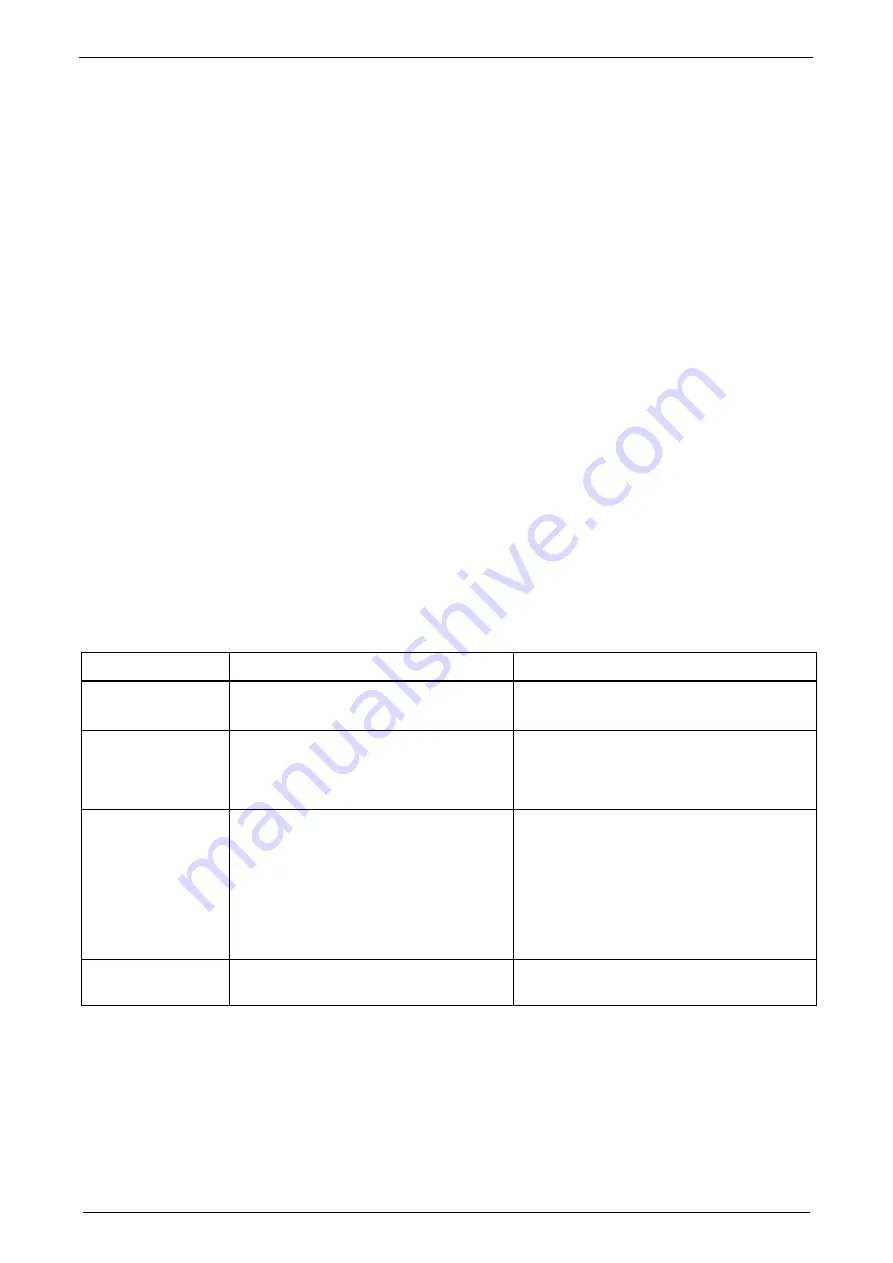
Parker EME
Compax3 device description
192-120100 N16 C3I10T10 - December 2010
77
3.10.1.2 Intended use
The Compax3 drive controller supports the "safe torque off" (STO) safety function,
with protection against unexpected startup according to the requirements of EN
ISO 13849-1, category 3 to PLe and EN 1037.
Together with the external safety control device, the "safe stop 1" (SS1) safety
function according to the requirements of EN ISO 13849-1 category 3 can be used.
As the function is however realized with the aid of an individually settable time
delay on the safety switching device, you must take into account that, due to an
error in the drive system during the active braking phase, the axis trundles to a stop
unguided or may even accelerate actively in the worst case until the expiry of the
preset switch-off time.
According to a risk evaluation which must be carried out according to the machine
standard 98/37/EG and 2006/42/EG or EN ISO 12100, EN ISO 13849-1 and EN
ISO 14121-1, the machine manufacturer must project the safety system for the
entire machine including all integrated components. This does also include the
electrical drives.
Qualified personnel
Projecting, installation and setup require a detailed understanding of this
description.
Standards and accident prevention regulation associated with the application must
be known and respected as well as risks, protective and emergency measures.
3.10.1.3 Advantages of using the "safe torque off" safety
function.
Safety category 3 in accordance with EN ISO 13849-1
Requirements
performance feature
Use of the safe torque off function
Conventional solution: Use of external switching
elements
Reduced switching
overhead
Simple wiring, certified application examples
Grouping of drive controllers on a mains contactor
is possible.
Two safety-oriented power contactors in series
connection are required.
Use in the production
process
High operating cycles,
high reliability, low wear
Extremely high operating cycles thanks to almost
wear-free technology (low-voltage relay and
electronic switch). The "safe torque off" status is
attained due to the use of wear-free electronic
switches (IGBTs).
This performance feature cannot be reached with
conventional technology.
Use in the production
process
High reaction speed, fast
restart
Drive controller remains performance- and control-
oriented in connected state.
No significant waiting times due to restart.
When using power contactors in the supply, a long
waiting time for the energy discharge of the DC link
circuit is required.
When using two power contactors on the motor side,
the reaction times may increase, you must however
take into consideration other disadvantages:
a) Securing that switching takes only place in
powerless state (Direct current! Constant electric arcs
must be prevented).
b) Increased overhead for EMC conform wiring.
Emergency-stop function According to the German version of the standard:
Permitted without control of mechanical power
switching elements 1)
Switch-off via mechanical switching elements is
required
1) According to the preface of the German version of the EN 60204-1/11.98,
electronic equipment for emergency-stop devices are also permitted, if they comply
with the safety categories as described in EN ISO 13849-1.