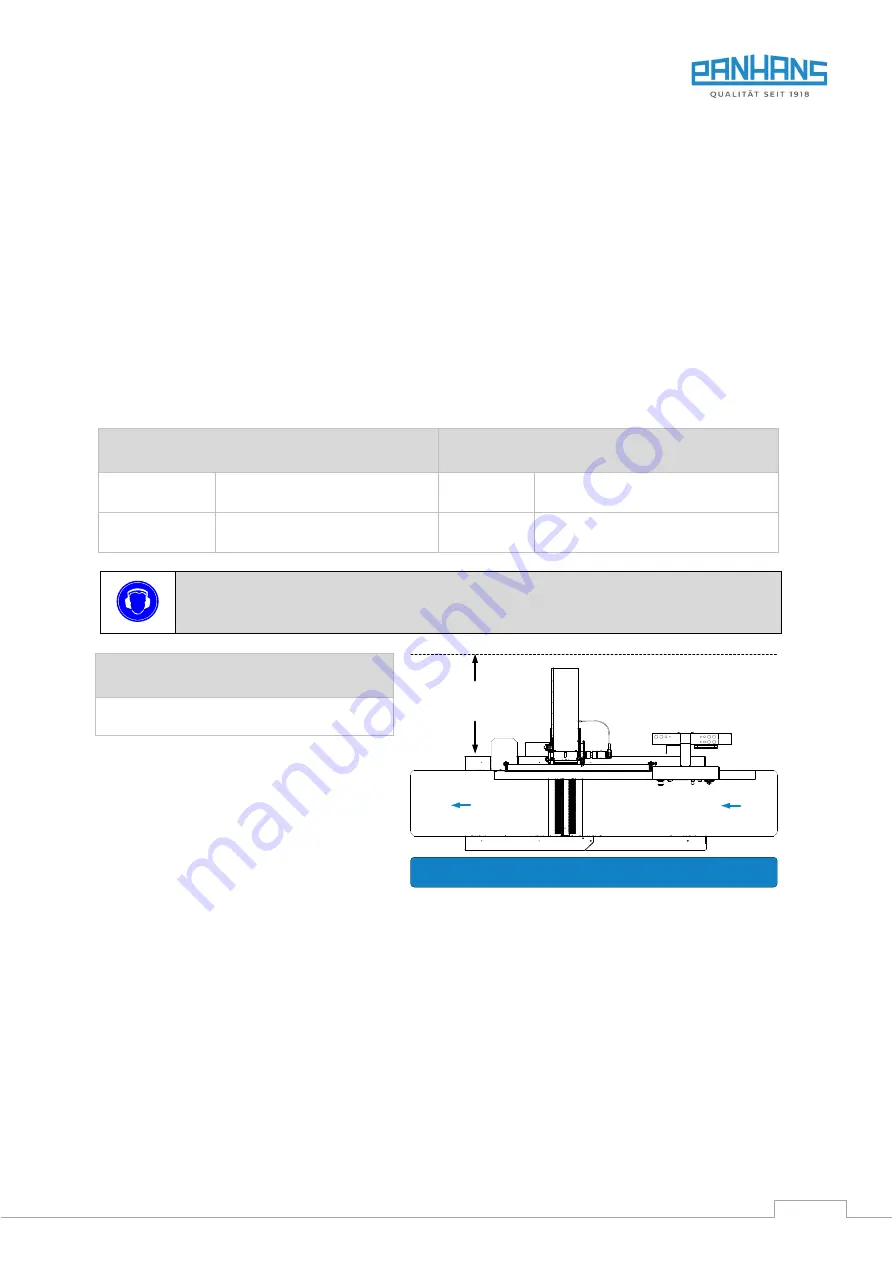
BA_PH_335-20_EN_07-22.docx
19
5.3
Emission Levels
5.3.1
Noise Information
The values given are emission levels and therefore do not necessarily represent safe workplace values. Alt-
hough there is a correlation between emission and immission levels, it cannot be reliably deduced whether
additional precautionary measures are necessary or not.
Factors that may affect the current immission level at the workplace include the duration of exposure, the
nature of the workspace, other noise sources, etc., e.g. the number of machines and other activities in the
vicinity. The permissible workplace values can also vary from country to country.
However, this information should enable the user to make a better assessment of hazard and risk.
5.3.2
Noise Emission Values
The specified measured values are determined in accordance with EN 860.
Uncertainty allowance K = 4 dB(A)
Workplace-related emission value
Sound power level
Idle
93 dB(A)
Idle
Lwa = 84 dB(A)
Working
99 dB(A)
Working
Lwa = 92 dB(A)
The workplace-related noise emission values of the machine exceed 85 dB(A)!
Therefore, suitable hearing protection must be provided to the personnel!
Dust emission values:
Determined according to GS-HO-05
Workplace-related dust emission value
(permissible 2.0 mg/m³ air)
0.48 mg/m³ air
Figure 4: Working area
Working Area
Wall distance
approx. 750 mm