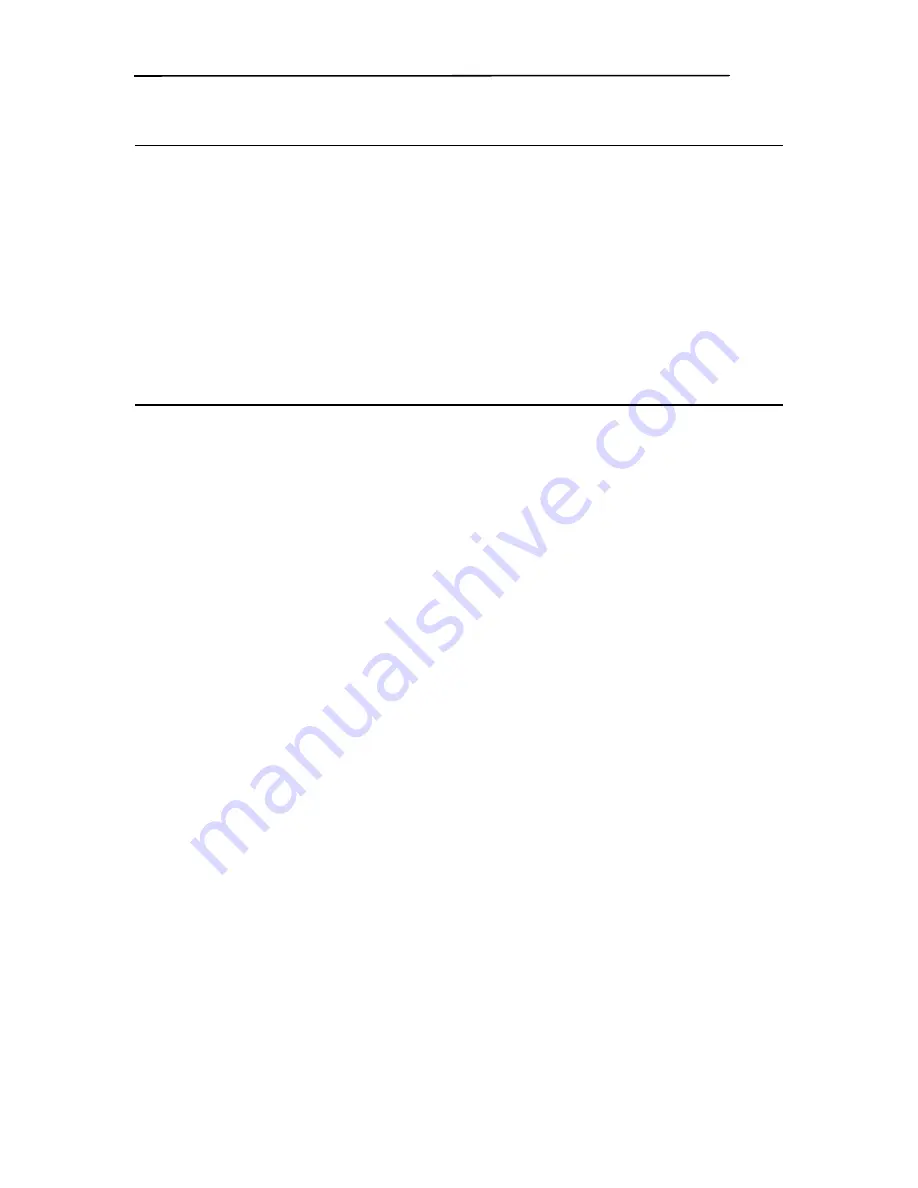
95
Specifications
Data System
Dispensable Volume:
Sample and Reagent: 1...99 uL, selectable in increments of 1
uL. Max. dispensable vol. 99 uL (sample reagent
volume). Flushing volume 1.3 mL, fixed.
Electronics:
The autosampler is powered from the spectrometer and is
software-controlled.
Data System
Description
Data Control:
Complete PC control using WinLab32 for AA software
operating under the Microsoft® Windows.
System Environment:
Provides complete control of the instrument and its major
accessories plus data handling and storage.
Data Handling:
Instrument readings linear in absorbance (-0.500 A to +2.000
A), concentration or emission intensity with continuously
variable scale expansion from 0.01 to 100 times. Integration
times operator-selectable from 0.1 to 120 sec. in increments of
0.1 sec. Reading modes include time-averaged integration,
non-averaged integration (peak area), and peak height
measurement. Includes built-in statistics. Up to thirty (30)
standards and a choice of proven calibration equations.
Reslope of the analytical curve using a single operator-selected
calibration standard.
Minimum PC Configuration
for system testing:
Factory Installed Operating System: Microsoft® Windows®7
Memory: 2 GB, Non-ECC, 1066 MHz, DDR3, 2 x 1GB, Four
DIMM slots
Furnace Autosampler
Description
Summary of Contents for PINAACLE 900 Series
Page 1: ...PINAACLE 900 SERIES Customer Hardware and Service Guide ATOMIC SPECTROSCOPY...
Page 2: ......
Page 3: ...PinAAcle 900 Series Customer Hardware and Service Guide...
Page 52: ...36 Safety Practices...
Page 55: ...39 Lab Space Requirements Dimensions and Weights Figure 2 1 Instrument dimenstions...
Page 84: ...68 Preparing Your Laboratory...
Page 91: ...75 The PinAAcle 900 Series Spectrometer System Figure 3 2 Optical System for the PinAAcle 900H...
Page 92: ...76 System Description Figure 3 3 Optical System for the PinAAcle 900T...
Page 93: ...77 The PinAAcle 900 Series Spectrometer System Figure 3 4 Optical System for the PinAAcle 900Z...
Page 101: ...85 Burner Assembly System Figure 3 8 Block diagram of the burner system...
Page 210: ...194 Preparing the System...
Page 310: ...294 Maintenance Figure 6 54 Window key Item Description 1 Window key 1...
Page 354: ...338 Maintenance...
Page 388: ...I 6 Index W WEEE Instructions 34 Weights 39 Windows cleaning 321 refitting 320 removing 318...
Page 389: ......