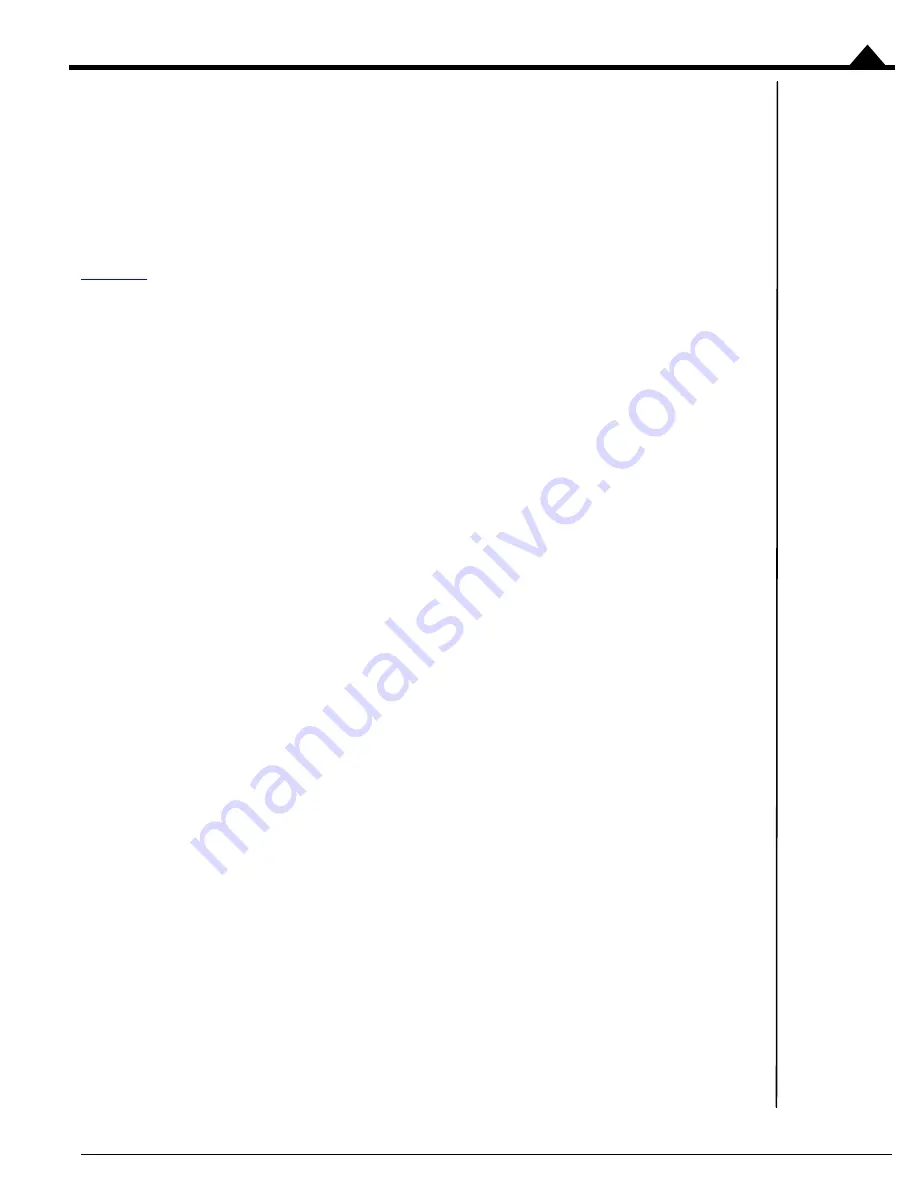
Application Notes — MC74113 & MC75113
Juno Step Motor Control IC User Guide
101
15
15.7 PWM High/Low Motor Drive With
Leg Current Sensing/Control
This section presents several design examples PWM high/low motor drive with leg current sensing. The examples
focus on different priorities including power rating, cost, and noise immunity.
15.7.1 Leg Current Sensing
shows an example for leg current sensing. Only phase A is shown here while the design for other legs are
the same.
This example has two functional sections. The first is the current sensing sensor, and the second is the analog signal
conditioning circuit.
In this example, the leg current sensor is a resistor, R2. Q1 and Q2 are the half-bridge power train for motor winding
phaseA. Current sensing resistor R2 senses the leg current in Q2, which equals the motor winding current when Q2
conducts.
Q2 is switching at the PWM frequency, and the voltage drop on R2 is proportional to the motor winding current when
Q2 is on. Therefore, the voltage signal is also a chopping signal. The signal is always sampled when Q2 is on to ensure
an accurate reading. Also, the voltage drop can be positive, negative or zero depending on the winding current
direction.
U1 and the passive parts are the analog conditioning circuit. It scales and filters the voltage signal on R2 and input to
the analog input pin CurrentA.
U1A is configured as a differential amplifier with R3=R5 and R1=R6. It amplifies the voltage drop across R2, which
is the differential voltage. It also attenuates the common mode noise including the noise on the power train.
D1 provide a 1.65V voltage bias source as half the 3.3V ADC range. This bias can be shared with current sensing
stages of other phases. With this voltage bias, R2 current is sensed in either direction.
By default, the MC74113 and MC75113 take 1.65V reading as zero current. Host commands can be sent to
compensate the error introduced by the offsets and tolerances of the current sensing circuit.
R4 and C1 is a low pass filter to reduce output noise. It also alleviates the signal glitch due to ADC sampling. R4 and
C1 have to be placed close to CurrentA pin. Please note, because the signal on R2 is a chopping signal at the PWM
frequency, the bandwidth of R4 and C1 should be much higher than the PWM frequency preventing signal distortion/
delay.
The gain of the current sensing circuit is
V
CurrentA
= I_leg*R2*R1/R3+1.65
For this example, it is
V
CurrentA
= I_leg*0.02*54.9/10.0+3.3/2= 0.1098*I_leg+1.65
I_leg is defined as positive flowing from the ground to Q2 as shown in the schematic. It is because the current out of
the half bridge and into motor winding is defined as positive.
Therefore, the current sensing range is ±15A. This current range should include the peak current during dynamic
regulation. For example, during acceleration, the instantaneous current could be twice of the continuous current or
even more.
With the continuous current and peak current known, the power rating of the current resistor can be determined. The
conservative design rule is to assume that the current will go through R2 continuously, and the power dissipation is