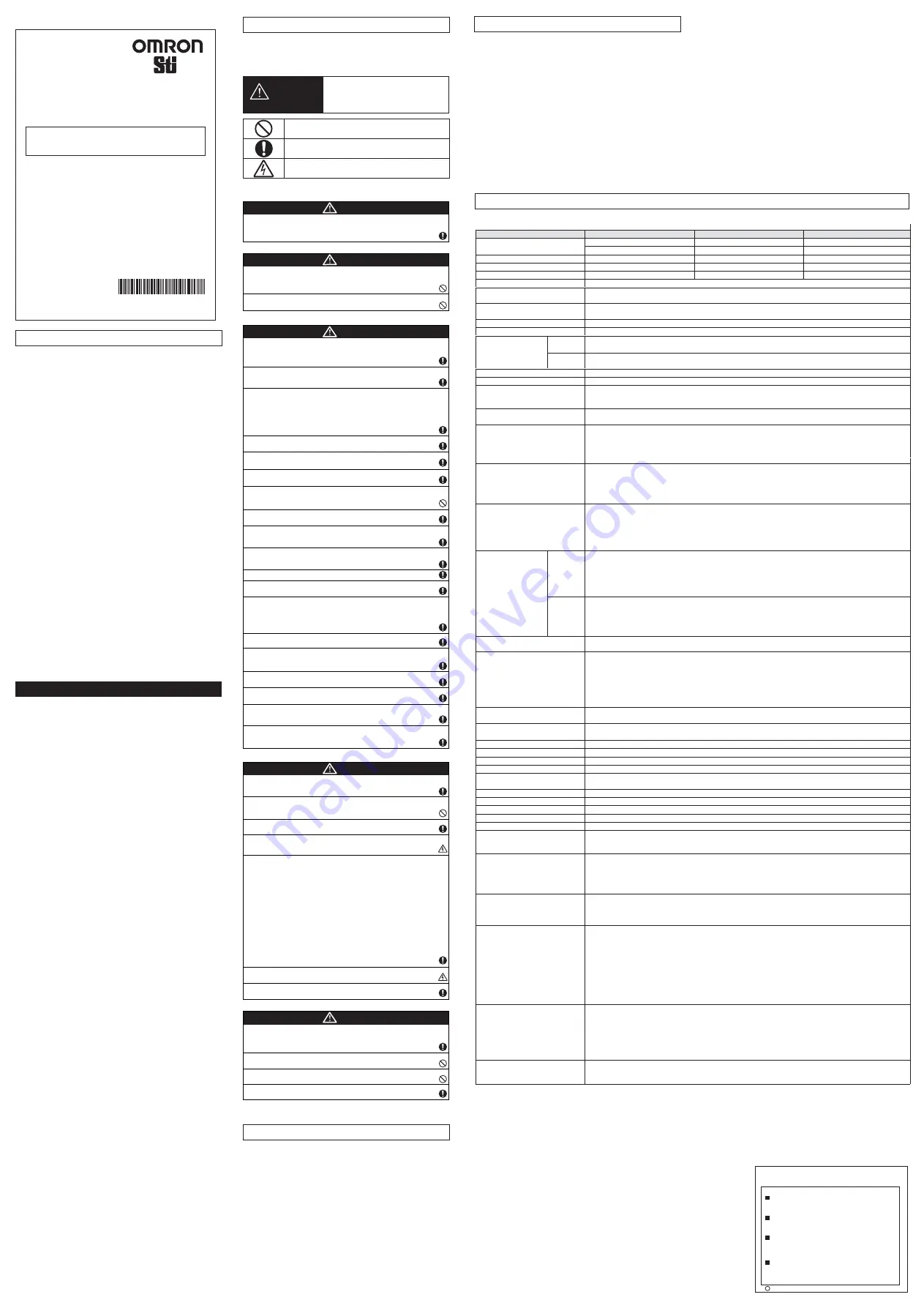
SAFETY LIGHT CURTAIN
Model
F3SJ-A
□□□□
P
□□
-TS
1. Application of a F3SJ sensor alone cannot receive type approval provided by
Article 44-2 of the Labour Safety and Health Law of Japan. It is necessary to
apply it in a system. Therefore, when using the F3SJ in Japan as a "safety
system for pressing or shearing machines" prescribed in Article 42 of that
law, the system must receive type approval.
2. The F3SJ is electro-sensitive protective equipment (ESPE) in accordance with
European Union (EU) Machinery Directive Index Annex V, Item 2.
3. EC Declaration of Conformity
OMRON declares that F3SJ is in conformity with the requirements of the
following EC Directives:
Machinery Directive 2006/42/EC
EMC Directive 2014/30/EU
4. F3SJ is in conformity with the following standards:
(1) European standards
EN61496-1 (Type 4 ESPE), EN 61496-2 (Type 4 AOPD), EN61508-1
through -3 (SIL3), EN ISO 13849-1:2015 (Category 4, PL e)
(2) International standards
IEC61496-1 (Type 4 ESPE), IEC61496-2 (Type 4 AOPD), IEC61508-1
through -3 (SIL3), ISO 13849-1:2015 (Category 4, PL e)
(3) JIS standards
JIS B 9704-1 (Type 4 ESPE), JIS B 9704-2 (Type 4 AOPD)
(4) North American Standards:
UL61496-1(Type 4ESPE), UL61496-2(Type 4AOPD), UL508, UL1998,
CAN/CSA C22.2 No.14, CAN/CSA C22.2 No.0.8
5. The F3SJ received the following approvals from the EU accredited body,
TÜV SÜD Product Service GmbH:
Ć
EC Type-Examination in accordance with the EU Machinery Directive,
Type 4 ESPE (EN61496-1), Type 4 AOPD (EN 61496-2)
Ć
TÜV SÜD Product Service Type Approval, Type 4 ESPE (EN61496-1),
Type 4 AOPD (EN 61496-2), SIL1, 2, 3 (EN61508-1 through -3), EN ISO
13849-1:2015 (Category 4, PL e)
6. The F3SJ received the certificates of UL listing for US and Canadian safety
standards from the Third Party Assessment Body UL.
•Both are: Type 4 ESPE (UL61496-1), Type 4 AOPD (UL61496-2)
7. The F3SJ is designed according to the standards listed below. To make sure that the
final system complies with the following standards and regulations, you are asked
to design and use it in accordance with all other related standards, laws, and
regulations. If you have any questions, consult with specialized organizations
such as the body responsible for prescribing and/or enforcing machinery safety
regulations in the location where the equipment is to be used.
•European Standards: EN415-4, EN692, EN693
•U.S. Occupational Safety and Health Standards: OSHA 29 CFR 1910.212
•U.S. Occupational Safety and Health Standards: OSHA 29 CFR 1910.217
•American National Standards: ANSI B11.1 to B11.19
•American National Standards: ANSI/RIA 15.06
•Canadian Standards Association CSA Z142, Z432, Z434
•SEMI Standards SEMI S2
•Ministry of Health, Labour and Welfare "Guidelines for Comprehensive
Safety Standards of Machinery", Standard Bureau's Notification No. 501
dated June 1, 2001.
© OMRON Corporation
2006-2020
All Rights Reserved.
LEGISLATION AND STANDARDS
Alert Statements in this Manual
INSTRUCTION SHEET
Regarding the alert symbols and meani ngs used for the safe uses
In order for our customers to use the F3SJ in safety, precautions are indicated in
this manual with the alert symbols and statements such as the followings. Those
safety precautions relate to the important descriptions that must be obeyed for
the safe uses and operations. Be sure to obey the precautions. The following
indictions and symbols are used for the descriptions.
The F3SJ must be installed, configured, and incorporated into a machine
control system by a sufficiently trained and qualified person. An unqualified
person may not be able to perform these operations properly, which
may cause a person to go undetected, resulting in serious injury.
Do not use this sensor for machines that cannot be stopped by electrical
control. For example, do not use it for a pressing machine that uses
full-rotation clutch. Otherwise, the machine may not stop before a
person reaches the hazardous part, resulting in serious injury.
Make sure to test the operation of the F3SJ after installation to verify that
the F3SJ operates as intended. Make sure to stop the machine until the test
is complete. Unintended function settings may cause a person to go
undetected, resulting in serious injury.
Install a protective structure so that the hazardous part of a machine can only
be reached by passing through the sensor's detection zone. Install the sensors
so that part of the person is always present in the detection zone when
working in a machine's hazardous areas. If a person is able step into the
hazardous area of a machine and remain behind the F3SJ's detection zone,
configure the system with an interlock function that prevents the machine
from being restarted. Failure to do so may result in serious injury.
Do not use the auxiliary output or external indicator output for safety applications.
Human body may not be detected when F3SJ fails, resulting in serious injury.
Make sure to install the F3SJ at the safe distance from the hazardous part of
the equipment. Otherwise, the machine may not stop before a person
reaches the hazardous part, resulting in serious injury.
Install the interlock reset switch in a location that provides a clear view of the entire
hazardous area and where it cannot be activated from within the hazardous area.
The F3SJ cannot protect a person from an object flying from a hazardous
area. Install protective cover(s) or fence(s).
Use independent 2 input devices for muting inputs.
You must install F3SJ, muting sensor, and physical barrier so that an
operator should not enter hazardous zone.
The muting and override functions disable the safety functions of the device.
You must ensure safety using other method when these functions are operating.
Install muting sensors so that they can distinguish between the object that is being
allowed to pass through the detection zone and a person. If the muting function
is activated by the detection of a person, it may result in serious injury.
Muting lamps (external indicators) that indicate the state of the muting and
override functions must be installed where they are clearly visible to
workers from all the operating positions.
Install the sensor system so that it is not affected by the reflective surface
of the F3SJ.
Make sure that the F3SJ is securely mounted and its cables and connectors
are properly connected.
Make sure that foreign material such as water, oil, or dust does not enter
the F3SJ or the connector while the cap is removed.
When using more than 1 set of F3SJ, install them so that mutual
interference does not occur, such as by configuring series connections or
using physical barriers between adjacent sets.
Do not use the sensor system with mirrors in a retro-reflective
configuration. Doing so may hinder detection. It is possible to use mirrors
to "bend" the detection zone to a 90-degree angle.
Perform an inspection for all F3SJ as described in "Chapter 5 Checklists" of
User’s manual. When using series connections,perform inspections for
every connected F3SJ.
Connect the load between the output and 0V line (PNP output). Connecting
the load between the output and +24V line will result in a dangerous
condition because operation is reversed to ON when blocked.
Do not short-circuit the output line to the +24V line. Otherwise, the output
is always ON. Also, the 0V of the power supply must be grounded so that
output does not turn ON due to grounding of the output line.
Configure the system by using the optimal number of safety outputs that
satisfy the requirements of the necessary safety category.
Do not connect each line of F3SJ to a DC power supply of more than
24VDC+20%. Also, do not connect to an AC power supply. Failure to do
so may result in electric shock.
Double or reinforced insulation from hazardous voltage must be applied to all
input and output lines. Failure to do so may result in electric shock.
Do not try to disassemble, repair, or modify this product. Doing so may
cause the safety functions to stop working properly.
Do not use the F3SJ in environments where flammable or explosive
gases are present. Doing so may result in explosion.
Perform daily and 6-month inspections for the F3SJ. Otherwise,
the system may fail to work properly, resulting in serious injury.
Extension of the cable must be within a specified length. If it isn't, safety
function may not work properly, resulting in danger.
To use the F3SJ in PSDI mode (Reinitiation of cyclic operation by the
protective equipment), you must configure an appropriate circuit between the
F3SJ and the machine. For details about PSDI, refer to OSHA1910.217,
IEC61496-1, and other relevant standards and regulations.
For the F3SJ to comply with IEC 61496-1 and UL 508, the DC power
supply unit must satisfy all of the following conditions:
• Must be within the rated power voltage (24V DC ± 20%)
• Must have tolerance against the total rated current of devices if it is
connected to multiple devices
• Must comply with EMC directives (industrial environment)
• Double or reinforced insulation must be applied between the primary and
secondary circuits
• Automatic recovery of overcurrent protection characteristics (reversed L
sagging)
• Output holding time must be 20ms or longer
• Must satisfy output characteristic requirements for class 2 circuit or
limited voltage current circuit defined by UL508
• Must comply with laws and regulations, regarding EMC and electrical
equipment safety, of the country or region where the F3SJ is used (Ex: In
EU, the power supply must comply with the EMC Directive and the Low
Voltage Directive.)
PRECAUTIONS ON SAFETY
Make sure to observe the following precautions that are necessary for
ensuring safe use of the product.
• Thoroughly read this manual and understand the installation procedures,
operation check procedures, and maintenance procedures before using the
product.
• Loads must satisfy both of the following conditions:
-Not short-circuited
-Not used with a current that is higher than the rating
• Do not drop the product.
• Dispose of the product in accordance with the relevant rules and regulations
of the country or area where the product is used.
PRECAUTIONS FOR SAFE USE
•When extending the communication line with a cable (twisted-pair wire)
other than the dedicated cable (F39-JD
□□
), use a cable with the same or
superior specification. Connect the shield to the 0V line.
•When replacing the cable connectors with other types of connectors, use
connectors that provide a protection grade of IP54 or higher.
•Properly perform the wiring after confirming the signal names of all the
terminals.
•Do not operate the control system until 2 seconds or more (2.2 seconds or
more in case of series connection) after turning ON the power of the F3SJ.
•Be sure to route the F3SJ cable separate from high-potential power lines or
through an exclusive conduit.
•When using a commercially available switching regulator power supply,
make sure to ground the FG terminal (frame ground terminal).
•Install the emitter and receiver so that their vertical direction should match.
•If the protective height is 600 mm or more, use intermediate mounting
brackets of specified quantities and locations according to the dimensions.
If the brackets described above are not used, ratings and performance cannot
be not met.
•Sharing the power supply with other devices may cause the F3SJ to be
affected by noise or voltage drop. It is recommended that the F3SJ use a
dedicated power supply but do not share with other devices.
■
Cleaning
Do not use thinner, benzene, or acetone for cleaning, because they affect the
product's resin parts and paint on the case.
■
Object detection
The F3SJ cannot detect transparent and/or translucent objects.
■
Wiring and installation
•Make sure to perform wiring while the power supply is OFF. Otherwise, the
F3SJ may fail to operate due to the diagnosis function.
•Do not short-circuit output lines to +24V line. Otherwise a fault of F3SJ may
occur.
RATINGS
Indicates a potentially hazardous situation
which, if not avoided, will result in minor or
moderate injury, or may result in serious
injury or death. Additionally there may be
significant property damage.
WARNING
WARNING
WARNING
WARNING
WARNING
WARNING
For Users
■
Ratings/Specifications
In the type names in this table, the
□□□□
contain the 4 digits indicating the protective height (mm).
For Machines
For Installation
For Wiring
Other
Detection capability
Opaque objects
F3SJ-A
□□□□
P20-TS
Diameter 20mm
Beam gap
15mm
Number of beams
16 to 166
Protective height
245 to 2,495mm
Lens diameter
Diameter 5mm
Operating range
0.2 to 9m (for protective height up to 1649 mm)
0.2 to 7m (for protective height 1655 mm or greater)
Response time
ON to OFF: 10ms to 27.5ms max., OFF to ON: 40ms to 110ms max. (when incidence is stable).
Refer to the reverse side for details.
Startup waiting time
2s max. (2.2s max in case of series connection)
24VDC ± 20% (ripple p-p10% max.)
Power supply voltage(Vs)
Current
consumption
(no load)
Emitter
Up to 50 beams: 76 mA max., 51 to 100 beams: 106 mA max., 101 to 150 beams: 130 mA max., 151 to 200
beams: 153 mA max., 201 to 234 beams: 165 mA max.
Receiver
Up to 50 beams: 68 mA max., 51 to 100 beams: 90 mA max., 101 to 150 beams: 111 mA max.,151 to 200
Light source
Infrared LED (870nm wavelength)
Within ±2.5 ° for the emitter and receiver at a detection distance of at least 3 m according to IEC61496-2
beams: 128 mA max., 201 to 234 beams: 142 mA max.
Effective aperture angle (EAA)
Safety outputs(OSSD)
PNP transistor outputs x 2, Load current 300mA max, Residual voltage 2V max. (except for voltage drop due
to cable extension)(including inductance load), Maximum capacity load 2.2
μ
F, Leakage current 1 mA max.
(This may be different from previously used logic (ON/OFF) because safety circuit is used.)
output)
Auxiliary output 1 (Non-safety
PNP transistor output x 1, Load current 300mA max., Residual voltage 2V max. (except for voltage drop due
to cable extension), Leakage current 1mA max.
External indicator output
(Non-safety output)
Connectable external indicator
- Incandescent lamp : 24VDC, 3 to 7W
- LED lamp : Load current 10 to 300mA.
external indicator.)
Leakage current 1mA max.(An indicator cable F39-JJ3N or F39-A01P
□
PAC is required when using an
Output operation mode
Safety outputs : ON when receiving light
Auxiliary output 1 : Reverse output of safety output
muting system)
External indicator output 1: Reverse output of safety output (for basic system), ON during muting/override (for
External indicator output 2: ON in lockout (for basic system), ON during muting/override (for muting system)
Input voltage
Indicators
Test input, Reset input, and Muting input:
ON voltage: 9V to Vs* (short-circuit current: approx. 2.0mA)
OFF voltage: 0 to 1.5V, or open
External relay monitoring input is:
OFF voltage: open
*The Vs indicates a voltage value in your environment.
ON voltage: 9V to Vs* (short-circuit current: approx. 3.5mA)
Emitter
Error mode indicators (red LED x 3): Blink to indicate error details
Incident light level indicators (green LED x 2, orange LED x 3): ON based on the amount of incident light
Power indicator (green LED x 1): ON while power is ON
Lockout indicator (yellow LED x 1): Blinks when in lockout
External device monitoring indicator [muting input 1 indicator],
Test indicator [muting input 2 indicator] (green LED x2): ON/Blink according to function
Receiver
Error mode indicators (red LED x 3): Blink to indicate error details
Incident light level indicators (green LED x 2, orange LED x 3): ON based on the amount of incident light
OFF-state indicator (red LED x 1): ON when safety outputs are OFF/ Blinks when in lockout
Muting error indicator, Test indicator (green LED x 2): ON/Blink according to function
ON-state indicator (green LED x 1): ON when safety outputs are ON
Mutual interference prevention
function
Series connection
Time division emission by series connection
- Number of connections: Up to 3 sets
- Total number of beams: Up to 240
- Cable length between sensors: 15 m max. (not including series connection cable (F39-JJR*L or F39-JJR3W) and power cable)
Lockout occurs when:
- Number of connected sensors or total number of beams of them exceed the limits described above
- Other sensor than -TS type is attached to the series connection
- Self-test (After power ON, and during operation)
- External test (light emission stop function by test input)
- External device monitoring
- Muting (Includes override functions. F39-CN6 key cap for muting is required)
Interference light avoidance algorithm
Test function
Safety-related functions
Connection method
Protection circuit
Connector method (M12, 8-pin)
During operation: 35 to 85%RH (no condensation), During storage: 35 to 95%RH
During operation: -10 to 55°C (without freezing), During storage: -30 to 70°C
Ambient temperature
Output short-circuit protection, and power supply reverse polarity protection
Ambient humidity
Ambient light intensity
of 10,000 Ix max.
Incandescent lamp: receiving-surface light intensity of 3,000 Ix max., Sunlight: receiving-surface light intensity
Insulation resistance
20M
Ω
or higher (500VDC)
Dielectric strength voltage
1, 000VAC, 50/60Hz, 1min
Degree of protection
IP65 (IEC60529)
Dia. 6 mm, 8-wire (0.15mm
2
x 8) with braided shield, Allowable bending radius R5mm
Malfunction: 100m/s
2
, 1,000 times each in X, Y, and Z directions
Vibration resistance
Malfunction: 10 to 55Hz, Multiple amplitude of 0.7mm, 20 sweeps each in X, Y, and Z directions
Shock resistance
Connection cable, Series
connection cable (F39-JJR
□
L,
JJR3W)
Extension cable
(F39-JD*A, JD*B,JC*C)
bending radius of R36mm.
(To extend a cable, use an equivalent or higher-performance cable (twisted-pair wire) , and do not use the
Dia. 6.6 mm, 8-wire (0.3mm
2
x 4P, conductor resistance 0.058 ohm/m), with braided shield,Allowable
cable in the same duct as that for high-voltage cables or power cables)
For details about extension lengths ( Power Cable Length), refer to next page
Material
Cap: ABS resin
Cable: Oil resistant PVC
- F3SJ-A
□□□□
P20-TS/F3SJ-A
□□□□
P25-TS
Weight (g)=(protective height) x 1.5+
α
Casing (including metal parts on both ends): Aluminum, zinc die-cast
Optical cover: PMMA resin (acrylic)
Weight (packaged)
The values for
α
are as follows:
When protective heightis between 245 and 596mm,
α
=1100
When protective heightis between 600 and 1,130mm,
α
=1500
When protective heightis between 1,136 and 1,658mm,
α
=2000
When protective heightis between 1,660 and 2,180mm,
α
=2400
When protective heightis between 2,195 and 2,500mm,
α
=2600
Accessories
instruction sheet, top and bottom mounting brackets, intermediate mounting brackets (*), error
* The number of intermediate mounting brackets depends on the total length of the F3SJ.
- F3SJ total length is from 600 to 1,130mm: 1 set for each the emitter and receiver is included
- F3SJ total length is from 1,136 to 1,658mm: 2 sets for each the emitter and receiver are included
- F3SJ total length is from 1,660 to 2,180mm: 3 sets for each the emitter and receiver are included
- F3SJ total length is from 2,195 to 2,500mm: 4 sets for each the emitter and receiver are included
mode label, Quick Installation Manual(QIM)
Applicable standards
IEC61496-1, EN61496-1, UL61496-1 Type 4ESPE (Electro-Sensitive Protective Equipment)
IEC61496-2, EN 61496-2, UL61496-2 Type 4AOPD (Active Opto-electronic Protective Devices) IEC61508,
EN61508 SIL3, EN ISO 13849-1:2015 (Category 4, PL e), ISO 13849-1:2015 (Category 4, PL e)
Opaque objects
F3SJ-A
□□□□
P25-TS
Diameter 25mm
20mm
13 to 125
260 to 2,500mm
Opaque objects
F3SJ-A
□□□□
P14-TS
Diameter 14mm
9mm
26 to 234
245 to 2,117mm
- F3SJ-A
□□□□
P14-TS
Weight (g)=(protective height) x 1.7+
α
Original instructions
Observe the precautions described below to prevent operation failure,
malfunctions, or undesirable effects on product performance.
■
Installation environment
Do not install the F3SJ in the following types of environments:
•Areas exposed to intense interference light, such as direct sunlight
•Areas with high humidity where condensation is likely to occur
•Areas where corrosive gases are present
•Areas exposed to vibration or shock levels higher than in the specification
provisions
•Areas where the product may come into contact with water
•Areas where the product may get wet with oil that can solve adhesive
Do not use radio equipment such as cellular phones, walkie-talkies, or
transceivers near the F3SJ.
This is a class A product. In residential areas it may cause radio interference.
in which case the Responsible Person may be required to take adequate
measures to reduce interference.
PRECAUTIONS FOR CORRECT USE
②
Indicates prohibited actions.
Indicates mandatory actions.
Indicates the risk of electric shock.
You must ensure that the system works as you intended after configuring
floating blanking.Failure to do so may result in serious injury.
Warning zone output is non-safety output. You must not include it to
calculation of safety distance. Otherwise safety distance may be reduced,
resulting in serious injury.
A switch to activate the override function must be a hold-to-run device such
as a spring return key switch and must be installed in a location that
provides a clear view of the entire hazardous zone and where it cannot be
activated from within the hazardous zone.Make sure that nobody is in the
hazardous area before activating the override function.
Omron Companies shall not be responsible for conformity with any standards,
codes or regulationswhich apply to the combination of the Product in the BuyerÊ
s application or use of the Product. At BuyerÊ s request, Omron will provide
applicable third party certification documents identifying ratings and limitations
of use which apply to the Product. This information by itself is not sufficient for
a complete determination of the suitability of the Product in combination with
the end product, machine, system, or other application or use. Buyer shall be
solely responsible for determining appropriateness of the particular Product with
respect to BuyerÊ s application, product or system. Buyer shall take application
responsibility in all cases.
NEVER USE THE PRODUCT FOR AN APPLICATION INVOLVING
SERIOUS RISK TO LIFE OR PROPERTY OR IN LARGE QUANTITIES
WITHOUT ENSURING THAT THE SYSTEM AS A WHOLE HAS BEEN
DESIGNED TO ADDRESS THE RISKS, AND THAT THE OMRON
PRODUCT(S) IS PROPERLY RATED AND INSTALLED FOR THE
INTENDED USE WITHIN THE OVERALL EQUIPMENT OR SYSTEM.
Suitability for Use
Please read and understand this instruction sheet before
storing, installing, programming, operating, maintaining, or
disposing of the products. Please consult your OMRON
representative if you have any questions or comments.
Please refer to the User's Manual and the Quick Installation
Manual for detailed instructions on usage.
OMRON Corporation (Manufacturer)
Contact: www.ia.omron.com
Regional Headquarters
Shiokoji Horikawa, Shimogyo-ku, Kyoto, 600-8530 JAPAN
OMRON EUROPE B.V. (Importer in EU)
Wegalaan 67-69, 2132 JD Hoofddorp
The Netherlands
Tel: (31)2356-81-300/Fax: (31)2356-81-388
OMRON ELECTRONICS LLC
2895 Greenspoint Parkway, Suite 200
Hoffman Estates, IL 60169 U.S.A.
Tel: (1) 847-843-7900/Fax: (1) 847-843-7787
OMRON ASIA PACIFIC PTE. LTD.
No. 438A Alexandra Road # 05-05/08 (Lobby 2),
Alexandra Technopark,
Singapore 119967
Tel: (65) 6835-3011/Fax: (65) 6835-2711
OMRON (CHINA) CO., LTD.
Room 2211, Bank of China Tower,
200 Yin Cheng Zhong Road,
PuDong New Area, Shanghai, 200120, China
Tel: (86) 21-5037-2222/Fax: (86) 21-5037-2200
t
F e b , 2 0 2 0
F
*
7
9
2
8
4
2
0
-
8
K
*