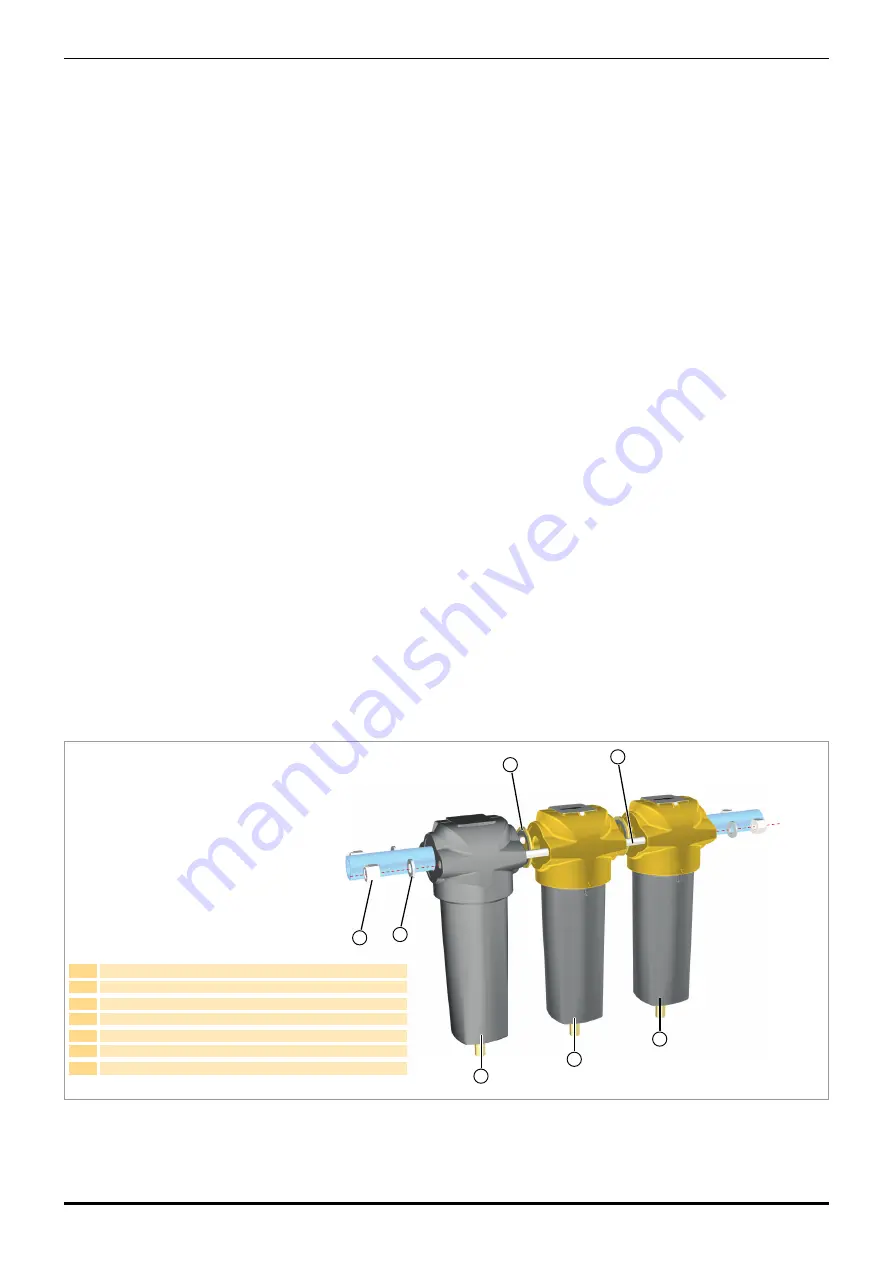
9
3.2 Locating the Equipment
3.2.1 Environment
The equipment should be located indoors in an environment that protects it from direct sunlight, moisture, and dust. Changes in temperature,
humidity, and airborne pollution will affect the environment in which the equipment is operating and may impair the safety and operation. It is the
customers' responsibility to ensure that the environmental conditions specified for the equipment are maintained.
3.2.2 Space Requirements
The equipment should be mounted on a flat surface capable of supporting its own weight plus the weight of all ancillary parts. The minimum
footprint requirements are specified below, however there must be adequate space around the equipment to allow airflow and access for
maintenance purposes and lifting equipment. A minimum spacing of approximately 500mm (20 ins) is recommended around all sides of the unit
and 1000m (39.4 ins) above it. The pump should have a minimum spacing of 100mm (4ins) around all sides.
Do Not
position the equipment so that it is difficult to operate.
3.3 Mechanical Installation
3.3.1 General Requirements
Ensure that each filter condensate drain is suitably piped away and any effluent is disposed of in accordance with local regulations.
It is important to ensure that all piping materials are suitable for the application, clean and debris free. The diameter of the pipes must be sufficient
to allow unrestricted inlet air supply to the equipment and outlet air supply to the application.
When routing the pipes ensure that they are adequately supported to prevent damage and leaks in the system.
All components used within the system must be rated to at least the maximum operating pressure of the equipment. It is recommended that the
system be protected with suitably rated pressure relief valves.
3.3.2 Securing the Unit
Mounting holes are provided in the feet of the unit. Once the unit has been positioned in its final location ensure that it is securely fixed in place.
3.3.3 Filter Installation
Multiple filters can be installed using the appropriate tie rod kits. Install the filters as illustrated in a vertical position ensuring that they are properly
secured.
Note: Before positioning the o-ring onto the filter ports, lubricate with a suitable acid free petroleum jelly.
1
2
3
4
5
6
7
1
Water separator
2
General purpose filter
3
High efficiency filter
4
Tie rod
5
Dowty seal
6
M6 Washer
7
M6 Nylock nut