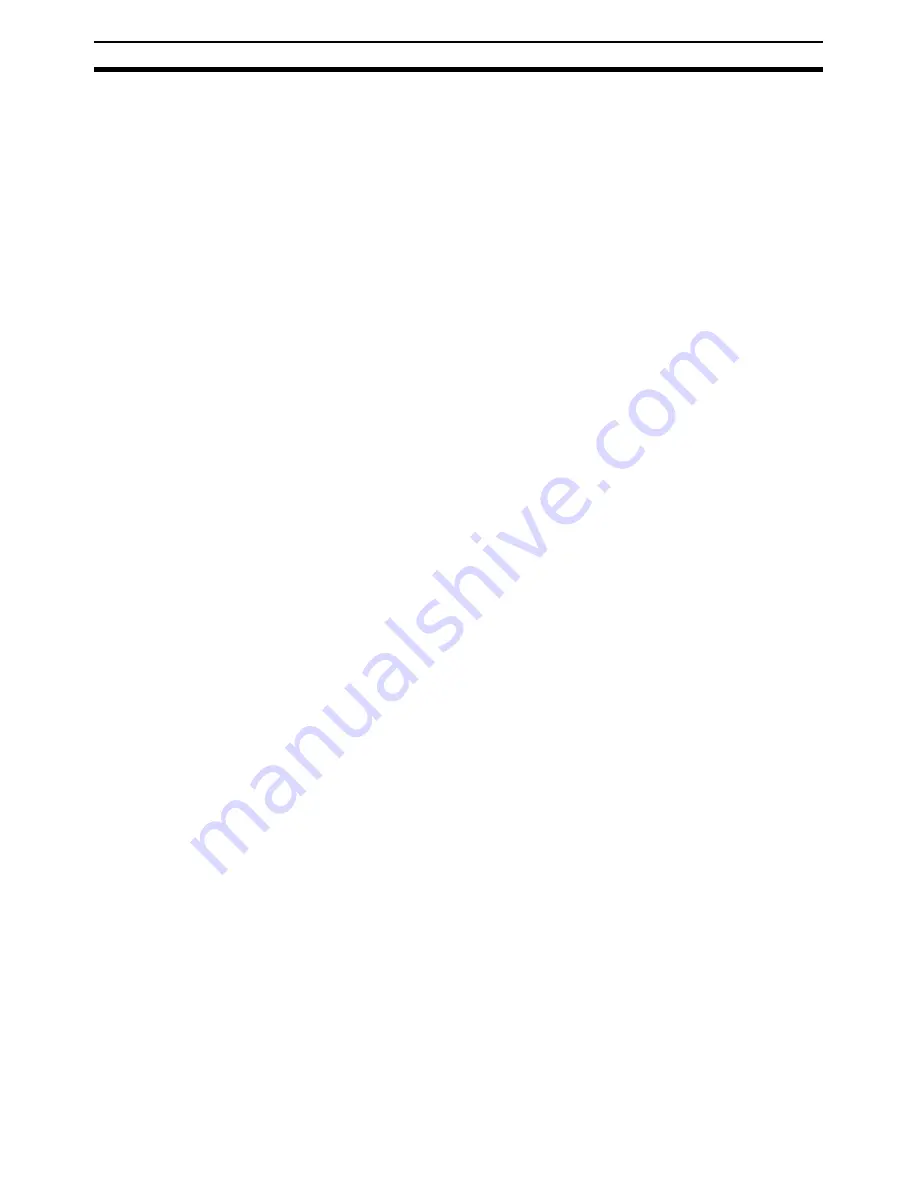
68
PROFIBUS-DP Master DTM
Section 3-3
Note
1.
If the selected PLC memory area, on to which the data must be mapped is
not supported by the PLC CPU, a warning message will be displayed upon
downloading the configuration.
2.
If an invalid setting is made the calculated length value will change its color
to red, indicating an invalid setting. In addition, a warning message will be
displayed, upon saving the changes. Invalid settings are for example
• The start address and length definitions of the data block will cause it
to exceed the area in the PLC.
• The data mapping of two or more I/O Areas (Output and/or Input) will
be overlapping each other partly or totally in the PLC Memory.
3.
The Compress button will be disabled, i.e. grayed out, when Auto-Ad-
dressing (see
) has been enabled.
Changing Mapped Data
Allocations
By default, the data are mapped to Area 1 in both the Output and Input Alloca-
tion tabs. It is however possible to map a part of the data to the second area in
the same tab. For example, an application may require to store all byte data in
one location and all word data in another.
Moving data mapped in one Area to another Area is done from the collective
list. The procedure is as follows.
1,2,3...
1.
Find the module which must be mapped to a desired Area in the collective
list, and select it.
2.
Left-click the module and drag it, while holding the Left mouse button, to
the desired Area. This can be the end of the list or any empty space in the
list in which it will fit (see Note).
3.
Release the mouse button. The module data is copied in the desired Area
and appended to the already existing list. The same entry in the other list
is now deleted.
4.
Finally, the PLC Memory Address to which the module is mapped is now
updated in the collective list.
Note
1.
If Auto-Addressing is enabled (see
Master Setup tab
in this section), any
empty spaces evolving out of moving of modules to another Area will be
removed by compressing the list. Modules located to a higher address will
be moved to a lower address to fill up the gap.
2.
If Auto-Addressing is disabled, compressing the list can be accomplished
by pressing the Compress button, after all modifications to the mapping
have been made.
3-3-2
Diagnostics User Interface
Diagnostics User Interface
The PROFIBUS-DP Master DTM provides a second User Interface, to display
the Diagnostics information available in the PROFIBUS-DP Master Unit. This
information concerns
• Unit and PROFIBUS-DP Interface status flags.
• Slave status flags and common slave diagnostics.
• The Unit’s Error Log.
Furthermore, the Diagnostics User Interface allows changing the Master’s
PROFIBUS operational mode and the transmission of Global_Control mes-
sages.
Summary of Contents for SYSMAC CJ1W-PRM21
Page 2: ...iv...
Page 36: ...22 Basic Operating Procedure Section 1 5...
Page 52: ...38 Defining PROFIBUS DP in the Software Section 2 5...
Page 112: ...98 Allocated CIO Area Words Section 4 2...
Page 122: ...108 Command Response Reference Section 5 2...
Page 160: ...146 Replacing the Unit Section 7 8...
Page 174: ...160 Appendix...
Page 180: ...166 I O Data Conversions Appendix D...
Page 186: ...172 Configurator Error and Warning Messages Appendix E...
Page 187: ...173 Index...
Page 188: ...174 Index...
Page 190: ...176 Revision History...