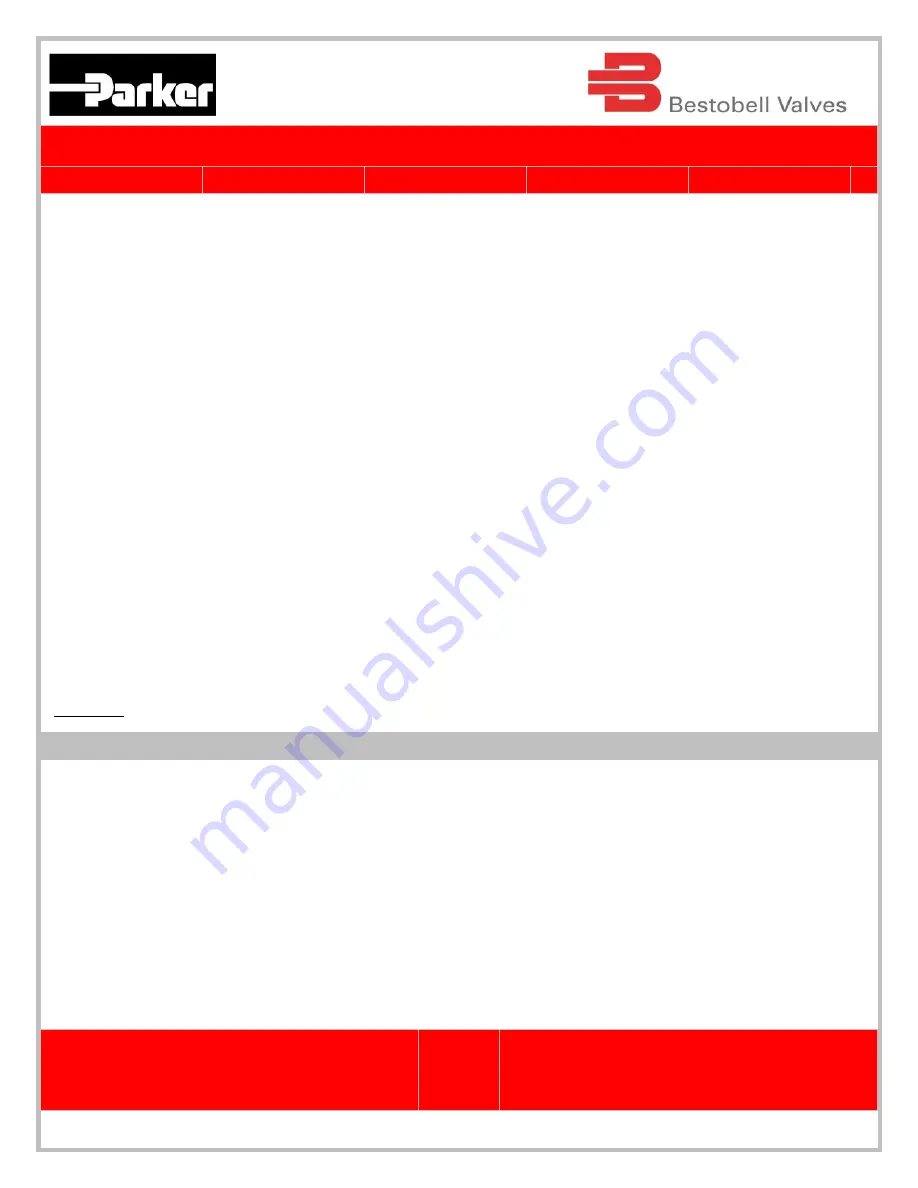
Date of Issue: 19 August 2021
Page 6 of 24
QF 80: Issue 2
Parker Hannifin
– Instrumentation Products Division Europe
President Park, President Way, Sheffield,
South Yorkshire, S4 7UR, United Kingdom
Tel: +44 (0) 114 224 0000 Web: www.parker.com/ipd
Globe / Needle Valve (DN10 (⅜”) – DN50 (2”)
Reference Number:
IOM 002
Date:
20 May 2014
Issue:
B
Valves must only be used in a circuit protected by suitable equipment.
The valve should be inspected for wear as part of a regular system maintenance programme.
Cryogenic burns can occur if the valve is handled during or after the valve has operated.
Minor leaks from the outlet side of the valve, if allowed to build up in a confined area, can be
hazardous. This can be avoided by dissipating into the atmosphere or a well ventilated area.
If valve is to be installed in hazardous climatic conditions or seismic areas, please inform Bestobell
Valves Ltd.
Identify the intended flow direction and match the valve orientation with its flow direction arrow.
Ensure that all end connections to the valve are in line and that the pipe work is supported to reduce
unwanted stresses, loading and vibration on the valve and system pipe work.
Ensure that all joining materials / components used during the installation of the valve are compatible,
and will not cause any deterioration to the valve structure.
When using on CO
2
, the internal atmosphere must be dry and moisture free as any bronze
components could be affected by carbonic acid.
DO NOT
check leaks with hands.
Cleanliness
Immediately after assembly in a controlled clean room, the valve is sealed in an airtight plastic bag to
maintain cleanliness. As such, it is essential to maintain this cleanliness throughout all stages of
installation. Particular care should be taken not to contaminate the internals of the valve with grease,
moisture, grinding dust, weld/brazing spatter etc.
Clean practi
ces will save time later with reduced ‘flushing’ and maintenance.