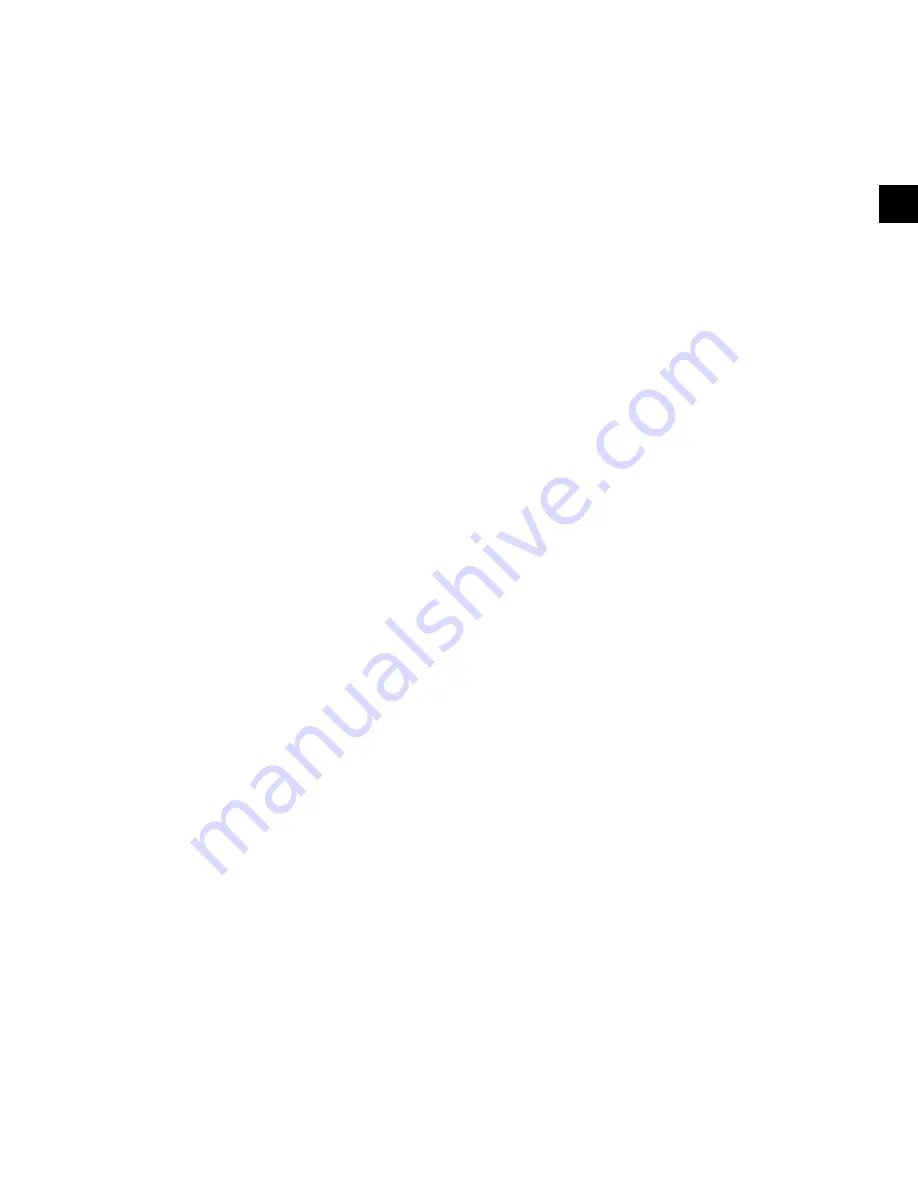
Form PA102.20-N1
91
Installation & Assembly Manual │
PACE
SECTION 3 - HANDLING, STORAGE, AND INSTALLATION
Issue Date: 07/03/2018
3
WATER TREATMENT
Any copper tube coils may be attacked by acid con-
densate. Treat the coils with boiling water and CO
2
to
remove the condensate, and to assure longer tube life.
Freeze Protection
Chilled water, hot water, and steam coils can be dam-
aged during freezing weather. Take the following pre-
cautionary measures to prevent freezing:
• Positive coil freeze protection must be used in
installations where any part of the water coil is
subjected to temperatures of 32°F or lower, which
may be accomplished by using a suitable anti-
freeze solution. If the coil is not in use, it is recom-
mended to drain the coil completely, and blow dry
the inside of the tubes with compressed air.
• After draining, flush the coils with an anti-freeze
solution such as 50% glycol and 50% water, which
will protect from the coil from freezing to approxi-
mately -35°F
at sea level. Refer to ASHRAE and
ARI guidelines for more information.
• During winter when shutdowns such as power
failure, night and weekend shutdowns may occur,
install the controls so the return air dampers go to
the fully open position, and all fresh air dampers
go to the fully closed position. A source of auxiliary
heat must be maintained inside the AHU cabinet.
• Other protection can include electromechanical
switches and constantly flowing water; however,
PACE will not be responsible for any coils dam-
aged by freezing.
Steam Coils
The operation of steam coils is dependent on airflow
quantity and temperature as shown in
. Consult the job submittal form for the infor-
mation specific to this AHU.
Steam Distributing Coils
Use the following instructions to clean the steam dis-
tributing coils:
• Do not bush or reduce the coil return pipe size.
• Use a full size return pipe to the bottom of a dirt
pocket. The supply pipe may be reduced at the
coil connection, if necessary.
• Install the coil casing level with the return down. A
coil must be sufficiently elevated to allow a 12 in.
minimum drop between the return connection on
the coil and the trap. More than a two inch drop
is required to protect the coil from freezing. The
return main should be located below the trap.
Steam Control
Continuous steam supply ensures long coil life and
minimizes potential trapping, venting and freezing
problems. A rapid cycling of the modulating steam sup-
ply or a frequent on-off steam supply control results in
repeated thermal and piping stresses which will short-
en the coil life. Modulating steam control valves must
not be oversized, and must be carefully selected. A
substantial variation in the supply pressure will require
installing a pressure-reducing valve ahead of the auto-
matic control valve.
Light load operation with a modulated steam supply
can be improved by the installation of a vacuum break-
er check valve. An open relief line to the atmosphere
from the return line near the coil is desirable, except on
vacuum systems.
With a modulated steam supply, it is not practical to lift
the condensate to an overhead return. Locate the coil
well above the return, or provide condensate unit, or a
boiler return trap below the coil.
Individual control valves are required on each coil in-
stalled in series with respect to airflow. When a modu-
lating steam valve supplies two or more coils in paral-
lel, with respect to airflow, the piping must be designed
to provide uniform steam distribution to each coil.
Steam Traps
Use the following information to select the correct
steam trap.
• Float and Thermostatic (F and T) traps are recom-
mended for all low or medium pressure applications.
• Use thermostatic traps only for air venting, for out-
door applications where a F and T trap might be
subject to freezing.
• Use bucket traps only for a non-modulated steam
supply.
• Size the steam traps in accordance with the man-
ufacturer's recommendations (usually several
times the steady state steam flow).
• Use the actual operating conditions (coil pressure
vs. return pressure) to select a trap.
• It is preferable to provide an individual trap for
each coil, but a single trap may be used for coils
operating in parallel with respect to the airflow.
Coils in series with respect to airflow must be sup-
plied with individual traps.
• Locate the trap at least 12 in. below the coil return
connection, and lower it when freeze protection is
required. Do not attempt to lift condensate modu-
lated steam supply.