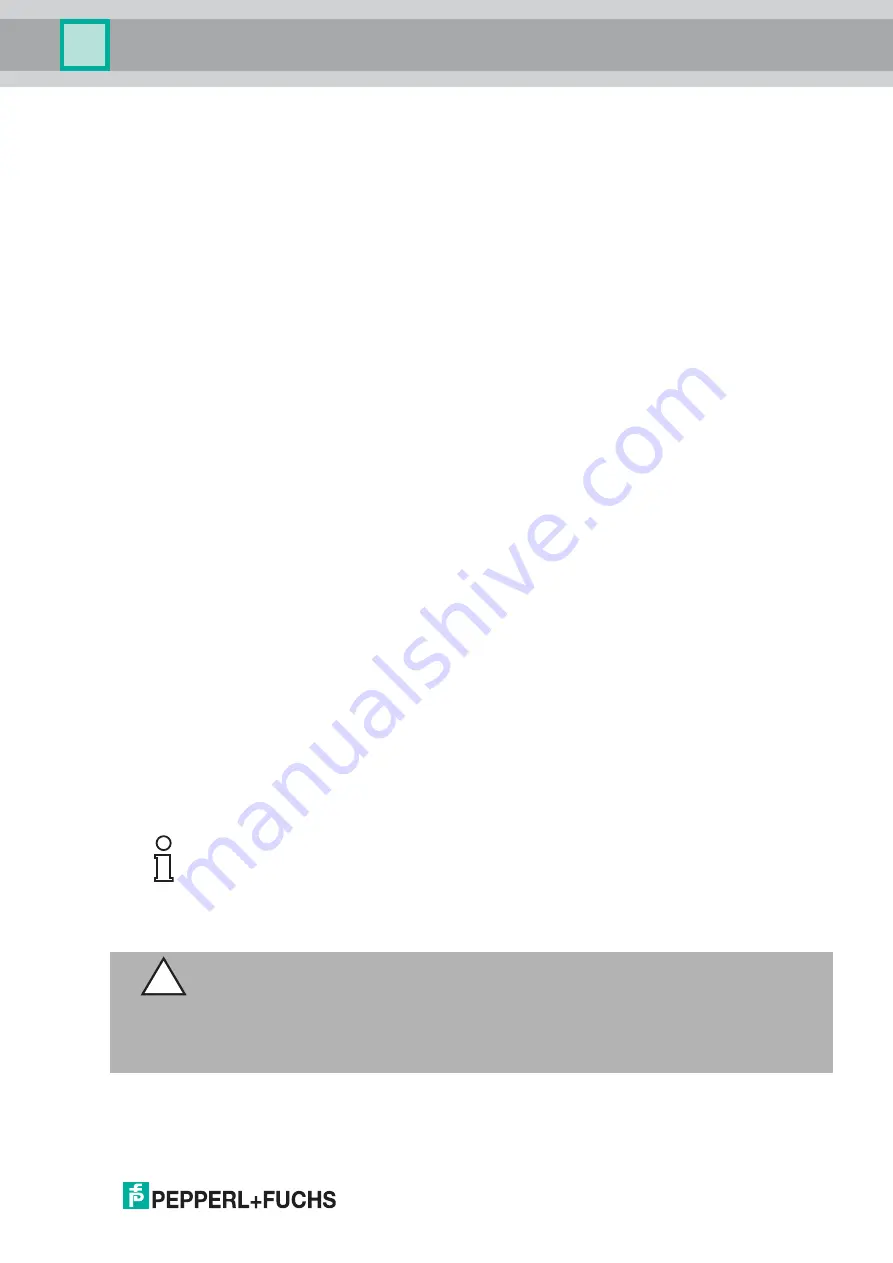
Output Function in Normal Operation
2
0
1
9
-0
2
19
8. Angular range outside of analog measurement range. The function of the analog output
depends on whether the output assumes the function of a voltage or a current output (de-
pending on the load).
Current output:
If the measurement range is exceeded, the analog output value adopts the error signal 3.6
mA. The current output issues this fault current until the position of the actuator falls within
the programmed analog measurement range again.
Voltage output:
If the measurement range is exceeded, the analog output value retains the last displayed
value until the position of the actuator falls within the analog measurement range again
(shown in the example).
9. Output signals
7.1
Function of Switching Outputs S1 and S2
The position of the actuator defined by the angular positioning system is based on half of the
actuator width (center of the actuator). The signaling zones are preset to the angle settings
120
°
... 125
°
(S1) and 240
°
... 245
°
(S2) at the factory. The switch-on and switch-off points of
the signaling zone can be programmed at any desired position. However, the minimum
signaling zone width is 5
°
.
If the actuator falls between S11 and S12 or S21 and S22 in the programmed signaling zone,
the corresponding switching output is activated. When a switching output is active, the
corresponding yellow LED lights up. If the actuator is positioned outside of a programmed
signaling zone, the relevant switching output changes to an idle state. When the actuator
leaves the detection area of the angular positioning system (loss of actuator), an active
switching output changes to an idle state ("up" position) and a switching output already in an
idle state remains in this state. The "Power/Error" LED lights up red when the actuator is lost.
7.2
Function of the Analog Output I/U
Function in normal operation
The position of the actuator defined by the angular positioning system is based on half of the
actuator width (center of the actuator). The start point of the analog output is preset to the
angular position 0
°
and the analog measuring range is set to a full 360
°
in the factory. The start
and end points of the analog measuring range can be defined by programming each relevant
angular position, the only restriction being that the analog measurement range must fall
between 90
°
and 360
°
.
After switching on, the angular positioning system automatically evaluates the load connected
at the analog output. If the load is a low resistance load (<400
Ω
), the analog output assumes
the function of a current output 4 mA ... 20 mA. If the load is a high resistance load (>3.3 k
Ω
),
the analog output assumes the function of a voltage output 0 V ... 10 V.
Note!
The impedance measurement and automatic determination of the output function
(current/voltage) only take place when the operating voltage is switched on. Any change made
to the load impedance during operation is no longer re-evaluated by the sensor. A load change
during operation can therefore cause the sensor to produce seemingly incorrect output logic.
Caution!
Make sure that the connected load is always low resistance (
≤
400
Ω
) or high resistance (
≥
3.3
k
Ω
).
If a load is connected with an impedance between 400
Ω
and 3.3 k
Ω
, this may result in
undefined output values because the sensor cannot fully control the analog output. The output
logic (current or voltage output) is not defined either.