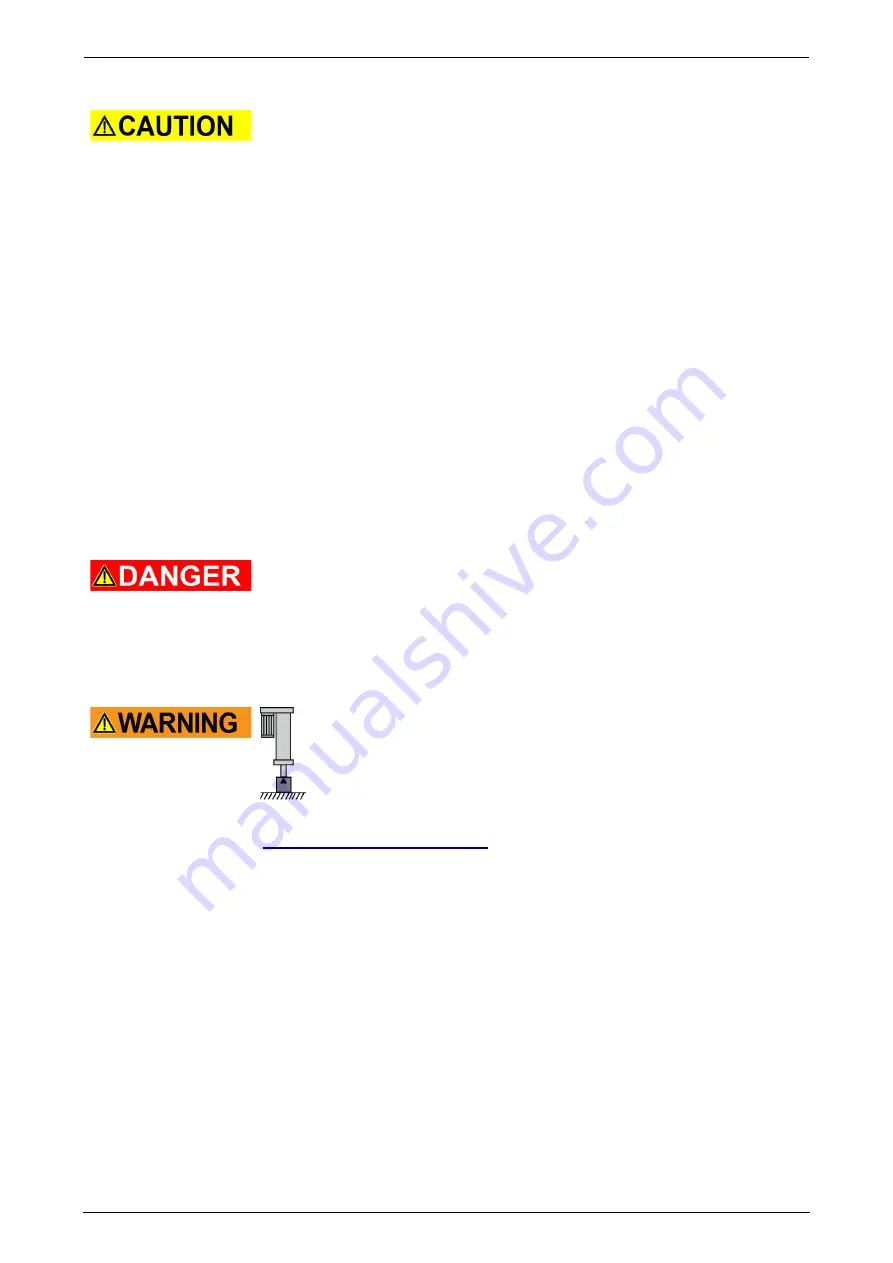
Parker EME
Motor/ gear assembly
23
192-550002N10 ETH March 2019
Please add the respective safety travels to the mentioned values!
Stroke, Usable Stroke and Safety Travel: see ETH catalogue
(solutions.parker.com/ETH_support).
Sensors and limit switches: see ETH catalogue
(solutions.parker.com/ETH_support).
Adjusting the machine reference initiator
The correct position for the home switch (machine zero switch) depends on the
application.
It is recommended to set the machine zero at or near the end of the travel. This
saves time, as it minimizes the chance that the machine zero is searched for in the
wrong direction. In some cases it is possible to use one of the limit switches as
machine zero. This method provides however a reduced precision, as the resulting
position can normally not be and-linked with the encoder index pulse.
2.3
Motor/ gear assembly
Notes on motor wiring
In order to adhere to the EMC directive, it is necessary to mount the motor if ever
possible unchanged. If you require a longer cable, the entire line should be
replaced with the same or a similar cable.
If you mount a connector on the new cable, please make sure that the 360° motor
cable shielding is maintained and that there is no connection to earth via the
connector housing.
Improper wiring may lead to severe injuries or death.
A wiring must always be made from a skilled electrician.
The motor must be grounded with a separate PE protective lead (green/yellow,
cross-section at least 2.5 mm
2
).
This cable must be connected to the available motor-ground connector or - if there
is non available - with a mounting screw. In the latter case, the coloring under the
head of the screw must be removed.
The internal ballscrew is not self-locking!
Always take care, especially in vertical position of the ETH cylinder that
the piston rod must be safeguarded!
In case of non respect severe injuries may occur.
In this chapter you can read about:
Motor / gear assembly with inline motor configuration ..................................................... 24
Motor / gearbox mounting with parallel motor configuration ............................................. 26
IP65 motor mount ............................................................................................................ 33