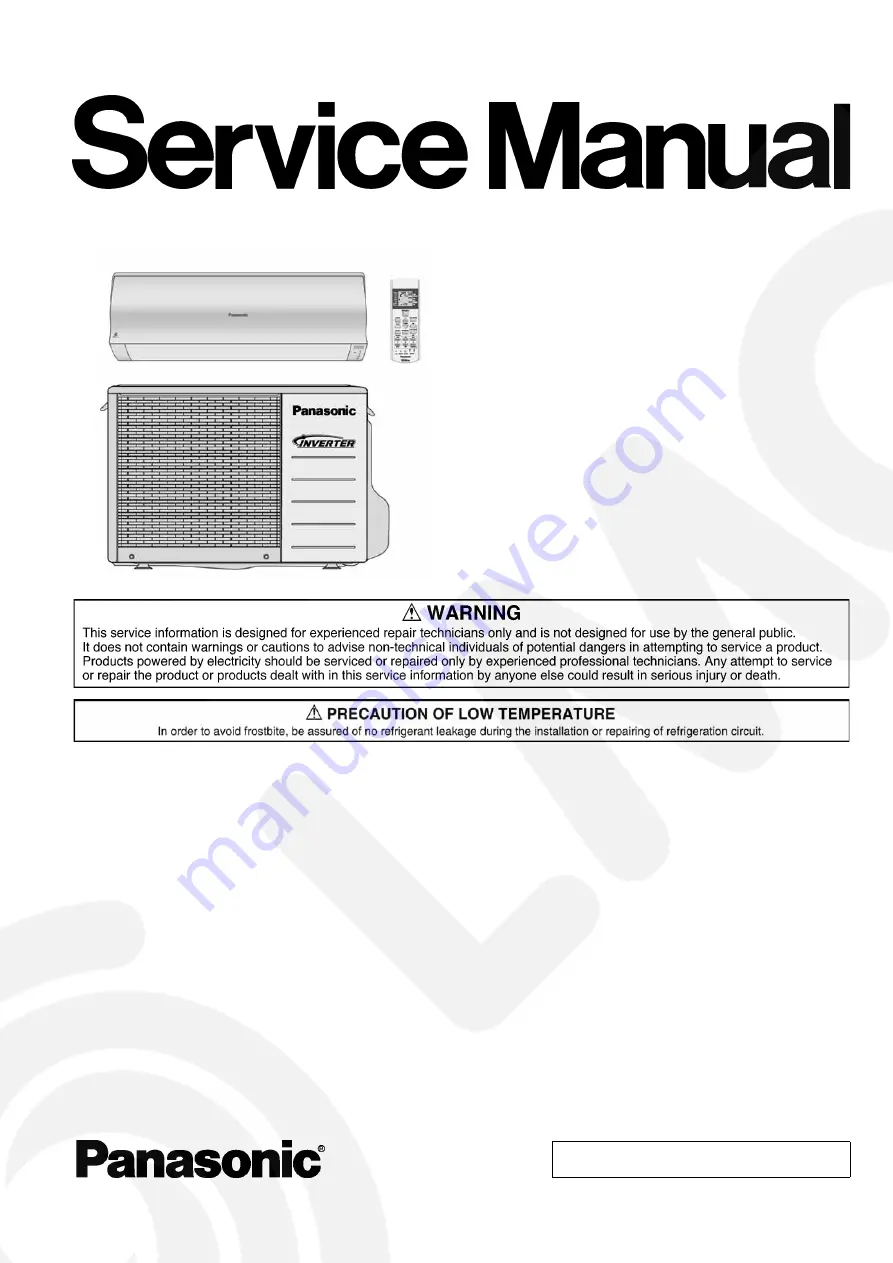
© Panasonic HA Air-Conditioning (M) Sdn. Bhd. 2009.
Unauthorized copying and distribution is a violation of law.
Order No. PHAAM0810076C2
Air Conditioner
CS-HE9JKE
CU-HE9JKE
CS-HE12JKE CU-HE12JKE
TABLE OF CONTENTS
PAGE
PAGE
1 Safety Precautions
-----------------------------------------------
3
2 Specifications
-----------------------------------------------------
5
3 Features
------------------------------------------------------------
11
4 Location of Controls and Components
------------------
12
4.1. Product Overview-----------------------------------------12
5 Dimensions
--------------------------------------------------------
13
5.1. Indoor Unit--------------------------------------------------13
5.2. Outdoor Unit -----------------------------------------------14
6 Refrigeration Cycle Diagram
--------------------------------
15
7 Block Diagram
----------------------------------------------------
16
8 Wiring Connection Diagram
--------------------------------
17
8.1. Indoor Unit--------------------------------------------------17
8.2. Outdoor Unit -----------------------------------------------18
9 Electronic Circuit Diagram
-----------------------------------
19
9.1. Indoor Unit--------------------------------------------------19
9.2. Outdoor Unit----------------------------------------------- 20
10 Printed Circuit Board
------------------------------------------
21
10.1. Indoor Unit ------------------------------------------------- 21
10.2. Outdoor Unit----------------------------------------------- 22
11 Installation Instruction
----------------------------------------
23
11.1. Select The Best Location ------------------------------ 23
11.2. Indoor/Outdoor Unit Installation Diagram ---------- 23
11.3. Indoor Unit ------------------------------------------------- 24
11.4. Outdoor Unit----------------------------------------------- 27
12 Operation and Control
----------------------------------------
30
12.1. Basic Function -------------------------------------------- 30
12.2. Indoor Fan Motor Operation--------------------------- 31
12.3. Outdoor Fan Motor Operation ------------------------ 32
12.4. Airflow Direction Control-------------------------------- 33
Summary of Contents for CS-HE9JKE
Page 13: ...13 5 Dimensions 5 1 Indoor Unit...
Page 14: ...14 5 2 Outdoor Unit...
Page 15: ...15 6 Refrigeration Cycle Diagram...
Page 16: ...16 7 Block Diagram...
Page 17: ...17 8 Wiring Connection Diagram 8 1 Indoor Unit...
Page 18: ...18 8 2 Outdoor Unit...
Page 19: ...19 9 Electronic Circuit Diagram 9 1 Indoor Unit...
Page 20: ...20 9 2 Outdoor Unit...
Page 22: ...22 10 2 Outdoor Unit 10 2 1 Main Printed Circuit Board...
Page 25: ...25 3 For the embedded piping This can be used for left rear piping and left bottom piping also...
Page 85: ...85 17 Technical Data 17 1 Operation Characteristics 17 1 1 CS HE9JKE CU HE9JKE...
Page 86: ...86...
Page 87: ...87...
Page 88: ...88...
Page 89: ...89 17 1 2 CS HE12JKE CU HE12JKE...
Page 90: ...90...
Page 91: ...91...
Page 92: ...92...