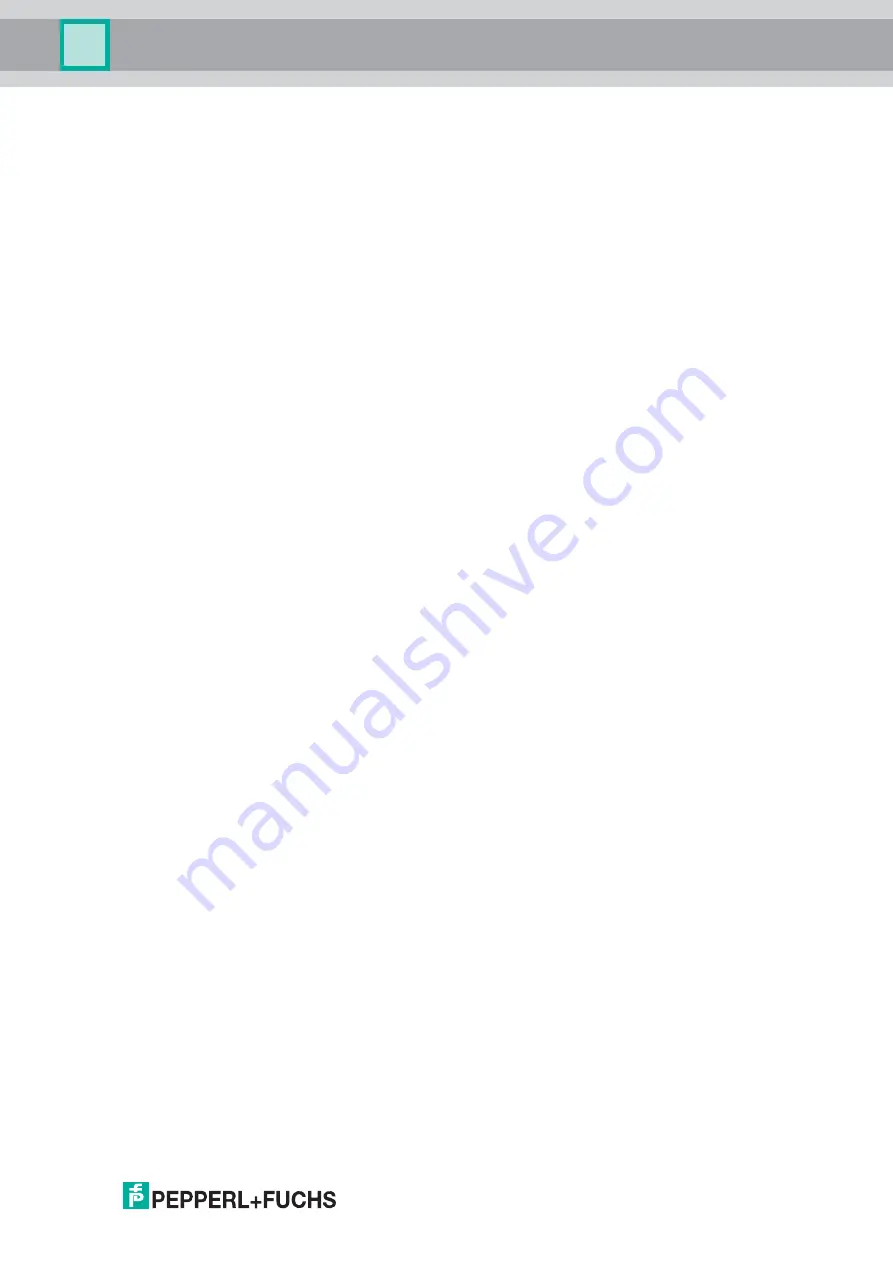
Functional Safety KFD2-CD-(Ex)1.32-**
Planning
201
8-11
13
3.5
Useful Lifetime
Although a constant failure rate is assumed by the probabilistic estimation this only applies
provided that the useful lifetime of components is not exceeded. Beyond this useful lifetime,
the result of the probabilistic estimation is meaningless as the probability of failure significantly
increases with time. The useful lifetime is highly dependent on the component itself and its
operating conditions
–
temperature in particular. For example, the electrolytic capacitors can
be very sensitive to the operating temperature.
This assumption of a constant failure rate is based on the bathtub curve, which shows
the typical behavior for electronic components.
Therefore it is obvious that failure calculation is only valid for components that have
this constant domain and that the validity of the calculation is limited to the useful lifetime
of each component.
It is assumed that early failures are detected to a huge percentage during the installation
and therefore the assumption of a constant failure rate during the useful lifetime is valid.
However, according to IEC/EN 61508-2, a useful lifetime, based on general experience,
should be assumed. Experience has shown that the useful lifetime often lies within
a range period of about 8 to 12 years.
As noted in DIN EN 61508-2:2011 note N3, appropriate measures taken by the manufacturer
and plant operator can extend the useful lifetime.
Our experience has shown that the useful lifetime of a Fuchs product can be higher
if the ambient conditions support a long life time, for example if the ambient temperature is
significantly below 60
°
C.
Please note that the useful lifetime refers to the (constant) failure rate of the device.
The effective life time can be higher.