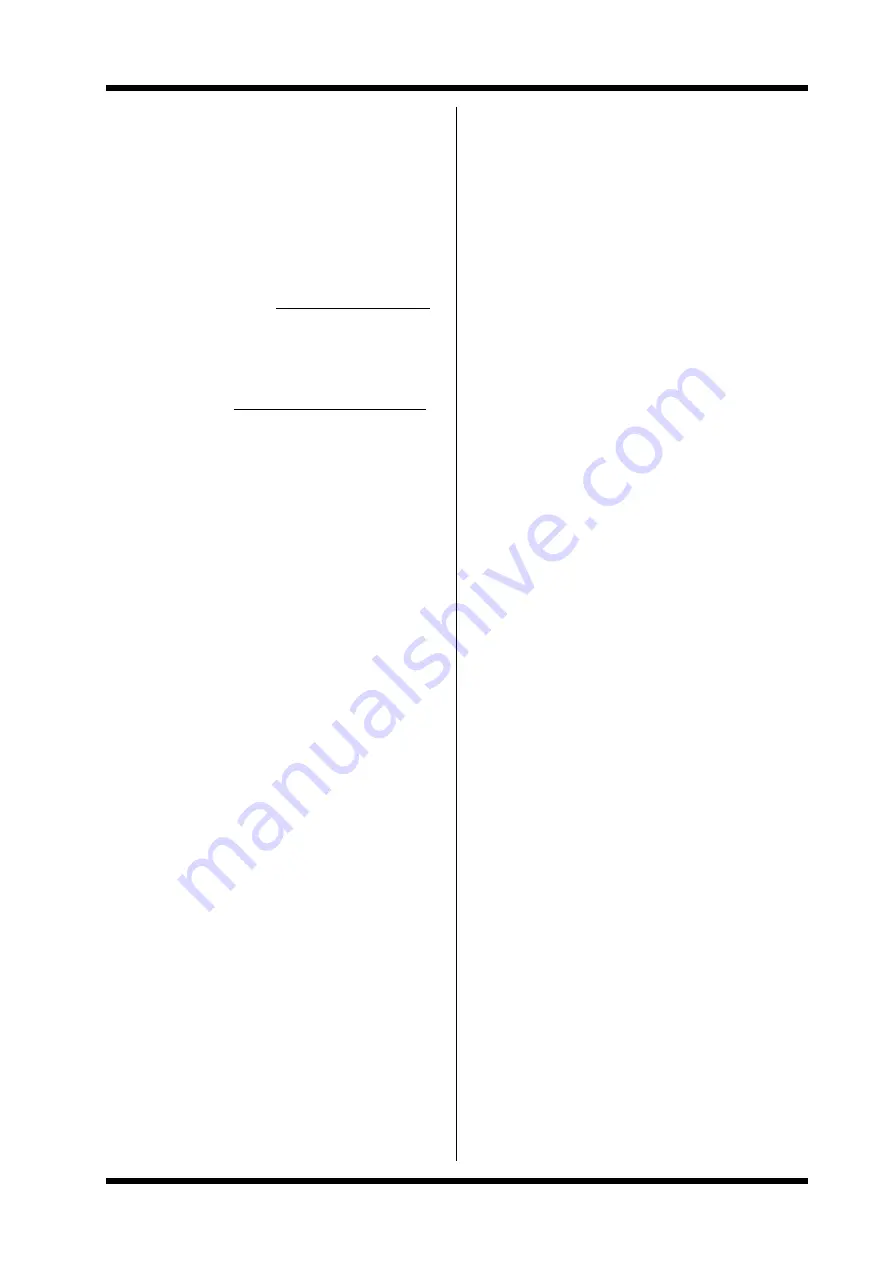
Microdrive Series Instruction Manual
4201-109 Rev I
21
to be considered. Be sure the box is large enough or has
sufficient clean airflow to provide effective cooling as
follows:
Estimate the average load power of the Microdrive :-
Pav(kW) = estimated average motor load
Knowing this power figure choose :-
EITHER
- a fully enclosed cabinet with an exposed
surface area and given inside/outside
temperature.
Exposed surface area (sq. m.) =
7.5 x Pav(kW)
(inside temp. - outside temp.)
OR
- if the cabinet is too large, air flow cooling will
be required. Calculate the appropriate flow of
air.
Airflow (cu.m./sec.) =
Pav(kW)
50 x (outlet air temp. - inlet air temp.)
A suitable convection or forced air system must be provided
to ensure the inside air temperature does not exceed 50°C.
1.2.2 MOUNTING THE MICRODRIVE
Microdrive-3 (UD3)
The Microdrive-3 (UD3) must be mounted vertically with
sufficient room (horizontally and vertically) between adjacent
Microdrives so that the maximum ambient air temperature
does not exceed 50°C.
Refer to fig. 1.3a for complete mechanical mounting details
for the Microdrive-3 (UD3).
Microdrive-i (UDi)
The Microdrive-i (UDi) can be mounted in three ways - wall
mounted, floor mounted (cabinet version only), and through
a switchboard gearplate:
UDi wall mounting:
As delivered, the UDi has mounting brackets attached to
the main heatsink as required for wall mounting.
UDi floor mounting:
The cabinet version of the UDi is able to be floor mounted.
The wall mounting brackets on the main heatsink may be
removed if required. The UDi is not suitable for free-
standing on the floor and should be securely fastened using
the floor mounting brackets provided.
UDi switchboard gearplate mounting:
Both the cabinet and the baseplate versions of the UDi may
be mounted through the back gearplate of a switchboard.
This allows the main heatsink cooling airflow to circulate
outside the switchboard - reducing the internal temperature
rise. In the case of the cabinet version of the UDi, the main
heatsink cooling air is kept separate from the switchboard
interior air, keeping the electronic components of the UDi
(and the switchboard interior) from being polluted by
external airborne contaminants.
If the Microdrive-i is through-wall mounted in a sealed
switchboard, the exposed surface area and/or the airflow
required may be reduced to 10% of the figure calculated in
Section 1.2.1 - Environmental Considerations.
Remove the wall mounting brackets from the main heatsink
before installation through the gear plate of the switchboard.
The UDi feet may be removed when mounting on the wall or
through a switchboard gear plate. If the UDi feet are
removed, do not mount the UDi directly on the floor as this
will block the airflow to the UDi heatsink cooling fan allow
at least the same height as the UDi feet for unimpeded
airflow to the heatsink.
Refer fig. 1.3b to fig. 1.3d for complete mechanical
mounting details for the Microdrive-i (UDi).
1.2.3 CONNECTING THE MICRODRIVE
Power Terminal Connections
Refer to fig. 1.4a for complete electrical wiring details for
the Microdrive-3 (UD3).
Refer to fig. 1.4b for complete electrical wiring details for
the Microdrive-i (UDi).
Control Terminal Connections
The 24-way control terminal strip is mounted across the
bottom of the Microdrive control electronics PCB (PDL Part
No. 0265-601). Pass the control electronics PCB external
control wiring into power cable termination cubicle. A
grommet cut-out is provided in the sealing plate at the
bottom of the UDi power electronics enclosure. Loom
control wiring and power wiring separately.
The control terminal strip is constructed of cage clamp
terminals. Care must be taken to avoid stripping their
threads or damaging the cage assembly by excessive
tightening.
Recommendations for control terminal wiring connections:
Recommended tightening torque :
0.5Nm
Maximum tightening torque
:
1.0Nm
Maximum cable size
:
1.1mm² appliance
wire
Maximum number of cables
per terminal
:
2
1.2.4 LARGE FRAME-SIZE MOTOR CONSIDERATIONS
Large frame-size motors (typically greater than 315 frame)
have additional installation requirements when used with AC
motor controllers. These motors may exhibit rotor voltage
build-up due to parasitic capacitances. Unless protective
measures are taken, this voltage may discharge through the
anti-friction bearings possibly leading to degradation of the
bearing via electrical discharge machining (EDM).
The preferred solution is to fit insulated bearings (or an
insulated bearing housing) with a rotor earthing brush.
Careful selection of the rotor earthing brush is required, as
this brush must provide a low impedance earth for high
frequency pulses. Rotor shaft earthing brushes are now
commercially available to suit this low voltage, low current
application. These brush systems are designed for long life
with minimal maintenance. Contact PDL Electronics or its
agent for further information on suitable earthing brushes.
An alternative solution is available from PDL Electronics in
the form of the Motor Voltage Optimiser. The MVO actively
filters out the common mode voltage applied to the motor.
Contact PDL Electronics or its agent for further information
on the Motor Voltage Optimiser.
Summary of Contents for D3-2.5
Page 2: ...Microdrive Series Instruction Manual 4201 109 Rev I 4201 003 Rev A Page 2 of 12...
Page 6: ...Microdrive Series Instruction Manual 4201 109 Rev I 4201 003 Rev A Page 6 of 12...
Page 12: ...Microdrive Series Instruction Manual 4201 109 Rev I 4201 003 Rev A Page 12 of 12...
Page 55: ...Microdrive Series Instruction Manual 4201 109 Rev I 55...
Page 74: ...Microdrive Series Instruction Manual 4201 109 Rev I 74...
Page 75: ...Microdrive Series Instruction Manual 4201 109 Rev I 75...
Page 76: ...Microdrive Series Instruction Manual 4201 109 Rev I 76...
Page 77: ...Microdrive Series Instruction Manual 4201 109 Rev I 77...
Page 78: ...Microdrive Series Instruction Manual 4201 109 Rev I 78...
Page 79: ...Microdrive Series Instruction Manual 4201 109 Rev I 79...
Page 80: ...Microdrive Series Instruction Manual 4201 109 Rev I 80...
Page 81: ...Microdrive Series Instruction Manual 4201 109 Rev I 81...
Page 82: ...Microdrive Series Instruction Manual 4201 109 Rev I 82...
Page 83: ...Microdrive Series Instruction Manual 4201 109 Rev I 83...
Page 112: ...Microdrive Series Instruction Manual 4201 109 Rev I 112...
Page 113: ...Microdrive Series Instruction Manual 4201 109 Rev I 113...