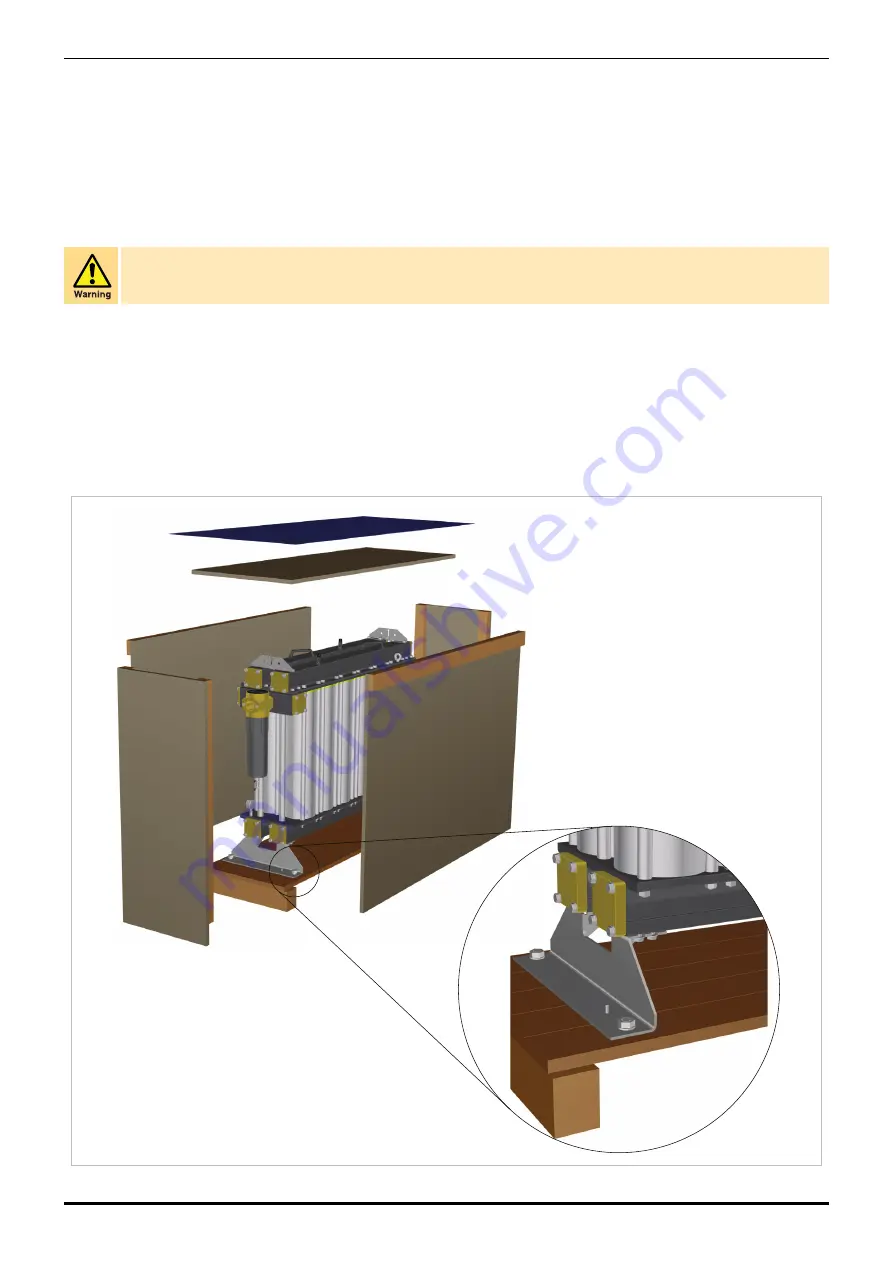
4
2.4 Receiving and Inspecting the Equipment
On receipt of the equipment carefully inspect the packaging for damage. If the packaging is damaged inform the delivery company immediately
and contact your local Parker Hannifin office.
2.4.1 Storage
If the equipment is to be stored prior to installation, do not remove it from the packaging. Ensure that it is stored in an upright position as
indicated by the arrows on the packaging.
Note.
The storage area should be secure and the environmental conditions should fall within those specified in the technical specification.If the
equipment is stored in an area where the environmental conditions fall outside of those specified, it is essential that it be moved to its final
location (installation site) and left to stabilise prior to unpacking. Failure to do this could cause condensing humidity and potential failure of the
equipment.
2.4.2 Unpacking
Remove the lid and all four sides of the packing crate. Carefully move the unit to its final location using a forklift truck or pallet truck. Once in it’s
final location, remove the unit from the pallet via the 4x bolts.
Note: Suitable slings and an overhead crane maybe required depending on the product size.
Do not attempt to lift the equipment by yourself. It is recommended that the equipment be carried by a minimum of two persons or
transported on a pallet truck.
Summary of Contents for PCO2
Page 15: ...12 C D F E...
Page 18: ...15 C D F E...