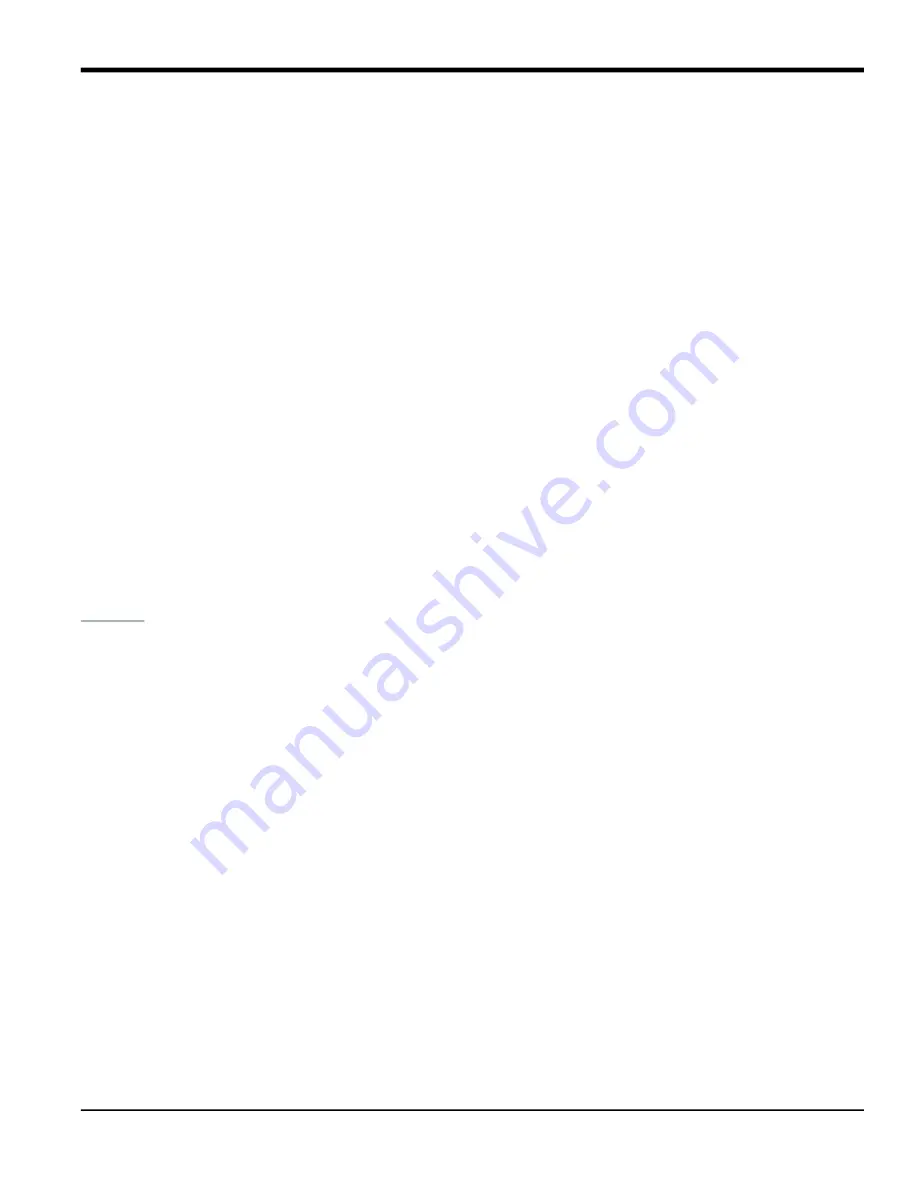
DigitalFlow™ XMT868i Programming Manual
39
Appendix C. Programming the XMT868i Using PanaView™
5. At the
Temp Input Return
prompt, double-click on
Fixed
to enter a constant temperature value or on
Slot1
to
select the output in Slot 1 that will provide the live temperature input for the return.
Note:
If Slot 1 contains an activated option card with an analog input assigned to
TEMP
or an
RTD
input, Slot 1
appears as an option at the above prompt. If the process temperature is stable, a fixed value may be used,
but most applications require a live temperature input.
6. One of the following two prompts will appear, depending on your selection in Step 3.
•
If
Fixed
was chosen, enter the known fixed process temperature and click
[Next Item]
.
The meter will only
accept values from –328° to 1832°F (–200
o
to 1000
o
C).
•
If
Slot 1
was chosen, double-click on the desired temperature input (from A to D).
The program now returns to the Channel menu.
C.5.5 Entering Setup Parameters
The signal limits and response times for the Model XMT868i are specified using the Set Up submenu. While following
the programming instructions, refer to Figure 55 on page 73. This submenu includes four options:
•
Signal - set the parameters related to the transducer signal
•
V Averaging - specify the response of the meter to step changes
•
Default Setup - initialize all parameters to default values
•
Advanced Features - enable mass flow, edit kinematic viscosity vs. sound speed table, activate K factors, and
select transmit code length.
To enter the Set Up submenu, highlight and double-click on the Set Up option in the center pane of the Channel
menu. Remember to record all programmed data in Appendix B,
Data Records
.
C.5.5.1 The Signal Option
Use this option to set the limits for the incoming signal and other parameters affecting the transducer signal. For
example, the programmed signal strength low limit may be used to determine the trigger point for an alarm.
CAUTION!
The Signal default settings are suitable for most applications. Consult the factory before changing
any of these parameters.
1.
From the Set Up option menu, highlight and double-click on
Signal
in the center pane.
2. Click
[Next Item] to accept the current Signal Low Limit value or enter a new value and click
[Next Item].
The default value for the above parameter is 20, and values from –20 to 100 are acceptable. The E1: LOW SIGNAL error
message appears when the signal strength falls below the programmed Signal Low Limit
value. See Chapter 2,
Error
Codes
, in the
Service Manual
for a discussion of error codes.
3. Click
[Next Item]
to accept the current Corr. Peak Limit value or enter a new value and click
[Next Item].
The default value for the above parameter is 100, and values from 0 to 500 are acceptable. The E4: SIGNAL QUALITY
error message appears when the signal quality falls below the programmed Cor. Peak Limit
value. See Chapter 2,
Error Codes
, in the
Service Manual
for a discussion of error codes.
4. Click
[Next Item]
to accept the current Soun– Limit value or enter a new value and click [Next Item]
.
The default value for the above parameter is 20%, and values from 1% to 50% are acceptable. The E2: SOUNDSPEED
error message appears when the calculated fluid soundspeed differs from the fluid soundspeed entered in the
CHx-SYSTM menu by more than the programmed Soun– Limit value. See Chapter 2,
Error Codes
, in the
Service Manual
for a discussion of error codes.
5. Click
[Next Item] to accept the current Velocity Low Limit value or enter a new value and click
[Next Item
].
The default value for the above parameter is –150.0 ft/sec. (–46 m/sec) and values from –500 to 500 ft/sec (–150 to
150 m/sec) are acceptable. The E3: VELOCITY RANGE error message appears when the calculated fluid velocity is less
than the programmed Velocity Low Limit value. See Chapter 2,
Error Codes
, in the
Service Manual
for a discussion of
error codes.
6. Click
[Next Item]
to accept the current Velocity High Limit value or enter a new value and click
[Next Item]
.
The default value for the above parameter is 150.0 ft/sec (46 m/sec) and –500 to 500 ft/sec (–150 to 150 m/sec) are
acceptable values. The E3: VELOCITY RANGE error message appears when the calculated fluid velocity exceeds the
Summary of Contents for DigitalFlow XMT868i
Page 2: ......
Page 4: ...ii no content intended for this page...
Page 50: ...Chapter 1 Programming Site Data 42 DigitalFlow XMT868i Programming Manual...
Page 74: ...Chapter 4 Printing Data 2 DigitalFlow XMT868i Programming Manual...
Page 78: ...Chapter 5 Clearing Data 4 DigitalFlow XMT868i Programming Manual...
Page 79: ...DigitalFlow XMT868i Programming Manual 5 Appendix A Menu Maps Appendix A Menu Maps...
Page 80: ...Appendix A Menu Maps 6 DigitalFlow XMT868i Programming Manual...
Page 86: ...Appendix A Menu Maps DigitalFlow XMT868i Programming Manual...
Page 144: ...Appendix D PanaView Menu Maps for the XMT868i 70 DigitalFlow XMT868i Programming Manual...
Page 150: ...Appendix A PanaView Menu Maps DigitalFlow XMT868i Programming Manual 76...
Page 162: ...Warranty 6 AquaTrans AT868 User s Manual no content intended for this page...
Page 163: ......