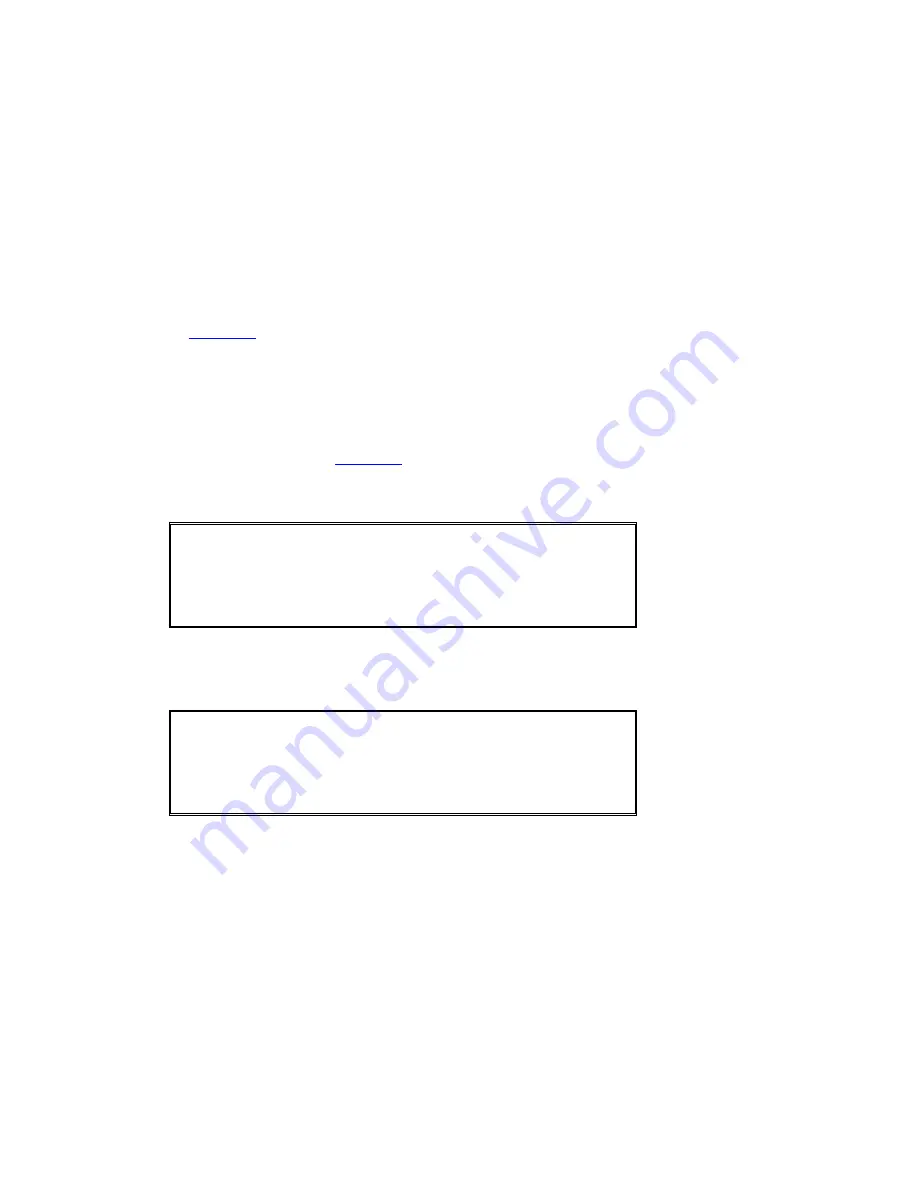
SECTION 8
CALIBRATION
100
8.2.2 PROGRAMMABLE CURRENT LIMIT CALIBRATION
1.
Connect the high current load to the output of the power source.
2.
Connect an Ammeter to the load wiring (Shunt type preferred).
3.
Program the UPC Voltage to drive a load at 60% of rated output current of the power source at 60
Hz.
4.
Set the Programmable Current limit parameter of the UPC steady-state program to 50% of rated
output current of the power source.
5.
Apply output power to the load. Adjust R24 of the DRM PCB until the RMS current measured with
the ammeter probe equals that of the programmed current limit value (in RMS amps). Refer to
(
) for control locations.
8.2.3 OUTPUT VOLTMETER CALIBRATION
The second step in the MANUAL calibration process is to calibrate the Output Voltmeter. Only one meter
circuit is used for all voltage, current and power measurements. If other metering functions are out of
specification after calibrating the Phase A voltmeter, return the unit for repair. The Output Voltmeter is
calibrated as follows: Refer to (
) for control locations.
1.
Remove top cover of the chassis.
2.
Turn on the system. Load and Execute a program with the following parameters:
PROGRAM: #1 FORM=3 COUPLING=DIRECT
FREQ=60 Va=125.0 Vb=125.0 Vc=125.0
WFa=1 WFb=1 WFc=1
#SEGS=0 Ilim=50 PHb=120° PHc=240°
3.
Calibrate the Metering Circuit by measuring the Power Source output voltage, Phase A to Neutral, at
the output terminal block with the 4½ digit DVM. Adjust R64 of the Metering PCB until the Va
display on the front reads the same as the output voltage.
V/I METER: ENTRY: 125.0
FREQ=60.00 Va=125.0 Vb=125.0 Vc=125.0
SENSE=INT Vab=208.0 Vbc=208.0 Vca=208.0
MANUAL MODE Ia=00.0 Ib=00.0 Ic=00.0
5.
Turn off the system.
6.
Replace top cover of the chassis.
8.3
EXTERNALLY REFERENCED CALIBRATION
The UPC metering is designed to be easily calibrated in the field. Calibration may be required in order to
ensure that the CSC function is able to precisely match the output voltage of the power source to the
programmed command voltage. Potential sources of error which may cause difference between these two
voltages are:
a)
Drift in oscillator signal level.
b)
Power Amplifier gain drift.
c)
Output transformer turns ratio error. i.e. Actual turns ratio different from encoded turns ratio.
d)
Difference between INT SENSE metering circuit and EXT SENSE metering circuit.
e)
Internal metering inaccuracy.