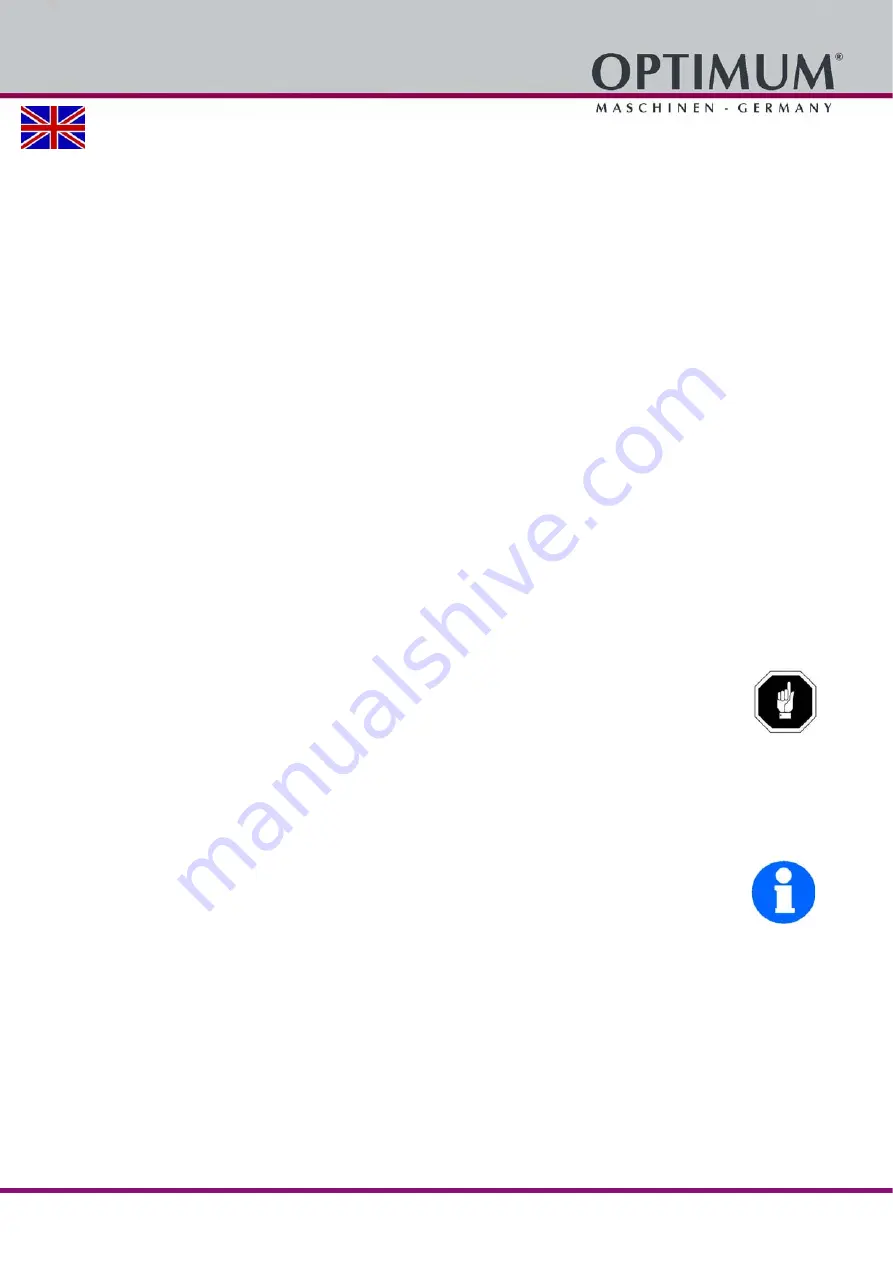
Operation
Version 1.0 - 2020-12-10
37
Translation of original operating instruction
GT22
EN
GT22_G
B_4
.f
m
Bonding:
The function of the bond is to keep the grinding wheel in shape for a long time. The bonding
agent on the grinding wheels keeps the abrasive grains at a certain distance from each other.
Make sure that the grinding wheel is stable for the grinding process.
Binding types
- The glass bond, combines hardness and structure. Very good for precision grinding, for
fast material removal.
- The plastic bond (resin and synthetic resin) is favourable for high-speed rotation and has
a certain elasticity. For heavy duty use, ideal for rough grinding.
- The ceramic bond: for the machining of difficult to machine materials such as PCD or
CBN.
- The rubber bond has elasticity and is favourable for narrow grinding wheels.
- The metal bond is particularly favourable for producing a grinding wheel whose abrasives
are very hard.
Pores:
The pores between the abrasive grains and the bond act as cooling lubricant chambers, which
also promote the removal of chips during grinding. If the pores are too small, e.g. on inferior
grinding wheels, additional friction and a higher temperature will occur. This can lead to dam-
age to the abrasive. By contrast, larger pore spaces allow more coolant to be carried along.
This reduces the risk of grinding fire.
4.12
Dressing the grinding wheel
To keep the grinding wheel sharp, it must be regularly dressed. There is a dressing device on
the grinding head.
The scope of delivery also includes a dressing device which can optionally be attached to the
grinding table in the T-slot for dressing the grinding wheel.
ATTENTION!
The dressing pin can break easily.
When dressing, the diamond tool should be guided from the centre of the wheel to the outside.
If the tool is guided in the opposite direction (from outside to inside) there is a risk that the grind-
ing wheel or the diamond pin will break.
Ensure that the dressing tool is securely fastened and that the dressing process is vibration-
free and free from shocks. This is very important for a good surface quality of the grinding
wheel!
INFORMATION
When the diamond pin is worn out, the diamond pin can be turned by 180°.
Coolant should be added when dressing the grinding wheel. This makes dressing faster and
more efficient. The suitable coolant extracts heat and thus increases the service life of the dia-
mond pin. The coolant must always be kept clean!
4.13
Digital Readout
The grinding machine is equipped with the two axis display DPA31.
The additional function that is possible with the DPA31 when operating on milling machines is
not possible on grinding machines.