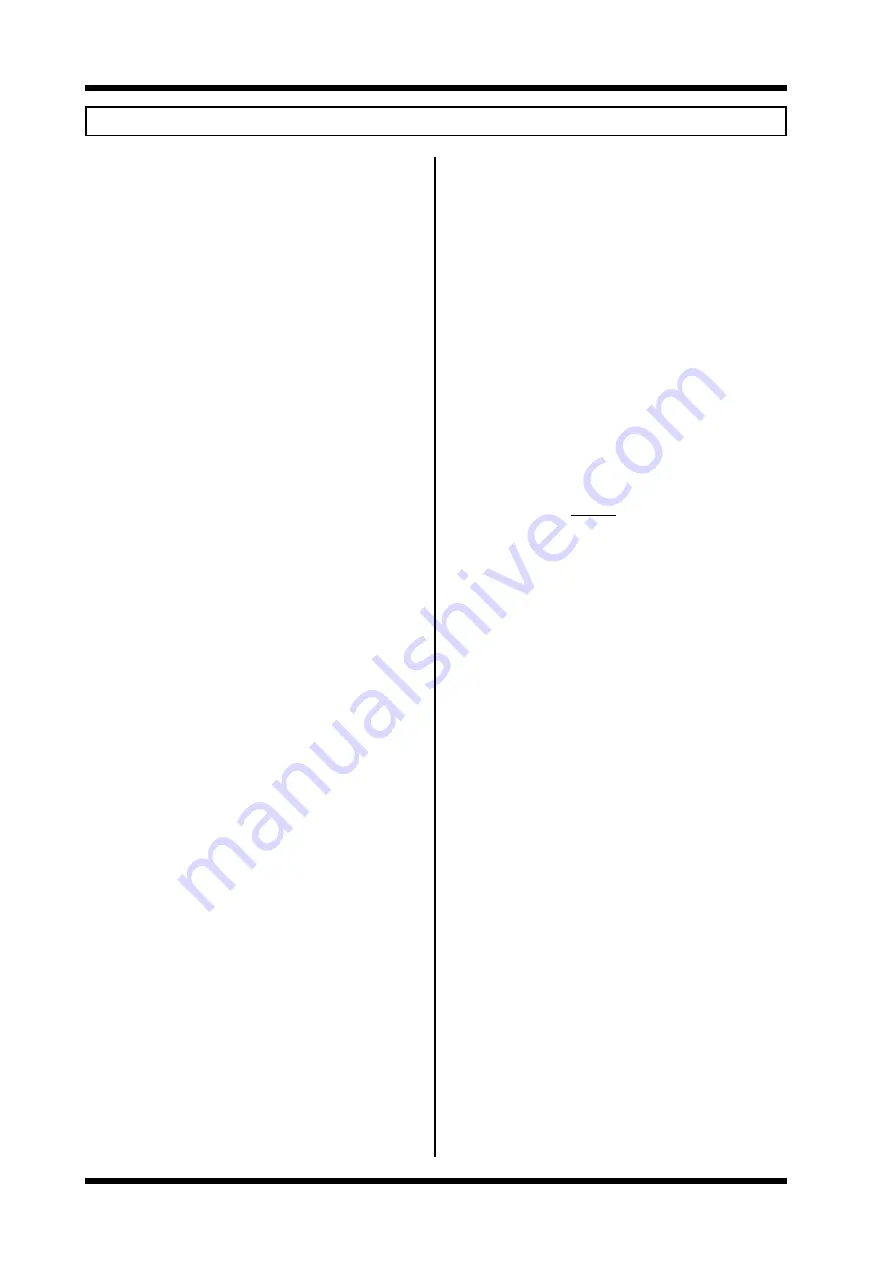
Microdrive Series Instruction Manual
4201-109 Rev I
40
PART 2 THE FULL FEATURES OF THE MICRODRIVE
2.1
INTRODUCTION TO THE FULL
FEATURES OF THE MICRODRIVE
Discussion in Part One - The Standard Microdrive of this
manual is limited to the basic essentials for use of the
Microdrive from the standard configuration.
The standard configuration is just one selection setting of a
large variety available in the Microdrive (refer to Table 2.1).
The process flexibility of the Microdrive only becomes
evident when its programmable features are employed.
This particularly refers to the ability to configure the
Microdrives operation in five specific areas (fig. 2.1):
- input frequency control source
- analogue output source
- process control, feedback
- relay outputs
- digital (switch) inputs
This configurability means that the Microdrive can often be
employed as a complete stand-alone process control
system.
Logic is also incorporated to cater for certain special
applications (e.g., crane control).
Some specific application set-ups are given in the
appendices.
2.2
CONTROL INPUT/OUTPUT
FUNCTIONAL DESCRIPTION AND
SPECIFICATION
Fig. 2.2 provides the complete electrical specification of all
Microdrive control inputs and outputs and includes
diagramatic descriptions. Each input is individually
described below. Further information (including specific
examples of connection) is presented in the detailed
descriptions of the relevant screen.
2.2.1 COMMON POINT ISOLATION
For safety reasons the Microdrive control PCB must be
linked to ground at some point in a control system. When
supplied the control PCB common point (0V) is connected
to ground via a link J2 = E (fig. 2.2). Where control wiring is
run to external control equipment (or other Microdrives)
there should be only one earth connection for the complete
control system (to prevent ground loops). If necessary, shift
open link J2, J2 = X.
2.2.2 INPUTS
010V Potentiometer Control Input
Voltage control input for reference frequency adjustment or
as a feedback source. It may be used for voltage control or
as potentiometer input source. The voltage level at this
input may be directly observed on Screen -3 at any time.
420mA Current Input
Current loop control input for reference frequency
adjustment or as a feedback source. Note that the current
return
(-connection) is common with the control PCB circuit 0V
connection. The current level may be directly observed on
Screen -3 at any time.
Motor PTC
PTC thermistor input for motor overheating protection. If
PTC protection is not required, this input must be linked to
0V.
Tacho Input
Pulse train input for tacho follower frequency reference
signal or speed control feedback signal. The pulse/
frequency ratio is defined by the tacho-gain parameter
(Screen 43).
Configurable (Multi-function) Digital Inputs
The switch (digital) input control lines of the Microdrive may
be configured to provide many alternative functions. Refer
to the detailed description of Screen 66 for a full description
of the inputs and their alternative configurations. The level
status of each of these inputs may be directly examined by
viewing Screen -3 at any time (1224V = 1; 0V = 0). Their
logical operation may be inverted. When supplied, these
inputs are set for active low operation (that is, they are
internally connected to bias high through the input logic bias
link as shown in fig. 2.2. To match the state, Screen 79
MFI INVERT is set to [N]O. Inversion of the logic (to pull
high to activate) is achieved by changing both link and
changing Screen 79 together.
WARNING:
Special care must be taken when altering
the input logical operation. Refer to detail of
Screen 79 in Part 2 - The Full Features of
the Microdrive.
Supply for control of active high inputs may be sourced from
Terminal 16 or alternatively an external 1224Vdc supply.
2.2.3 OUTPUTS
Configurable 010V Analogue Output
A voltage output which may be configured (Screen 70) to
represent several different internal signals. Suitable for
driving industrial voltmeters or further process controls.
Digital Frequency Output
A pulse train 26.25 times the Microdrive output frequency.
This pulse train (falling edge referenced) is specifically
intended for use with a PDL digital frequency display meter.
The digital frequency output range is dependent upon the
modulation mode selected (refer Screen 72).
Configurable Relay Outputs
Three voltage free 250Vac (30Vdc) 1A rated relay outputs
are provided for industrial interface. Each relay may be
programmed (Screens 6769) to switch according to one of
several possible output controls.
One changeover contact pair and two normally open
contacts are provided. Each relay has LED status
indication.
Tacho Supply
Power supply for the pulse tacho generator (encoder).
+10V Supply
Voltage reference signal for (1 kohm) potentiometer control.
Summary of Contents for D3-2.5
Page 2: ...Microdrive Series Instruction Manual 4201 109 Rev I 4201 003 Rev A Page 2 of 12...
Page 6: ...Microdrive Series Instruction Manual 4201 109 Rev I 4201 003 Rev A Page 6 of 12...
Page 12: ...Microdrive Series Instruction Manual 4201 109 Rev I 4201 003 Rev A Page 12 of 12...
Page 55: ...Microdrive Series Instruction Manual 4201 109 Rev I 55...
Page 74: ...Microdrive Series Instruction Manual 4201 109 Rev I 74...
Page 75: ...Microdrive Series Instruction Manual 4201 109 Rev I 75...
Page 76: ...Microdrive Series Instruction Manual 4201 109 Rev I 76...
Page 77: ...Microdrive Series Instruction Manual 4201 109 Rev I 77...
Page 78: ...Microdrive Series Instruction Manual 4201 109 Rev I 78...
Page 79: ...Microdrive Series Instruction Manual 4201 109 Rev I 79...
Page 80: ...Microdrive Series Instruction Manual 4201 109 Rev I 80...
Page 81: ...Microdrive Series Instruction Manual 4201 109 Rev I 81...
Page 82: ...Microdrive Series Instruction Manual 4201 109 Rev I 82...
Page 83: ...Microdrive Series Instruction Manual 4201 109 Rev I 83...
Page 112: ...Microdrive Series Instruction Manual 4201 109 Rev I 112...
Page 113: ...Microdrive Series Instruction Manual 4201 109 Rev I 113...