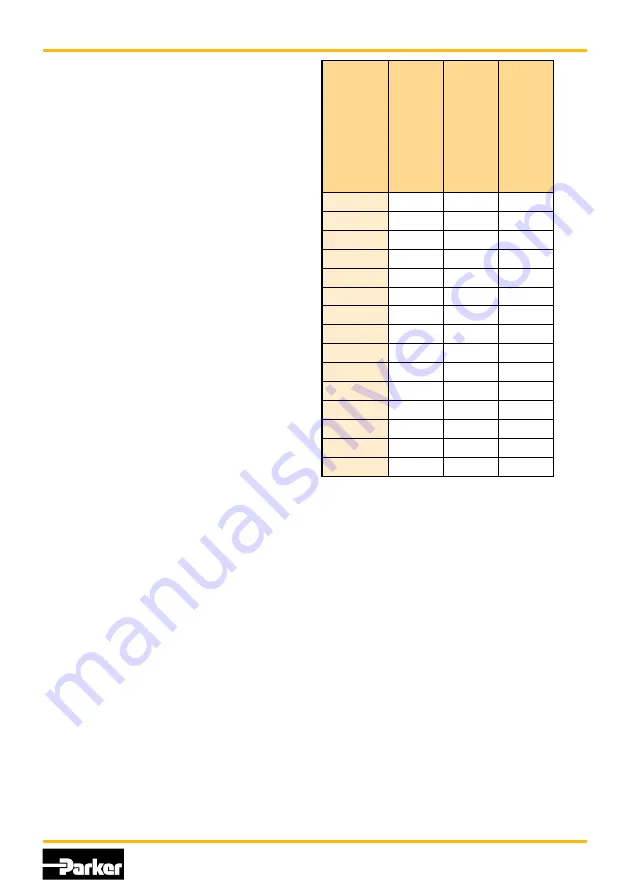
Bulletin MSG30-3245-INST/UK
Installation Manual
6
Parker Hannifin
Pump & Motor Division Europe
Chemnitz, Germany
Axial Piston Pump
Series PV, series 44 and higher
Start up
Check if all ports are properly connected according
to the specification, all connectors are tightened and
all adjustments are made.
Open suction valve (if installed)!
Switch system to free circulation or to lowest pres-
sure. Allow air bleeding for quick priming. Start pump
in tip mode operation until pump and all pipes are
filled and free from air bubbles. If pump does not build
up pressure, double check the installation.
Raise pressure setting only when all air is re-
moved. Let the pump work at reduced pressure for
5 - 10 min, check if all pipes and connections are
leak free and tight.
Observe reservoir: fluid level, built up of foam, fluid
temperature. When system is warmed up first func-
tional tests can be performed.
2. Displacement adjustment
All axial piston pumps of the PV series are equipped
with an adjustable displacement limiter.
The servo piston stroke is limited at full displace-
ment by a screw, guided in the end cover plug of the
servo piston bore. The screw is protected against
unintentional adjustment by a self-sealing lock nut
(see figure on page 4).
The factory setting of the displacement is according to
the nominal displacement of the pump. An adjustment
may only be made to a lower displacement (turning
screw in). An adjustment to a higher than the nominal
displacement can destroy the pump.
Adjustment should only be made with the pump
working at full displacement (not compensated) and
at a low output. At full displacement the piston area of
the servo piston is under case pressure. Opening the
self-sealing nut will only cause a negligible leakage
under these conditions.
Turning the adjustment screw clockwise will reduce
the pumps displacement. For the sizes PV016 –
PV092 the thread pitch is 1mm, for sizes PV140 –
PV360 the thread pitch is 1.5 mm. The table shows
the displacement change per mm resp. per turn and
the minimum adjustable displacement.
Note:
All pumps are adjusted and tested after as-
sembly in our factory. Only the compensator pressure
needs to be adjusted. That is done on the pilot valve
spindle. No other adjustments on the compensator
or the pump is required. Only after service or repair
a basic adjustment needs to be performed.
Size
Displacement chang
e per mm
(appr
ox.
cm³/U)
Displacement chang
e per turn
(appr
ox.
cm³/U)
Minim
um
adjustab
le
displacement (appr
ox.
cm³/U)
PV016
1.5
1.5
9
PV020
1.5
1.5
13
PV023
1.5
1.5
16
PV028
1.5
1.5
20
PV032
2.2
2.2
17
PV040
2.2
2.2
25
PV046
2.2
2.2
30
PV063
3.4
5.1
35
PV076
2.2
2.2
40
PV080
3.4
5.1
50
PV092
3.4
5.1
65
PV140
5.6
8.4
20
PV180
5.6
8.4
60
PV270
6.8
10.2
120
PV360
8.6
12.9
180
3. Standard pressure compensator,
code ...MMC
The adjustment of the compensating pressure is
performed for the standard pressure com pen sa tor
directly at the compensator.
To adjust the pressure, the lock nut (SW 13) is to be
loosened and the adjustment spindle is to be turned
(screw driver).
Turning clockwise will increase the compensating
pressure, turning counter-clockwise will decrease the
compensating pressure.
The compensating pressure can be adjusted in
a range from 15 to 350 bar (approx. 125 bar/turn).
By turning the pressure pilot cartridge housing
the compensator differential can be adjusted. It is
factory set to 15±1 bar and should not be changed
(approx. 20 bar/turn).
Different compensator differential settings can
cause instability or excessive power losses.
By using adapter kit PVCMCK** the standard
pressure compensator can be made remote control-
lable. This adapter replaces one of the side plugs.
Adapters are available for G1/4, M12x1.5 ISO 6149
and 7/16-20 UNF.
See also the remarlks in chapter 6.