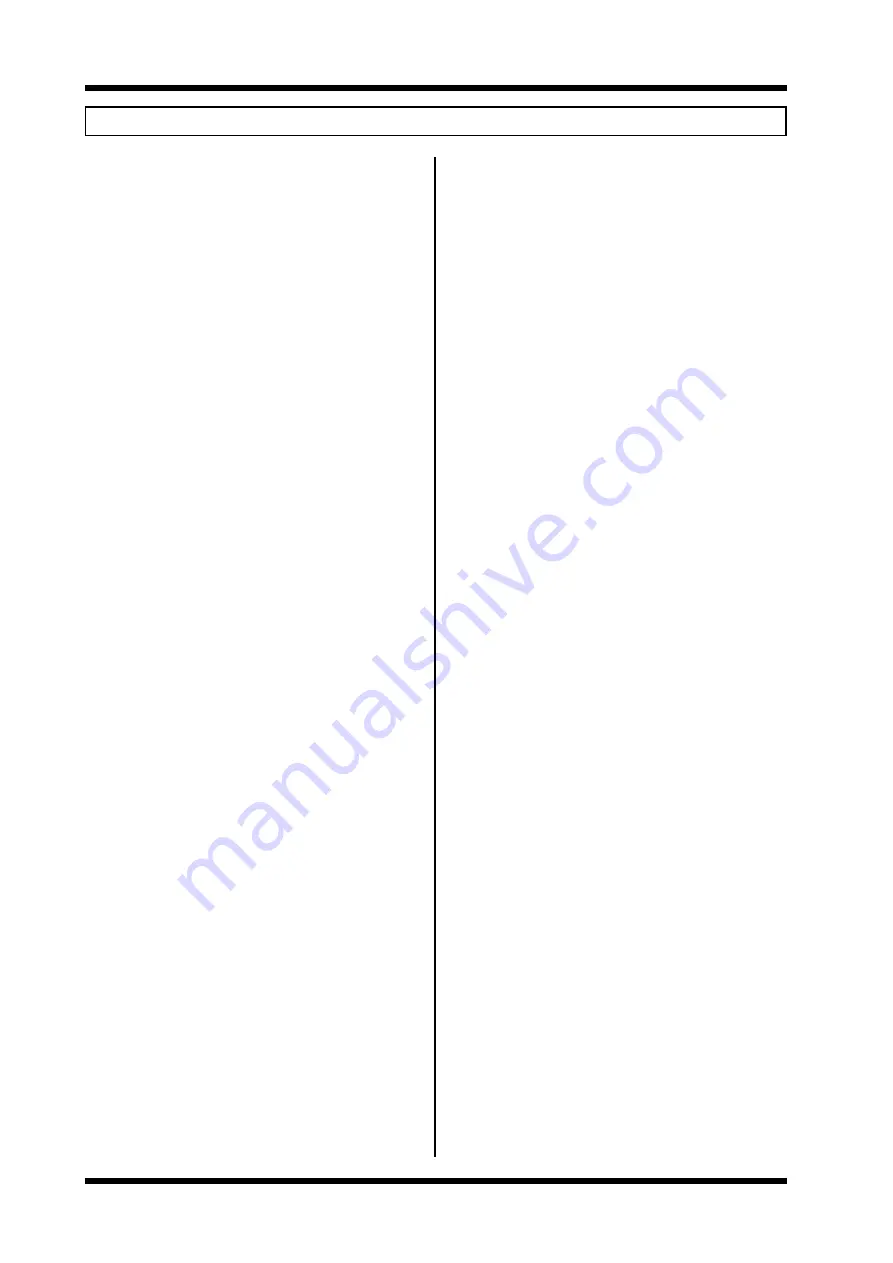
Microdrive Series Instruction Manual
4201-109 Rev I
20
PART 1
THE STANDARD MICRODRIVE
Other useful techniques include:
The use of a six pole motor in a four pole
application (Microdrive operates around 75Hz
instead of 50Hz) this gives better motor cooling
(hence a wider useful speed range) and 50% better
starting torque at very little extra motor cost.
Small motors may often be connected in 230V
(delta) connection. Using this connection on a
Microdrive (motor voltage set to 230V) on a 400V
supply allows the motor to be operated with full flux
up to 87Hz, thus providing a very wide constant
torque speed range. Note that the motor in fact
produces 1.7 times its rated power when operated
at 87Hz. The penalty is that the motor draws 1.7
times more current (because of the delta
connection), so a larger Microdrive may be required.
Other recommendations:
Regardless of how good a thermal overload or
model is, a PTC thermistor in the motor windings
provides the ultimate thermal protection and is
recommended. The Microdrive accepts standard
PTCs directly.
Always specify motors with high temperature
insulation at least class F or better.
1.2
INSTALLATION
1.2.1 ENVIRONMENTAL CONSIDERATIONS
The Microdrive must be sited in a suitable environment. As
with all equipment, the cleaner, cooler and more vibration
free the environment, the longer and more trouble free will
be the life of the Microdrive.
The ambient temperature should not be below 0°C, and must
not exceed the Microdrive specification of 50°C; relative
humidity should be less than 90% and there must be no
condensation. Avoid mounting the Microdrive in direct
sunlight.
The UD3 has a protection rating of IP21 and must have a
clean environment (Pollution degree 2), free of electrically
conductive (wet or dry) dust (e.g., carbon fibre, salt, etc.),
and free of spraying water.
The cabinet version of the UDi is protected against dust and
splashing water (Pollution degree 3). The UDi should not
be hosed down.
The baseplate version of the UDi must have a clean
environment (Pollution degree 2), free of electrically
conductive (wet or dry) dust (e.g., carbon fibre, salt, etc.),
and free of spraying water. The baseplate version of the
UDi is designed for mounting in a switchboard.
If mounting the Microdrive in a switch board be sure to allow
for sufficient cooling. The switchboard interior air
temperature must not exceed the Microdrive specification of
50°C. Calculate the correct airflow by using the formula
below and also consulting Section 1.2.2 - Mounting the
Microdrive.
In some applications it may be desirable to improve the
conditions in which the Microdrive is to be fitted. The first
choice in this case is to fit the Microdrive remotely in a clean
location.
If remote location is not practical, a protective box may have
1.1
APPLICATION RECOMMENDATIONS
The Microdrive is suitable for controlling the speed of all
standard three phase induction motors. Choose a
Microdrive which is capable of supplying the full load current
of the motor(s) to be driven.
When the Microdrive is correctly adjusted, full torque can be
obtained from the motor at up to rated speed. A standard
motor may be operated above rated speed by using higher
than rated frequency, but the torque that is able to be
generated declines (1/f) as there is insufficient voltage to
provide correct stator flux.
Operation below rated speed must take account of the
reduced cooling efficiency of the motor. Because of thermal
limitations, the continuous capability of the motor reduces
from rated torque at rated speed, to the value defined by the
zero speed cooling value at zero speed. The Microdrive
thermal model (overload) takes these factors into account
and provides safe protection from inadvertent overload of
this type. More detail is provided in Part 2 - The Full
Features of the Microdrive.
The quality of the Microdrive current waveform is such that
no derating of the motor torque due to harmonic heating is
necessary.
In a safety situation motors may be switched on and off the
Microdrive while it is running but this is not good control
practice it stresses the Microdrive and may lead to
occasional tripping due to arcing of the contact terminals. A
more elegant control solution is to use the Microdrive
control terminals.
Generally it is better practice to leave electronic equipment
(including the Microdrive) permanently connected to the
mains supply. Switching the mains on and off to control the
Microdrive is bad practice and should be avoided (use the
control terminals). If mains switching is insisted upon (!), it
must not occur more often than once every 5 minutes or the
Microdrive-3 (UD3) charging circuits may be damaged. The
Microdrive-i (UDi) has a SCR controlled soft-charge input
circuit and does not suffer from multiple charging cycle
limitations.
Several motors may be operated at once on the Microdrive,
but individual protection must be supplied. Be sure to
choose a Microdrive which is capable of supplying the total
current requirements of all of the motors. If you plan to
start motors independently direct-on-Microdrive then you
must also include the DOL starting current of the motors
(this generally leads to gross oversizing of the Microdrive
a much better solution is to stop the Microdrive, connect the
extra motors, and restart the Microdrive).
An advantage of the Microdrive is that non-standard motors
(frequency, voltage) can be driven from standard mains.
The Microdrive may be set to drive any motor with a rated
voltage between 10 and 995Vac, and any rated frequency
between 10 and 250Hz.
When selecting the gearing of your system, be sure to
operate the motor as near to rated speed as possible.
Centring your speed range around rated speed (so that
maximum speed actually overspeeds your motor) gives
better motor cooling and utilisation.
Summary of Contents for D3-2.5
Page 2: ...Microdrive Series Instruction Manual 4201 109 Rev I 4201 003 Rev A Page 2 of 12...
Page 6: ...Microdrive Series Instruction Manual 4201 109 Rev I 4201 003 Rev A Page 6 of 12...
Page 12: ...Microdrive Series Instruction Manual 4201 109 Rev I 4201 003 Rev A Page 12 of 12...
Page 55: ...Microdrive Series Instruction Manual 4201 109 Rev I 55...
Page 74: ...Microdrive Series Instruction Manual 4201 109 Rev I 74...
Page 75: ...Microdrive Series Instruction Manual 4201 109 Rev I 75...
Page 76: ...Microdrive Series Instruction Manual 4201 109 Rev I 76...
Page 77: ...Microdrive Series Instruction Manual 4201 109 Rev I 77...
Page 78: ...Microdrive Series Instruction Manual 4201 109 Rev I 78...
Page 79: ...Microdrive Series Instruction Manual 4201 109 Rev I 79...
Page 80: ...Microdrive Series Instruction Manual 4201 109 Rev I 80...
Page 81: ...Microdrive Series Instruction Manual 4201 109 Rev I 81...
Page 82: ...Microdrive Series Instruction Manual 4201 109 Rev I 82...
Page 83: ...Microdrive Series Instruction Manual 4201 109 Rev I 83...
Page 112: ...Microdrive Series Instruction Manual 4201 109 Rev I 112...
Page 113: ...Microdrive Series Instruction Manual 4201 109 Rev I 113...