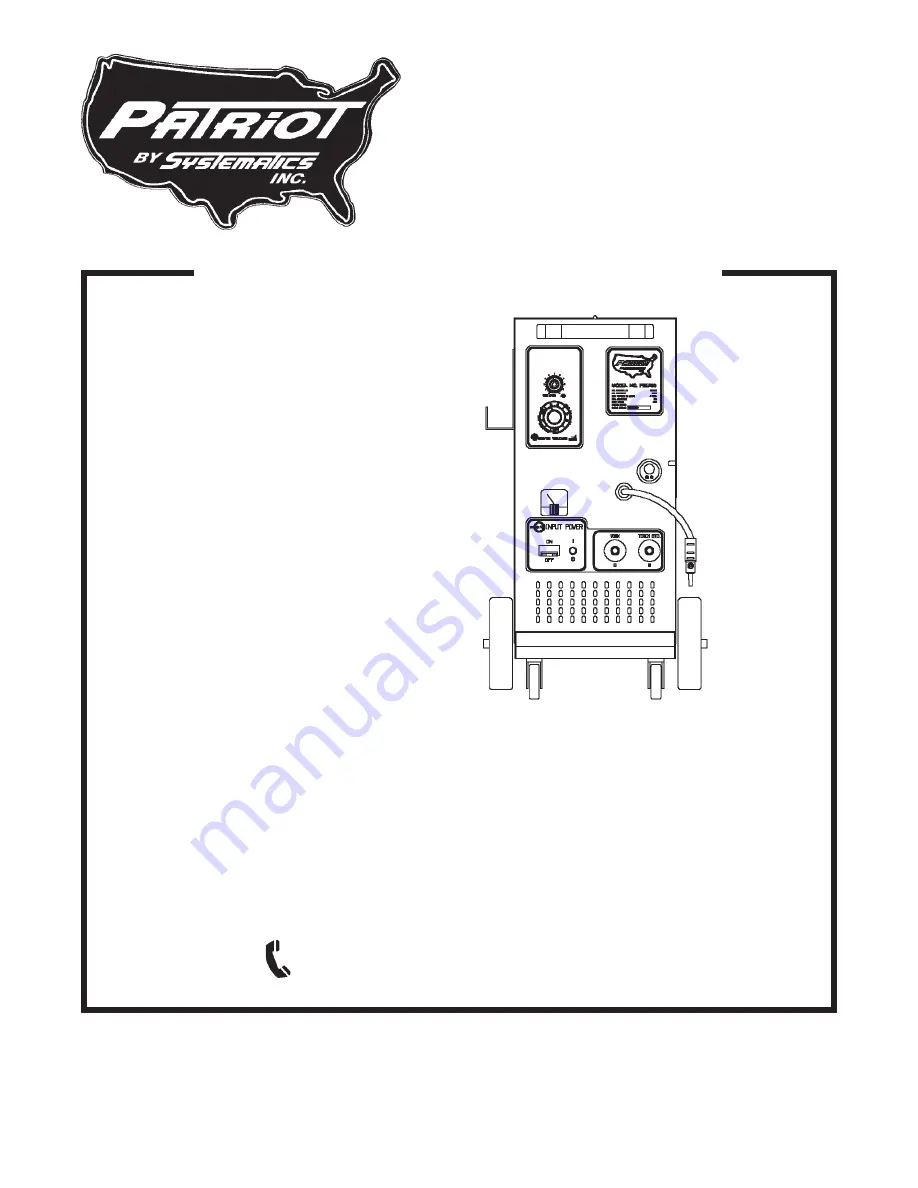
PBE250 M.I.G. COMBINATION UNIT
OWNER'S MANUAL
CONGRATULATIONS!
YOU HAVE JUST PURCHASED ONE OF THE FINEST
MIG WELDING SYSTEMS AVAILABLE TODAY. THE
PBE250
REPRESENTS FOURTH GENERATION TECH-
NOLOGICAL ADVANCEMENTS. THIS SYSTEM IS DE-
SIGNED AND ENGINEERED TO PROVIDE YOU WITH
YEARS OF PROFESSIONAL SERVICE.
INSTALLATION
OPERATION
MAINTENANCE
FORM WC5369
Rev. 8/00, 5/01
FOR TECH. SERVICE, CALL 1-610-696-9040