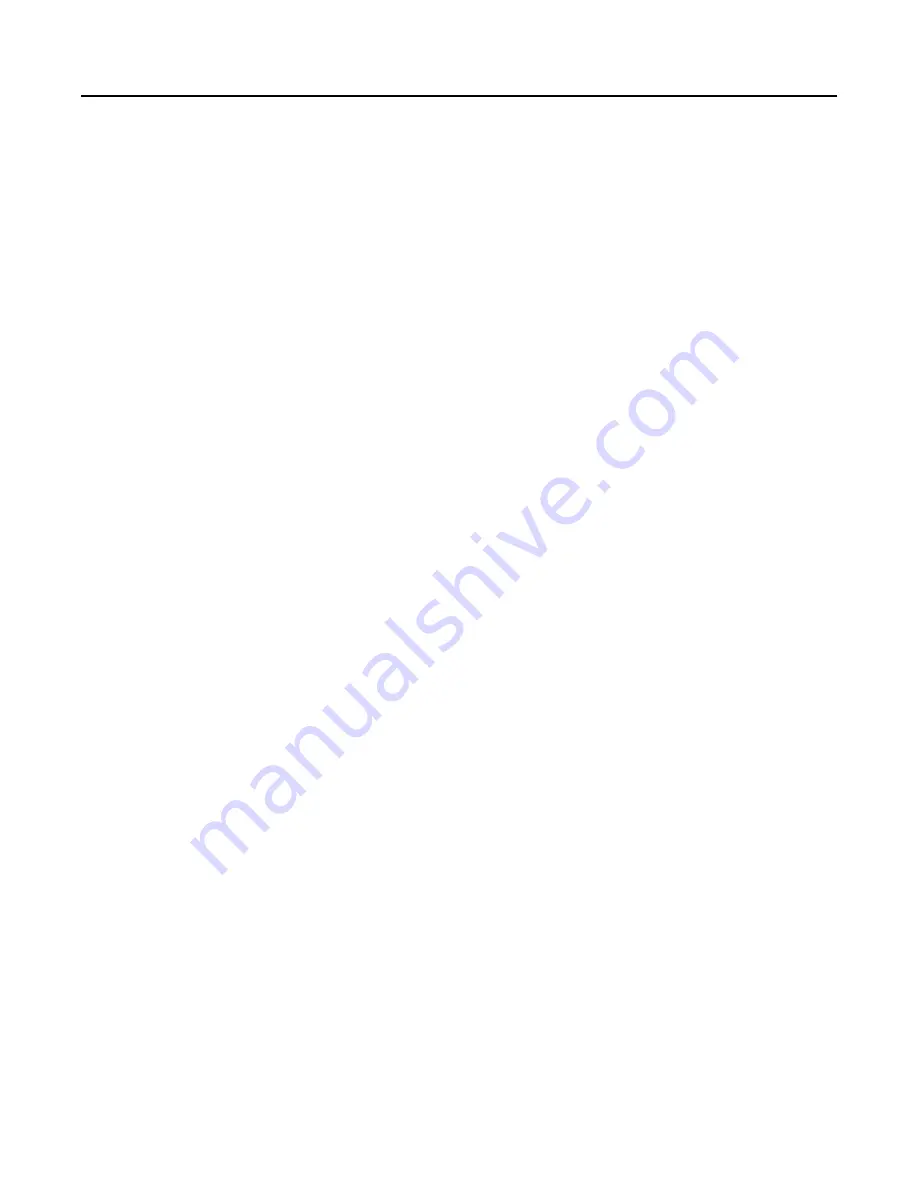
• For jump starting with cables in cold weather, refer
to the Operation and Maintenance Manual,
“Starting with Jump Start Cables.” for instructions.
Viscosity of the Engine Lubrication
Oil
Correct engine oil viscosity is essential. Oil viscosity
affects the amount of torque that is needed to crank
the engine. Refer to this Operation and Maintenance
Manual, “Fluid Recommendations” for the
recommended viscosity of oil.
Recommendations for the Coolant
Provide cooling system protection for the lowest
expected outside temperature. Refer to this
Operation and Maintenance Manual, “Fluid
Recommendations” for the recommended coolant
mixture.
In cold weather, check the coolant often for the
correct glycol concentration in order to ensure
adequate freeze protection.
Engine Block Heaters
Engine block heaters (if equipped) heat the engine
jacket water that surrounds the combustion
chambers. This heat provides the following functions:
• Startability is improved.
• Warm up time is reduced.
An electric block heater can be activated once the
engine is stopped. An effective block heater is
typically a 1250/1500 W unit. Consult your Perkins
dealer or your Perkins distributor for more
information.
Idling the Engine
When idling after the engine is started in cold
weather, increase the engine rpm from 1000 to 1200
rpm. This increase in RPM will warm up the engine
more quickly. Maintaining an elevated low idle speed
for extended periods will be easier with the
installation of a hand throttle. The engine should not
be “raced” in order to speed up the warm-up process.
While the engine is idling, the application of a light
load (parasitic load) will assist in achieving the
minimum operating temperature. The minimum
operating temperature is 82 °C (179.6 °F).
Recommendations for Coolant
Warm Up
Warm up an engine that has cooled below normal
operating temperatures due to inactivity. The warm-
up should be performed before the engine is returned
to full operation. During operation in very cold
temperature conditions, damage to engine valve
mechanisms can result from engine operation for
short intervals. This action can happen if the engine
is started and the engine is stopped many times
without being operated in order to warm up
completely.
When the engine is operated below normal operating
temperatures, fuel and oil are not completely burned
in the combustion chamber. This fuel and oil causes
soft carbon deposits to form on the valve stems.
Generally, the deposits do not cause problems and
the deposits are burned off during operation at
normal engine operating temperatures.
When the engine is started and the engine is stopped
many times without being operated in order to warm
up completely, the carbon deposits become thicker.
This action can cause the following problems:
• Free operation of the valves is prevented.
• Valves become stuck.
• Pushrods may become bent.
• Other damage to valve train components can
result.
For this reason, when the engine is started, the
engine must be operated until the coolant
temperature is 71 °C (160 °F) minimum. Carbon
deposits on the valve stems will be kept at a
minimum. The free operation of the valves and the
valve components will be maintained.
In addition, the engine must be thoroughly warmed in
order to keep other engine parts in better condition
and the service life of the engine will be generally
extended. Lubrication will be improved. There will be
less acid and less sludge in the oil. This lubrication
will provide longer service life for the engine
bearings, the piston rings, and other parts. However,
limit unnecessary idle time to 10 minutes in order to
reduce wear and unnecessary fuel consumption.
SEBU8352-02
31