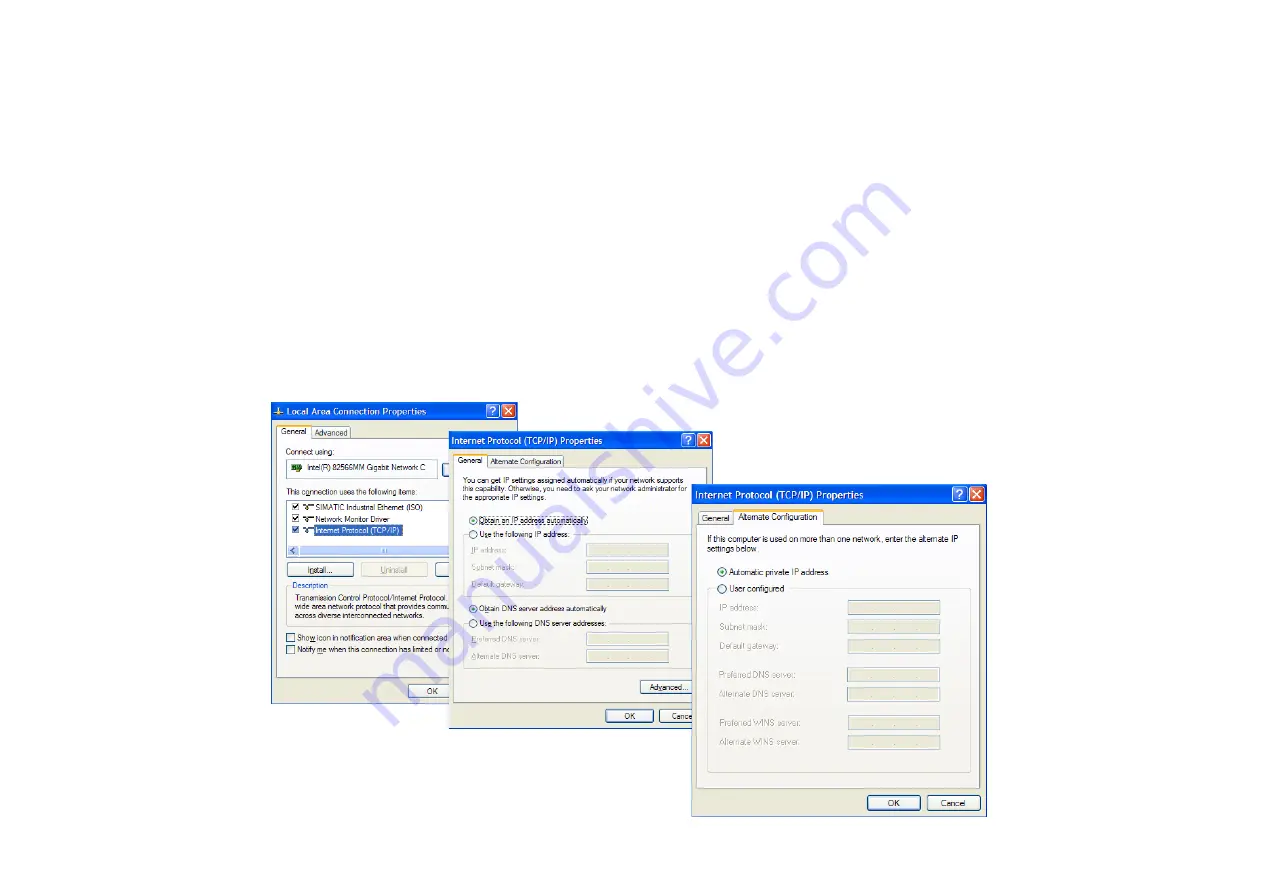
12-10
Ethernet
AC30V series Variable Speed Drive
CHANGING THE PC ETHERNET SETTINGS
Normally the PC Ethernet adapter is set to obtain an IP address automatically either from a DHCP server or using an automatic private IP
address (Auto-IP). The adapter settings may be checked / modified as follows:
For
Windows XP
under Control Panel
Network Connections
For
Windows 7
under Control Panel
Network And Sharing Center
Change adapter settings
Right-click on the required network adapter and choose Properties, then double-click on
Internet Protocol (TCP/IP)
(Windows XP) or
Internet
Protocol Version 4 (TCP/IPv4)
(Windows 7).
To use a fixed IP address make sure
Use the following Ip address
under the
General
tab is chosen and enter the required IP address, subnet
mask and default gateway.
To use DHCP or Auto-IP make sure
Obtain IP address automatically
under the
General
tab is selected and under the
Alternate
Configuration
tab that
Automatic private IP
address is selected.
Summary of Contents for AC30V Series
Page 34: ...Installation 4 16 AC30V series Variable Speed Drive Basic Speed Control Wiring...
Page 35: ...4 17 Installation AC30V series Variable Speed Drive APPLICATION 1 AUTO MANUAL CONTROL...
Page 36: ...Installation 4 18 AC30V series Variable Speed Drive Auto Manual Control Wiring...
Page 37: ...4 19 Installation AC30V series Variable Speed Drive APPLICATION 2 RAISE LOWER TRIM...
Page 38: ...Installation 4 20 AC30V series Variable Speed Drive Raise Lower Trim Wiring...
Page 39: ...4 21 Installation AC30V series Variable Speed Drive APPLICATION 3 PRESETS SPEEDS...
Page 40: ...Installation 4 22 AC30V series Variable Speed Drive Presets Speeds Wiring...
Page 41: ...4 23 Installation AC30V series Variable Speed Drive APPLICATION 4 PID CONTROL...
Page 42: ...Installation 4 24 AC30V series Variable Speed Drive PID Control Wiring...
Page 162: ...Sequencing Logic B 2 AC30V series Variable Speed Drive SEQUENCING DIAGRAM...
Page 325: ...E 2 E Plan Library AC30V series Variable Speed Drive Which then brings up the E Plan page...