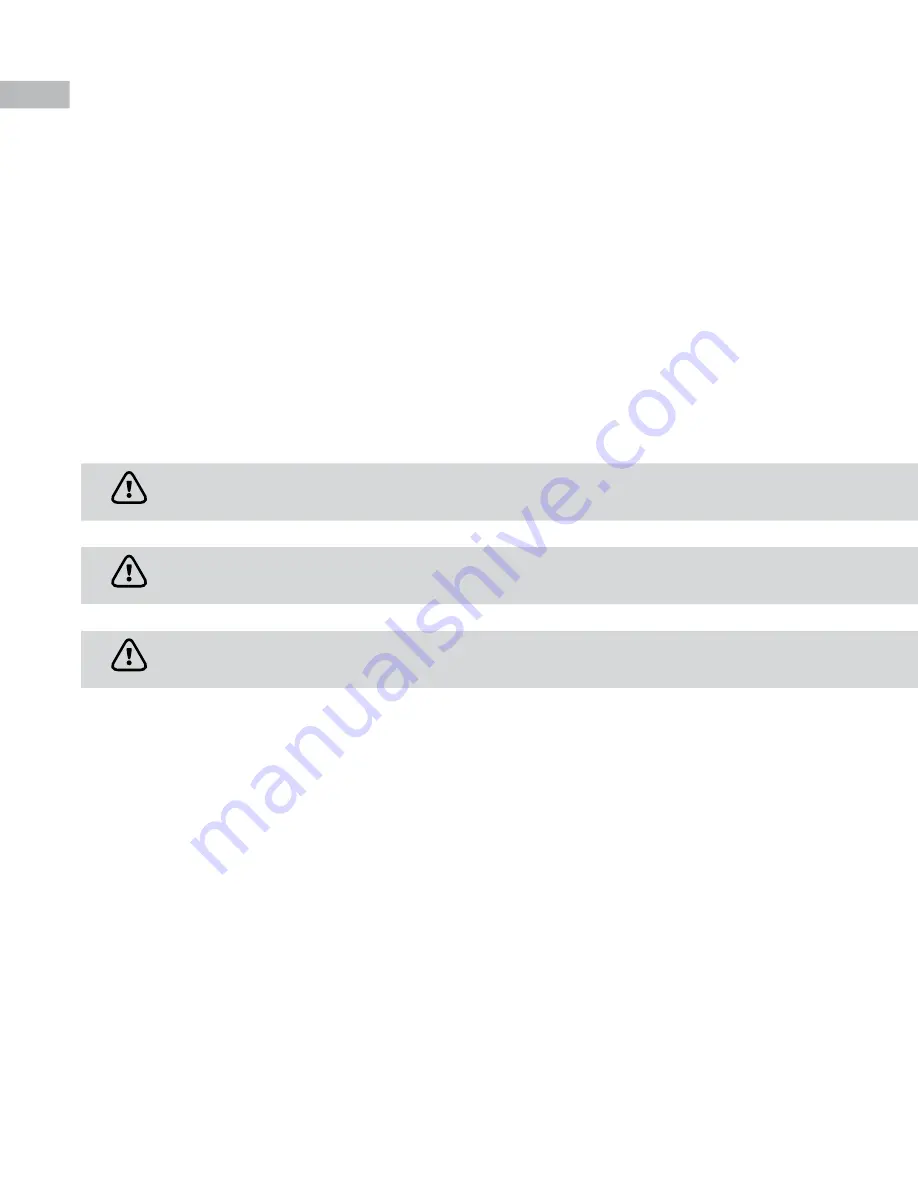
3
www.PennBarry.com
GENERAL SAFETY INFORMATION
Only qualified trained personnel should install or maintain equipment described in this document. Improper installation can result in
electric shock, possible injury due to high speed moving parts, or other potential hazards. Special circumstances such as high winds
or wet surfaces must be considered when installing the unit. Contact a PennBarry engineer if any questions or issues arise or if any
other information is needed before installing or maintaining the fan.
1. Follow all local, state and federal electrical and safety codes, as well as the National Electrical Code (NEC) and the National Fire
Protection Agency (NFPA) where applicable. Follow the Canadian Electrical Code (CEC) in Canada.
2. Make sure that the wheel spins freely without hitting or rubbing on any parts or objects.
3. The motor must be grounded; failure to ground a motor can result in a serious safety hazard.
4. The fan impeller should not be operated at RPM’s exceeding the rated RPM. If fan speed is higher than rated, the motor may
over amp, causing serious damage to the motor and other moving parts of the fan.
5. Power cord must be free of any kinks or pinches and must not come into contact with grease, oil or other liquids, flammable or
otherwise.
6. Verify that incoming power to the unit is of the correct voltage stated on the unit and/or motor nameplate.
7. Turn unit off before opening any access panels.
Receiving
PennBarry fans are carefully inspected and tested before leaving the factory. When the unit is received, inspect the packaging for any
signs of tampering. Inspect the unit for any damage that may have occurred during transit and check for loose, missing or damaged
parts. Mishandled units can void the warranty provisions. If units are damaged in transit, it is the responsibility of the receiver to
make all claims against the carrier. PennBarry is not responsible for damages incurred during shipment. Avoid severe jarring and/
or dropping. Handle units with care to prevent damage to components or finishes. If the unit is scratched due to mishandling, the
protective coating may be damaged. Incorrect lifting may damage the fan and void the warranty.
Unpacking
Upon reception, verify that all required parts and the correct quantity of each part have been received. If any items are missing,
report these to your local PennBarry representative. Due to variation in shipping carriers and availability, some items are shipped
separate from one another. Confirmation of shipment(s) must be limited to only items on the bill of lading.
Storage
Store in a dry, protected area being sure fan shaft, bearings and impeller are protected against dust and corrosion. If it is necessary
to store outdoors or within a building under construction, special care must be taken to prevent moisture, corrosion, dirt or
dust accumulation. Coat the shaft with grease or a rust preventative compound. Cover and seal bearings to prevent entrance of
contaminants. Impeller should be rotated at least once a month to circulate the grease in bearings. If stored outdoors over seven
(7) days, cover completely with a tarp or heavy waterproof paper. Electrical connections and leads must be protected from moisture.
Block impeller to prevent natural rotation. Do not allow material of any kind to be piled on top or inside of fan.
Always disconnect power before working on or near a fan. Lock and tag the service switch or breaker to prevent
accidental power up.
When servicing the fan, motor may be hot enough to cause pain or injury. Allow motor to cool before servicing.
Precaution should be taken in explosive atmospheres.
DANGER
CAUTION
CAUTION