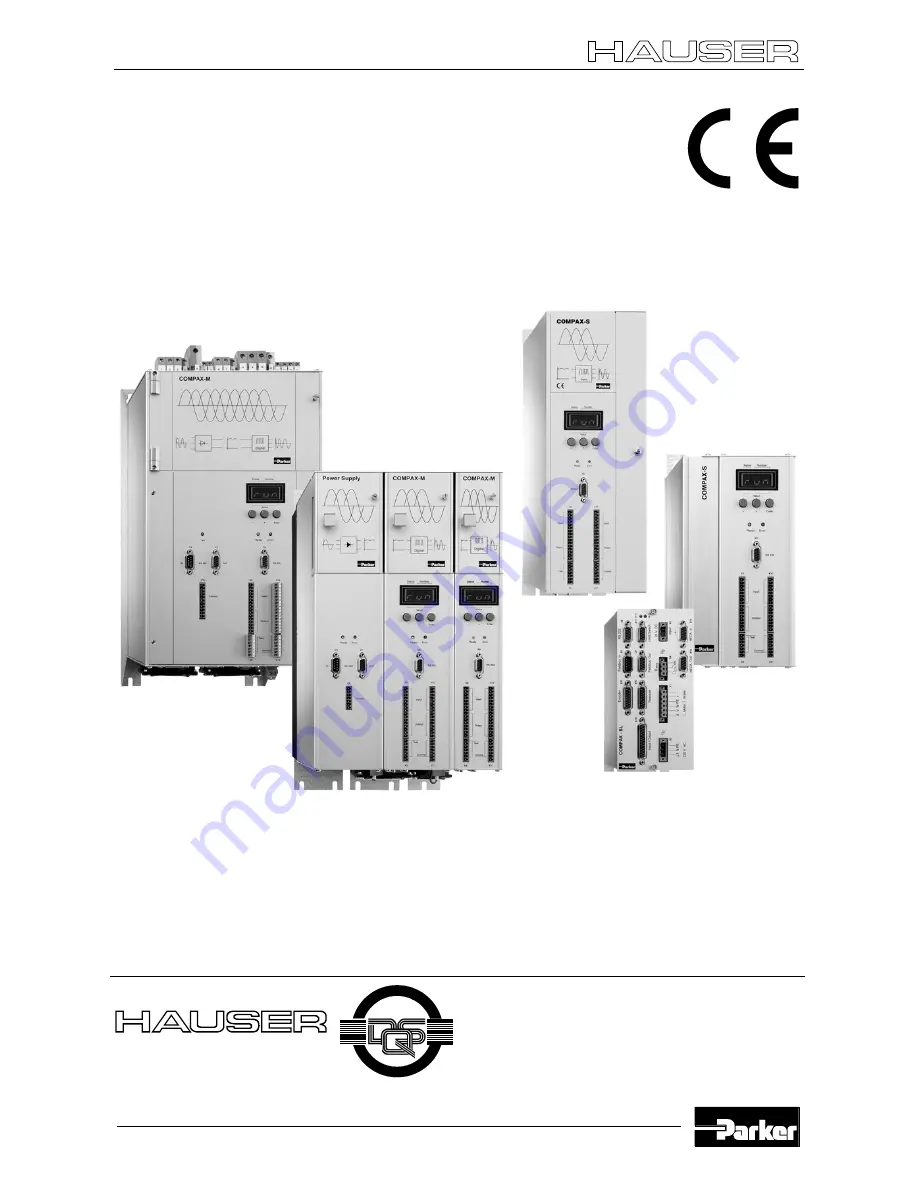
COMPAX-M /-S (L)
Subject to technical modification.
11.10.01 11:01
192-040053 N2
Data correspond to the state of technical development at the time of printing.
C O M P A X U s e r G u i d e
C o m p a c t S e r v o C o n t r o l l e r
W e a u t o m a t e m o t i o n
DIN EN ISO 9001
C
E R
T I F I E
D
Q
U
A
L I T
Y S Y S
T
E
M
Reg. Nr. 36 38
Parker Hannifin GmbH
EMD Hauser
P. O. Box: 77607-1720
Robert-Bosch-Str. 22
D-77656 Offenburg, Germany
Phone: +49 (0)781 509-0
Fax:
+49 (0)781 509-176
http://www.parker-emd.com
Parker Hannifin plc
Electromechanical Division
21 Balena Close
Poole, Dorset
BH17 7DX UK
Phone: +44 (0)1202 69 9000
Fax:
+44 (0)1202 69 5750
http://www.parker-emd.com
From software version V6.26
October 2001