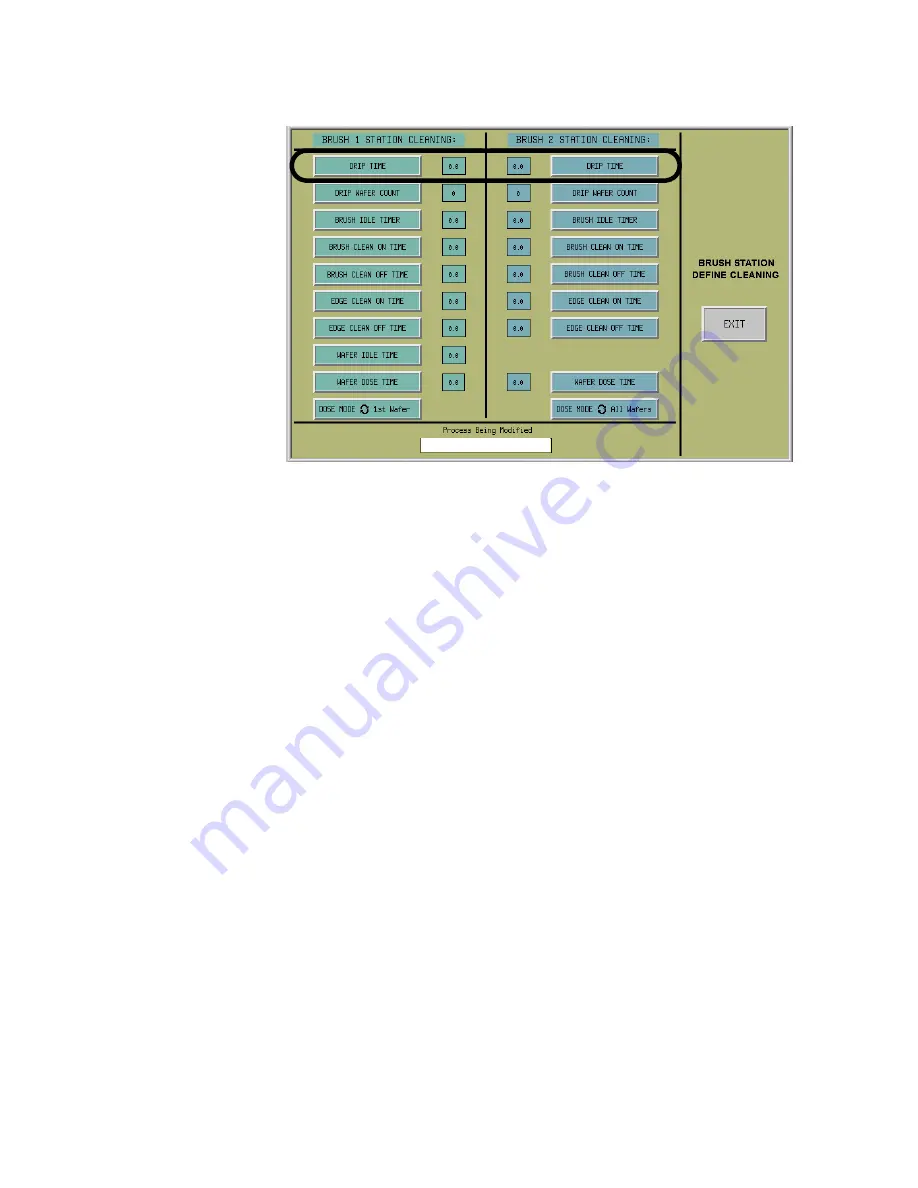
C h a p t e r 9 P R O C E S S R E C I P E
7/26/00
INTEGRA Operations Revision A
9-31
20-0200-231 (CR), 20-0200-232 (Std), 20-0200-251 (CD)
A
NOTE:
If the Brush Station
is set up to process chemical,
then chemical will be
dispensed to the brush, even if the DRIP CHEM button (operational during the
coinciding
EVENT
) is toggled to the
OFF
position.
Change DRIP WAFER COUNT
6 Touch
DRIP WAFER COUNT for Brush Station #1 Cleaning to
display the
NUMBER PAD
and set the number of wafers between
brush cleaning cycles. This option is only used when DI water,
(not chemical) is used to process each wafer. Periodically (based
on wafer count) NH
4
OH is introduced to clean the brushes.
7 Enter the desired count on the
NUMBER PAD
(not shown), and
touch ENTER.
Use the DRIP WAFER COUNT button to set the number of wafers
that can pass through the Brush Station without interruption. When
the number is reached, processing is halted, no incoming wafers are
allowed into the Brush Station(s), and the brushes are cleaned.
If Brush Station #2 is processing with NH
4
OH, then the process is
identical to Brush Station #1 processing with NH
4
OH.
8 Touch
DRIP WAFER COUNT for Brush Station #2 Cleaning to
display the
NUMBER PAD
to set the number of wafers between
brush cleaning cycles.
9 Enter the desired count on the
NUMBER PAD
(not shown), and
touch ENTER.
STANDARD
Summary of Contents for Synergy Integra
Page 8: ......
Page 24: ...1 4 INTEGRA Operations Revision A 7 26 00 20 0200 231 CR 20 0200 232 Std 20 0200 251 CD...
Page 38: ...2 14 INTEGRA Operations Revision A 7 26 00 20 0200 231 CR 20 0200 232 Std 20 0200 251 CD...
Page 222: ...9 62 INTEGRA Operations Revision A 7 26 00 20 0200 231 CR 20 0200 232 Std 20 0200 251 CD...
Page 314: ...10 76 INTEGRA Operations Revision A 7 26 00 20 0200 231 CR 20 0200 232 Std 20 0200 251 CD...