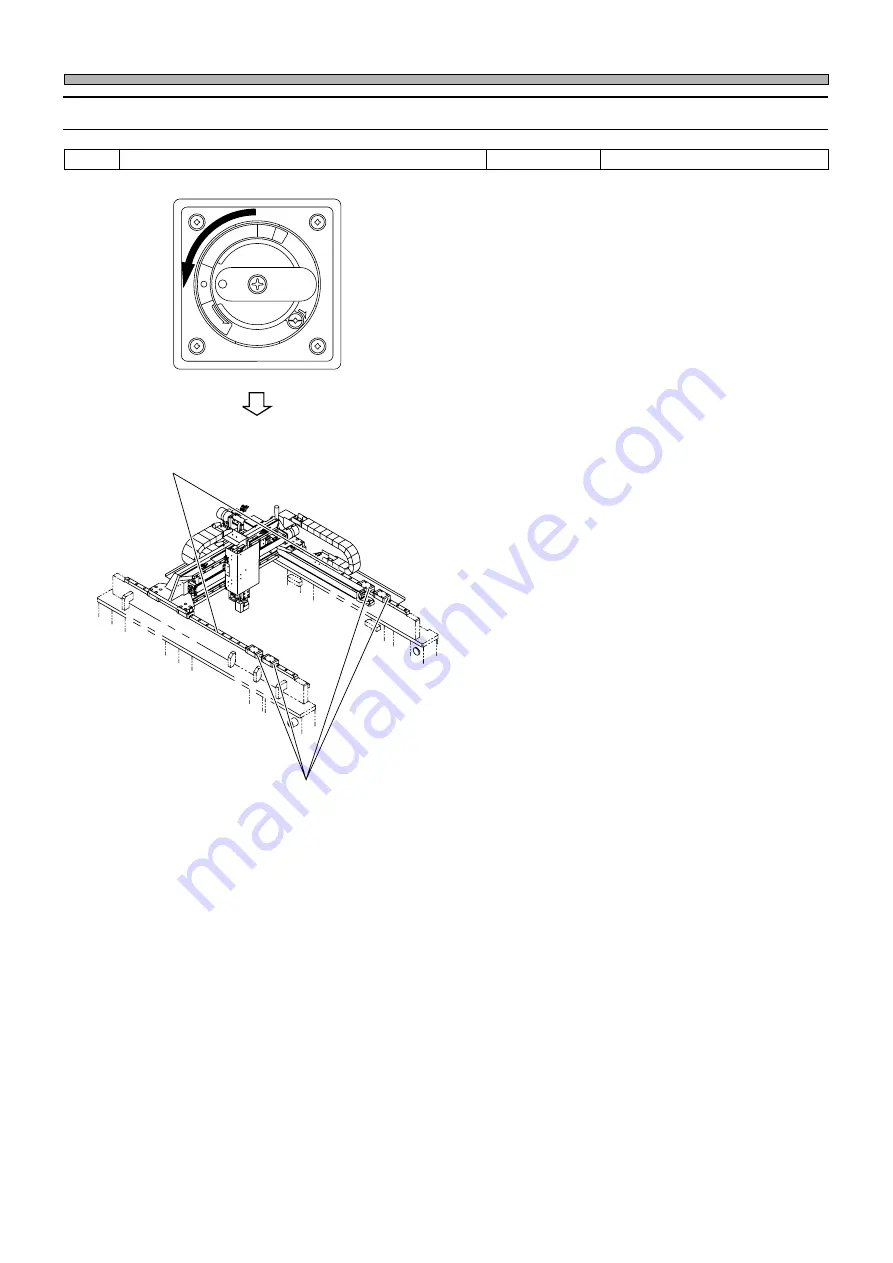
Page 1-58
Check Every 1500 Hours (Once Three Months)
1-7-4
Cleaning and Lubricating the Linear Bearing of Squeegee Axis
1.
Turn off the power.
2.
Open the front and rear safety covers.
3.
Clean and lubricate the linear bearing.
1.Linear bearing of squeegee axis
Lubricate the grease nipple.
Tools
Required time
5 to 10 minutes
1E4C-E-MMA01-A09-00
Linear way of recognition unit and squeegee head
Linear bearing of squeegee axis
REL
EA
SE
TR
IP
O
F
F
ON
RE
S
E
T
160HC1AA
Summary of Contents for KXF-1E4C
Page 2: ......
Page 6: ...4 1E4C E MMA00 B01 00 MEMO ...
Page 12: ...10 1E4C E MMA00 A02 01 MEMO ...